как изготовить станок для уплотнения старых изделий из ПЭТ и другого пластика, технология сборки, материалы

В эпоху, когда идеи для создания бизнеса рождаются с нуля, особенно актуальной является работа с различного рода пластиковыми отходами, например, с бутылками.
Их перерабатывают в различные изделия, а иногда просто останавливаются на этапе сбора и сбыта пустой использованной тары.
Но в любом случае актуальным остается вопрос их транспортировки и хранения.
Облегчить различные манипуляции с этой объемной тарой может помочь пресс для пластиковых бутылок.
Его не обязательно покупать, можно изготовить самостоятельно.
Технология и материалы
Прежде чем определиться с конструкцией и, соответственно, с количеством необходимых материалов, нужно понимание, где пресс будет стоять. От высоты потолка в помещении напрямую зависят габариты оборудования.
Нет смысла самому изготавливать высокомощные прессы для пластика, поскольку цена работы и закупаемых запчастей практически приравнивается к стоимости промышленного станка.
Преимущества самостоятельной сборки:
- экономия денежных средств: иногда очень актуальна, особенно в организации небольшого бизнеса;
- доступные материалы, которые есть даже в самых отдаленных городах;
- нет расходов по транспортировке и установке тяжелого оборудования, он собирается непосредственно на месте;
- пресс изготавливается строго под свои задачи, размер и плотность упаковки кипы зависит от пожелания.
Если нет опыта в работе с металлом и сваркой, лучше обратиться к специалисту, поскольку в профессиональных мастерских есть весь необходимый инструмент.
Ниже рассмотрим технологию сборки пресса для пластиковых бутылок с ручным управлением, но с достаточной мощностью загрузки до 30 кг.
Технические характеристики
Вот основные из них:
- Высота — определяющий типоразмер. Он зависит от размера рычага гидроцилиндра. В данном исполнении он может варьироваться от 1,5 до 3-х метров.
- Размер плит и, следовательно, остальных габаритов зависит от ширины плит пресса.
- Площадь станины — ориентировочно составляет от 1 до 1,5 метров.
- Мощность электродвигателя. Целесообразно установить движок 380 Вольт, но можно и 220 Вольт. Мощность определяет скорость сведения-разведения плит пресса.
- Вес кипы или брикета. В принципе, количество загружаемого материала зависит напрямую от физических возможностей оператора, какой конкретно вес способен поднять человек в постоянном режиме работы. Данная модель предполагает упаковку кипы бутылок массой до 25 кг.
- Размеры кипы — зависят от размеров плит. Оптимальное значение по ширине — 300-400 мм. Толщина зависит от веса. Бутылки — не очень удобный материал для прессования, они скользят и выпирают. Поэтому брикет может выглядеть раздутым и неаккуратным.
Необходимые материалы
Вот то, без чего не обойтись при создании пресса для пластиковых бутылок своими руками:
- Узел гидравлики. Из чего он будет состоять, зависит от предполагаемой мощности и габаритов. Если это мини-пресс, то достаточно просто гидравлического цилиндра от домкрата. Но в таком случае качество спрессованного материала будет зависеть от силы рук оператора, поскольку он не существенно увеличивает усилие ручного труда. Если пресс нужен более мощный, то потребуется: насос масляный, соединительные трубки, масляный распределитель и цилиндры.
- Электроника. Двигатель (можно взять даже модель б/у), пускатель и небольшой щиток управления.
- Листовой металл и балки (швеллеры, уголки и т.д.).
Оборудование для работы
Понадобятся такие агрегаты:
- дрель электрическая;
- болгарка и набор дисков по металлу;
- сварочный аппарат и комплект электродов.
Может возникнуть проблема с подключением электронной системы управления двигателем, поэтому, если нет соответствующего опыта, лучше найти опытного КИПовца. Для него это работа пяти минут.
Чертеж и схема изготовления
Для того чтобы начать работу, необходимо определиться с тем, как установить гидроцилиндры. То есть, какая из плит будет подвижной — верхняя или нижняя. От этого зависит место крепления гидравлического узла и, собственно, чертеж.
Ниже приведена схема с классическим (и более простым) расположением цилиндра.
Этапы сборки пресса для ПЭТ бутылок своими руками:
- Изготовление станины. Целесообразнее первым изготовить именно каркас, к которому затем будут крепиться остальные узлы. Металлические уголки желательно выбирать с существенным запасом по прочности, поскольку помимо веса остальных элементов, каркасу необходимо выдерживать и постоянные нагрузки при спрессовывании брикетов. Основание выполняется плоским прямоугольной формы. Для усиления конструкции его можно дополнительно укрепить стальными или чугунными плитами. В габаритах рамки определяющим размером является высота. Она складывается из размеров гидравлического цилиндра, толщины ходовой плиты и неподвижной части (стола), а также от предполагаемого размера подъема верхней части плиты.
- Крепление гидравлического узла. Согласно чертежу, цилиндр или домкрат установлен на основании корпуса. Подвижная часть цилиндров закрепляется снизу на подвижной плите, через нее передавая усилие смыкания на материал. На одинаковом расстоянии по обе стороны закрепляют пружины. Их задача — плавное возвращение пресса в исходное состояние.
- Подвижная часть стола. Она изготавливается из подвижного основания, которое по ширине исполняется чуть меньше расстояния между опорами станины. Через трубку оно приваривается (или закрепляется) к штоку домкрата. Сверху к основанию закрепляется плита подвижной части стола. Ее можно усилить рамной конструкцией.
- Неподвижная часть (плунжер). По своим габаритам равна движущейся части, приваривается на закрепленную рамку в верхней части станины.
- Электродвигатель и пускатель. Устанавливаются на подвижном столе. Крепление пускателя определяется местом положения поршня. Двигатель перекачивает масло, то есть приводит в движение масляный насос.
- Дополнительные отверстия на раме. Выполняются для регулирования положения неподвижной плиты. То есть, передвигая ее вверх или вниз, можно увеличивать или уменьшать размер прессуемой кипы.
Сферы применения
Помимо работы с ПЭТ бутылками, такие самодельные прессы могут применяться для уплотнения:
Они могут быть полезны в:
- Магазинах и кафе. Количество упаковочного материал в этих объектах колоссально. Необходимо решение для организации их хранения.
- Небольших цехах. Различные товары и сырье упаковывается в коробки и пакеты, которые тоже нужно как-то складывать и перевозить.
- Пунктах приема макулатуры, ветоши и другого объемного вторсырья.
Когда необходим промышленный пресс?
Если речь идет о небольших объемах ПЭТ бутылок, которые необходимо спрессовать, то вполне достаточно самостоятельно изготовленного станка.
Для крупных промышленных предприятий и пунктов приема пластиковых бутылок такой станок вряд ли будет подходящим, поскольку они отличаются небольшой производительностью и высокой степенью задействования рабочей силы.
С большим потоком материала он просто не справится, поскольку здесь уже необходимо выгодное соотношение между скоростью работы и количеством спрессованного материала.
Также фактором, который способен склонить выбор в пользу промышленного оборудования, является запас прочности. Несомненно, качество сварных швов и прочность металла напрямую определяют срок службы станка.
Прочитать о прессах для пластиковых отходов промышленного производства вы можете в здесь.
Полезное видео
В данном видео автор показывает, как изготовить пресс для старых бутылок и картона своими руками:
Итог
Пресс не относится к сложному и наукоемкому оборудованию, поэтому для его изготовления вполне достаточно простых материалов, доступных по цене.
Схем для его изготовления предложено масса и их можно найти в свободном доступе. Поэтому изготовление пресса своими руками — это действительно путь к экономии материальных ресурсов. Польза от его установки вполне очевидна.
Возможно, вас также заинтересует информация о переработке ПЭТ бутылок в домашних условиях.
Вконтакте
Google+
Одноклассники
Переработка пластика в домашних условиях: способы, оборудование, видео
Пластмассовые изделия стали неотъемлемой частью нашей жизни, поэтому сегодня тема переработки пластика в домашних условиях приобрела особую значимость. Рециклинг пластмасс, даже осуществляемый в собственном доме, вносит свою лепту в защиту окружающей среды от огромных куч почти не разлагаемых пластиковых (полимерных) отходов.
Какой пластик можно переработать самому?
Основа всех пластиков – полимеры (соединения, имеющие высокую молекулярную массу и состоящие из мономеров). Возможность переработки пластмасс зависит от типа сырья, из которого сделано пластиковое изделие. В наши дни существует множество видов пластика, которые, однако, можно объединить в две большие группы:
- Термопластик. Из этого материала производится примерно 80% пластиковой продукции. Включает виды: ПНД, ПВД, ПЭТ, ПП, ПС, ПВХ и др.
- Термореактивный пластик. Представлен полиуретаном, эпоксидной, фенольными смолами и т.д.

Переработать второй тип пластмасс в домашних условиях невозможно, т.к. термореактивный пластик не поддается повторному плавлению (в некоторых случаях на предприятиях он подвергается измельчению и использованию в виде наполнителя).
Термопластики же при нагревании плавятся без потери начальных свойств и, охлаждаясь, вновь приобретают исходную форму. Именно поэтому «дома» можно осуществлять переработку только термопластичных пластмасс с помощью специального, но «нехитрого» оборудования и получать из таких пластиковых отходов новые полезные изделия и материалы.
Наиболее распространенным перерабатываемым сырьем являются ПЭТ-бутылки и другая пластмассовая тара.
Каждый пластик уникален по своему, от структуры до утилизации. На нашем сайте про каждый вид пластика, как отход, написаны исчерпывающие статьи, почитать, которые можно по следующим ссылкам: полиэтилен низкого давления, полиэтилен высокого давления, полиэтиленовая пленка, полиэтилентерефталат, полипропилен, полистирол, поливинилхлорид, поликарбонат.
Чтобы понять, из какого вида пластика выполнено изделие, нужно обратить внимание на маркировку, нанесенную на его поверхности (часто на дне)
Что нужно для переработки в домашних условиях?
Промышленные аппараты, перерабатывающие пластик, дорогие и требуют больших площадей. Безусловно, такие агрегаты не подходят для реализации идеи переработки пластмассовых отходов в домашних условиях. Чтобы получать из ненужной пластмассы новые изделия кустарным способом, потребуется самостоятельно сконструировать несколько специальных машин.
Следуя проекту Precious Plastic
Для переработки пластика «своими руками» понадобятся следующие устройства (или одно из них в зависимости от поставленной цели):
- Шредер. Измельчает полимерные отходы с получением крошки заданного размера, которая затем подвергается дальнейшей обработке. Аппарат включает несколько основных компонентов: измельчающую часть, загрузочную воронку, станину и источник тока. Наиболее трудоемким этапом в изготовлении устройства является производство измельчающего элемента, состоящего из вала с «нанизанными» на него лезвиями. Загрузочный бункер делается из листового металла (здесь также могут идти в ход отходы, например, старые автомобильные части). Нужный размер получаемой пластиковой фракции задается с помощью сетки, установленной под измельчающую часть.
- Устройство для сжатия (пресс). На пластиковую крошку, загружаемую в аппарат, воздействуют большое давление и высокая температура, результатом процесса является получение новых спрессованных пластмассовых изделий самых разных форм. Основные элементы устройства: печь, станина, пресс и электроника.
- Инжектор («впрыскиватель»). Принцип работы данного устройства заключается в том, что под воздействием высокой температуры пластиковая крошка плавится до текучей массы, которая затем впрыскивается в какую-либо форму. После того, как пластмассовая масса остывает, получаются новые твердые предметы небольших размеров.
- Экструдер. Нагретая пластиковая масса подвергается продавливанию через канал устройства, в результате процесса пластик выходит из аппарата в форме нитей. С помощью экструдера можно получать пластиковые гранулы.

Линия по переработке пластика от проекта Precious Plastic.
Чертежи для сборки всех этих устройств можно скачать бесплатно на сайте preciousplastic.com. Там же можно просмотреть видео-инструкции, в которых наглядно и доступно рассказывают о технологиях создания аппаратов, необходимых материалах и последовательности действий.

Проект Precious Plastic является международным. Его создатель Дейв Хаккенс усовершенствовал найденные в Интернете чертежи устройств по переработке полимеров и, применив свои знания, сконструировал эффективные аппараты, позволяющие легко получать новые изделия из пластмассовых отходов. Проект помогает простому человеку создавать машины, перерабатывающие пластик, и с их помощью извлекать выгоду не только для себя, но и для окружающей среды.
Также рекомендуем почитать интересную статью про виды оборудования для переработки пластмасс в промышленных масштабах. В статье подробно рассмотрены все основные типы оборудования, от дробилок и шредеров до целых линий по переработке пластика в гранулы. А также раскрыт такой важный вопрос, как выбор необходимого оборудования для начала бизнеса на пластиковых отходах.
Простой механизм для резки бутылок из пластика
Суть работы данного резака заключается в том, что он отрезает от края пластиковой бутылки (по ее окружности) нити, имеющие определенную толщину. Результат достигается благодаря зафиксированному лезвию, скользящему по изделию из пластика. Процесс не требует электрической энергии, устройство состоит лишь из держателя и непосредственно резака.
Из полученных своими руками пластиковых нитей можно создавать различные предметы интерьера, корзинки и иные объекты, на которые у человека хватит фантазии.
Несколько слов о технике безопасности
Переработка пластмассы в домашних условиях не требует сверхъестественных знаний по технике безопасности. При плавлении пластика стоит вооружиться огнеупорными перчатками (можно использовать сварочные краги), чтобы избежать ожогов.
Также при работе с пластиковыми изделиями важно знать, что их нельзя подвергать сжиганию, т.к. некоторые виды пластмасс, сгорая, выделяют в среду токсичные соединения.
Безусловно, лучше, если измельчение пластмассовых отходов, их плавление и т.д. будет происходить в специально отведенном для этого месте, например в гараже. Не стоит забывать и о безопасности во время изготовления устройств по переработке пластикового сырья. Здесь также необходимо использовать индивидуальные средства защиты:
- специальные очки при резке металла;
- сварочную маску при сварке;
- брезентовые или кожаные перчатки.
Как расплавить пластик в домашних условиях?
Расплавить отходы пластмасс в домашних условиях можно с помощью одного из описанных ранее устройств (пресса, инжектора, экструдера). Однако их создание требует определенных навыков и времени.

Можно прибегать к плавлению пластмассы, используя более примитивные способы. Например, для получения пластикового винтового барашка можно соорудить металлический шприц и твердую пресс-форму.
Описание процесса
В качестве сырья можно использовать полипропилен (маркировка «РР»). Измельченный материал закладывается в изготовленный шприц и утрамбовывается металлическим поршнем. Наполненный пластиком шприц помещается в обычную духовку примерно на 30 мин при температуре 220-240оС.
Затем расплавленная пластмассовая масса выдавливается из шприца в подготовленную пресс-форму, при этом в течение некоторого времени нужно произвести выдержку материала под давлением. После остывания из формы можно извлекать готовое изделие.
Полезное видео о переработке
Умельцы производят из ненужного пластика самые разные изделия. О том, как может осуществляться литье пластмассы в условиях дома с получением винтового барашка, смотрите в данном видео:
Расплавить несколько пластиковых крышек от бутылок можно с помощью строительного фена. Процесс формовки полезных небольших изделий из пластика представлен в следующем видео:
Выгода
Основная выгода самостоятельной переработки пластика состоит в том, что из ненужных и дешевых материалов получаются новые изделия, имеющие широкое применение в быту и других сферах нашей жизнедеятельности.

Соорудив специальное оборудование, можно организовать небольшой бизнес, основанный на изготовлении и продаже материалов для последующей обработки (например, флекса) или готовых к употреблению предметов (пластиковой посуды, плетеной мебели и т.д.).
Промышленная утилизация пластика связана с решением множества задач. Переработать пластмассовые отходы в домашних условиях значительно легче. Важно лишь поставить себе цель и определиться с направлением переработки. А сконструировать перерабатывающие пластик устройства любой сложности можно с помощью «всезнающего» Интернета.
Устройство для литья пластика (экструдер)


В этой статье рассмотрим, как изготовить экструдер. Но сначала давайте, что такое экструдер и экструзия.
Экструдер — это машина для непрерывной переработки полимерного сырья в однородный расплав и придания ему формы путём продавливания через экструзионную головку и специальное калибрующее устройство.
Экструзия (технологический процесс) — метод и процесс получения изделий из полимерных материалов путём продавливания расплава материала через формующее отверстие в экструдере.
Говоря простым языком, в камере устройства пластмасса расплавляется и под давлением выдавливается через сопло головки в пресс-форму.
Инструменты и материалы:
-Металлическая труба с резьбой на конце;
-Головка торцевая;
-Удлинитель для головки;
-Сварочный аппарат;
-УШМ;
-Тиски;
-Напильник;
-Перфорированный уголок;
-Два уголка-кронштейна;
-Медная трубка;
-Крепеж;
-Металлический хомут;
-Нагревательный элемент;
-Терморегулятор с датчиком;
-Стекловолокно;
-Алюминиевый скотч;
-Фитинги;
-Металлическая полоса;
-Угольник;
-Дрель;
Шаг первый: поршень
Камеру экструдера будет из металлической трубы 20 мм. Внутренняя стенка трубы должна быть ровная без шва. Внутрь камеры будет закладываться пластик, нагреваться и выдавливаться через сопло. Для выдавливания нужен поршень. Поршень мастер изготовил из торцевой головки. Подобрал головку по диаметру трубки. Установил ее на удлинитель. Приварил головку к удлинителю. Заварил торцевое отверстие головки.

Шаг второй: камера
На одном конце трубы имеется резьба. На противоположном конце делает загрузочное окно. Размечает и вырезает стенку трубы. Зачищает края напильником. Через прорезь будет загружаться пластик в камеру.
На резьбу накручивает переходную муфту.
Шаг третий: нагревательный элемент
Теперь нужно установить на камере нагревательный элемент. Мастер использует два нагревательных элемента по 400 Вт. Из перфорированного уголка делает крепление. Закрепляет нагреватели металлическими хомутами. Между уголками устанавливается медная трубка. В трубку устанавливается термодатчик.
Шаг четвертый: термоизоляция
Обматывает устройство стекловолокном. Поверх стекловолокна наматывает металлический скотч. Термоизоляция предотвратит потери тепла и защитит от случайного прикосновения.

Шаг пятый: установка
Из уголка мастер сделал рамку для крепления экструдера. Закрепил устройство на раме.


Шаг шестой: сопло
Роль сопла в экструдере играет латунный переходник. Вкручивает переходник.
Шаг седьмой: рычаг
Теперь нужно изготовить рычаг. Сначала мастер удлиняет толкатель поршня.
Закрепляет уголки на раме. К уголкам крепит поперечную трубу. К поперечине присоединяет трубу с прорезью. Берет еще один отрезок трубы. Один конец сплющивает (он крепиться в прорези предыдущего элемента), второй конец соединяет со штоком поршня. Все соединения подвижные.

Шаг восьмой: испытание аппарата
Сначала нужно прогреть камеру выше температуры плавления пластика на 2-3 градуса. Затем загрузить измельченный пластик в камеру. Небольшое наличие дыма в начале — это нормально, если дыма много и он идет постоянно нужно снизить температуру.
Работать с экструдером необходимо в хорошо проветриваемом помещении, используя средства защиты.
Источник
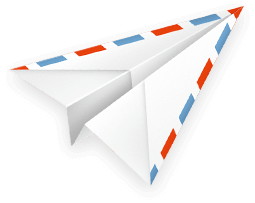
Получайте на почту подборку новых самоделок. Никакого спама, только полезные идеи!
*Заполняя форму вы соглашаетесь на обработку персональных данных
Становитесь автором сайта, публикуйте собственные статьи, описания самоделок с оплатой за текст. Подробнее здесь.Литье пластмасс в силикон — доступное мелкосерийное производство в домашних условиях
Многие из тех, кто печатает на 3D-принтере сталкиваются или с необходимостью получить партию моделей в короткие сроки, или скопировать удачно получившуюся деталь, или получить изделия с прочностными характеристиками, превосходящими таковые у пластиков для домашней 3d-печати.3D-принтер далеко не всегда способен выполнить такие задачи, но отлично подойдет для создания единственного образца, или мастер-модели. А дальше на помощь нам приходят материалы производства компании Smooth-On, наверное, самого популярного производителя материалов холодного отверждения.
В этом обзоре мы сравним самые основные и популярные силиконы, полиуретаны и добавки к ним, кратко посмотрим на основные способы создания форм и изделий, подумаем, где это может найти применение и, наконец, создадим свою силиконовую форму и модель.
Перед написанием этого поста мы прошли трехдневный тренинг у официального дилера Smooth-On в России, чтобы разобраться во всех тонкостях литья в силикон.
Обзор процесса
Процесс создания изделий методом литья практически всегда одинаков: создаем модель, с её помощью создаем силиконовую форму, заливаем в нее материал, получаем изделие. Но в зависимости от модели, необходимых свойств, количества отливок, каждый этап может кардинально меняться. Существует несколько способов как создания формы, так и готового изделия.
Пару слов о подготовке моделей, напечатанных на 3D-принтере. Компания Smooth-On обратила своё внимание на эту технологию и выпустила специальный лак под названием XTC-3D. Он прекрасно сглаживает характерные для напечатанных моделей огрехи, видимые слои, которые обязательно перейдут на силиконовую форму, и придает поверхности гладкость и глянцевый вид.
Подробный обзор XTC 3D Вы можете прочитать здесь.
Методы создания форм
• Сплошная заливка
Самый простой способ: модель помещается в опалубку (специальную герметичную емкость из обычного оргстекла, пластика или другого материала), фиксируется в ней и заливается силиконом. Хорошо подходит для простых двухмерных моделей, рельефов, сувенирной и брендинговой продукции.
• Разрезная форма
Аналогичен предыдущему, только модель размещается с учетом того, что форма будет разрезаться полностью или частично для облегчения съема. Модель может быть подвешена с помощью проволоки или размещена на тонкой опоре. Способ предназначен для более сложной геометрии, технических изделий, сложных фигур.
• Двухсоставная форма
Это один из самых сложных способов. Заключается в помещении модели на глиняную или пластилиновую основу, которая делит силиконовую форму пополам.
На основе размещаются специальные замки, которые будут обеспечивать точное совмещение двух форм и отсутствие смещений. Вокруг основы собирается опалубка, герметизируется горячим клеем или пластилином, и в неё заливается первая половина формы. Затем, после отверждения силикона, форма переворачивается, глина или пластилин счищаются, силикон покрывается разделительным составом, и заливается вторая половина формы.
• Метод «в намазку»
Этим методом создаются так называемые «чулочные» формы, когда силикон точно повторяет форму объекта и имеет толщину от 3 мм до нескольких сантиметров. Для создания формы «в намазку» необходим достаточно вязкий силикон, который бы не стекал с модели.
Можно использовать как специально предназначенные для этого силиконы, называемые тиксотропными, так и обычные, но модифицированные с помощью загустителей.
Силикон наносится кисточкой или шпателем в несколько слоёв, в которых чередуется вязкость и скорость отвердевания, чтобы форма была максимально детализированной и прочной. После того, как все слои готовы, с помощью специального состава создается жесткая внешняя оболочка, которая будет держать форму.
Методы заливки пластиков
Самый простой метод заключается в обычной заливке пластика в форму, он подходит для домашнего использования и позволяет достичь приемлемого качества. Но, по необходимости, для более качественного результата возможно использование установок высокого давления, что позволит практически полностью убрать пузырьки воздуха.
Для этого форма вместе с залитым пластиком помещается в камеру, в которой создается повышенное до 4 атмосфер давление. Форма должна оставаться в камере все время отвердевания полиуретана. При таком давлении пузыри уменьшаются до почти невидимых глазу размеров, что значительно повышает качество изделия.
Еще один метод, так называемая заливка «в обкатку», используется для создания полых изделий. В форму заливается небольшое количество пластика, около 10% от общего объема, отверстие для заливки закрывается, и начинается вращение формы по всех плоскостях, вручную или на специальной ротационной машине. При этом пластик отвердевает на стенках формы, создавая полую модель, что позволяет существенно снизить вес изделия и экономить материал.
Обзор силиконов
• Серия Mold Star 15, 16, 30
Силиконы для создания форм на основе платины. Застывают при комнатной температуре, образуют прочную, гибкую и очень детализированную форму. Предназначены для литья силикона, полиуретана, смол, полиэстера, воска и других материалов. Химически чувствительны и не способны работать с латексом, серой и некоторыми другими соединениями.
Самые базовые и основные силиконы, способные решать большинство задач. Цифра в названии отражает твердость по шкале Шор А. Обладает низкой вязкостью, что позволяет в большинстве случаев работать без оборудования для дегазации. Материал двухкомпонентный, части смешиваются в удобном соотношении 1:1 по объему. В основном предназначены для создания форм методом сплошной заливки.
• Серия Rebound 25, 40
Серия силиконов для создания форм методом «в намазку», который состоит в том, чтобы наносить силикон кистью или шпателем на поверхность модели. Обладает высокой вязкостью, возможностью модификации свойств с помощью загустителей и ускорителей для создания качественной многослойной формы. Двухкомпонентный, смешивается в соотношении 1:1 по объему.
• Серия Equinox 35, 38, 40
Силиконовые пасты с временем жизни 1, 4 и 30 минут. Предназначены для ручного смешивания, по консистенции напоминают густое тесто. Цифры соответствуют твердости по Шору А. Обладает крайне высокой прочностью на разрыв и долговечностью. В отвержденном состоянии является безопасным для заливки шоколада, карамели и других ингридиентов.
• Серия SortaClear 18, 37, 40
Серия полупрозрачных силиконов. Такая особенность, как оптическая прозрачность, используется для создания сложных разрезных форм — изделие прекрасно просматривается, что позволяет сделать точный разрез. Как и серия Equinox, является безопасным при контакте с пищевыми продуктами.
Также к силиконам существует большое количество добавок, обладающих самыми разными эффектами. Accel-T и Plat-Cat являются ускорителями отверждения, Slo-jo — увеличивает время жизни силикона, Thi-Vex увеличивает вязкость силикона и позволяет намазывать его кистью или шпателем на модель, Silc-Pig — это концентрированные пигменты для окрашивания.
Обзор полиуретанов
• Серия Smooth-Cast
Самая основная и популярная серия полиуретанов для создания конечных изделий. Линейка включает в себя более 10 наименований различных пластиков с самыми разными свойствами, позволяющими подобрать материал именно для Вашего проекта. Например, Smooth-Cast 300 обладает коротким временем жизни в 3 минуты и временем отверждения в 10 минут, что позволяет быстро воспроизводить большие партии деталей. Smooth-Cast 305 аналогичен предыдущему, но «живет» уже 7 минут, что позволяет провести дегазацию смешанных компонентов и получить еще более качественное изделие. ONYX обладает глубоким черным цветом, которого не достичь с помощью красителей, 65D ROTO предназначен для создания полых моделей с помощью метода «в обкатку», 325 незаменим для точного воспроизведения цвета, 385 отверждается практически без усадки и максимально точно копирует изделие.
• Серия TASK
Серия полиуретанов специального назначения. Разработана для промышленного применения и обладает специфическими свойствами для конкретных задач.
Для Вашего удобства мы сформировали специальные фильтры по сферам применения:
• Пищевые:
Smooth-Sil 940, серия Sorta Clear, серия Equinox, TASK 11.
• Архитектурные, заливка бетона и других абразивных материалов:
Серия VytaFlex, серия Brush-On, серия Ez-Spray, серия PMC.
• Медицинские: симуляция тканей и органов
Серия Dragon Skin, добавки Slacker, Ecoflex 0030, Ecoflex Gel, Body Double.
• Прототипирование:
Практически любые полиуретаны и силиконы, в зависимости от задач и требований. Серии Mold Max, Mold Star, Smooth-Cast, TASK.
• Спецэффекты и грим:
Skin Tite, Body Double, Dragon Skin, Alja-Safe, Ecoflex, Soma Foama, Rubber Glass, Encapso K.
Стоит отметить, что это деление все же условное, и дано, чтобы примерно представить возможности широкого ассортимента компании Smooth-On.
Обзор процесса
Мы будем использовать только те материалы и оборудование, которые можно применить в домашних условиях. Мы попробуем создать самую сложную в изготовлении двухсоставную форму.
Нам понадобятся:
• Платиновый силикон Mold Star 30
• Заливочный полиуретан Smooth-Cast 300
• Лак для 3D-моделей XTC-3D
• Упаковка виниловых перчаток
• Несколько одноразовых пластиковых стаканчиков
• Емкости для смешивания
• Термоклеевой пистолет
• Материал для опалубки (пластиковые панели)
• Скульптурная глина
• Несколько малярных кистей
В роли мастер-модели выступит модель довольно популярного среди печатников тестового болта. Мы распечатали его черным PLA пластиком на Picaso 3D Designer с толщиной слоя 100 микрон. Сделали мы это специально для того, чтобы продемонстрировать эффект XTC 3D, поскольку далеко не каждый 3D принтер может печатать с качеством 50 микрон.
Далее — обработка, чтобы отлитая модель не переняла слоистость напечатанного объекта. Обрабатываем болт лаком XTC-3D (подробнее об этом процесс можно прочитать тут), а затем шкурим, чтобы получить гладкую матовую поверхность.
Теперь модель готова к заливке силиконом. Помещаем её на глиняную основу, с помощью которой мы создадим силиконовую форму из двух частей.
Модель должна быть погружена в глину ровно наполовину, так что начинаем процесс выравнивания глины. Края должны быть максимально ровными и полностью прилегать к модели, от этого зависит качество разделения силиконовых половинок. Убираем лишнюю глину и заключаем модель в пластиковую опалубку.
Все стыки пластика обрабатываем термоклеевым пистолетом и закрываем опалубку, окончательно обрабатываем глиняную основу, делаем в ней выемки для замков.
Все готово к заливке силикона. Поскольку двухкомпонентные силиконы и полиуретаны склонны к разделению на фракции, перед каждым использованием их необходимо тщательно перемешивать в емкости.
После перемешивания отмеряем равное количество двух компонентов по объему и приступаем к смешиванию.
Для данной марки силикона дегазация в вакуумной камере необязательна, что очень удобно: исключены появления пузырьков, которые могут испортить нашу форму. Медленно заливаем силикон в опалубку, в самую нижнюю её точку.
И оставляем застывать. Время застывания для этой марки силикона составляет 6 часов. По истечении этого времени освобождаем модель от опалубки.
Затем убираем глину, тщательно очищаем модель от её остатков, смазываем силикон разделительным составом. В случае его отсутствия, можно использовать и обычный вазелин, но качество будет немного хуже.
И дальше полностью повторяем процесс, заливая вторую половину силиконовой формы.
Спустя еще 6 часов силиконовая форма готова. С помощью лезвия аккуратно разъединяем половинки, вынимаем деталь и оцениваем, что у нас получилось.
Хорошо видны замки, закладывавшиеся в глиняной основе, хорошая детализация, несмотря на то, что разделительная линия проходила по довольно сложным местам, вроде вдавленных букв.
На самом деле, для данной модели это не самый оптимальный способ создания формы. Но нам было интересно протестировать именно этот метод, несмотря на сложности.
Итак, все готово к заливке полиуретана. Соединяем две половинки формы, используя элементы опалубки для жесткости, скрепляем с помощью резинок, скотча или другим способом, и приступаем к подготовке полиуретана.
Хорошо перемешиваем оба компонента, встряхивая их в течение 5-10 минут. После этого даем немного отстояться, чтобы вышли образовавшиеся пузыри. Все остальное точно так же, как и с силиконом: отмеряем равное количество по объему и смешиваем их. А дальше действовать нужно быстро: время жизни этого полиуретана составляет всего 3 минуты, а время начинает идти сразу, как вы смешали два компонента вместе. Так что мешаем быстро, но аккуратно, чтобы не создавать лишних пузырьков, и сразу заливаем в форму.
Примерно через 3 минуты, в зависимости от объема материала, произойдет быстрое схватывание пластика, а через 10 минут деталь готова к извлечению.
Модель готова. Переданы абсолютно все детали оригинала.
Заключение
Хочется отметить, что поистине огромные возможности использование материалов Smooth-On открывает в совокупности с 3D-печатью.
Теперь Вы можете получать изделия из огромного количества материалов с самыми различными свойствами, а не ограничиваться лишь классическими PLA и ABS. К тому же, доступным станет мелкосерийное производство: распечатав всего один экземпляр и должным образом его обработав, Вы сможете в довольно короткие сроки создать необходимое Вам количество копий в домашних условиях. Для достижения приемлемого результата вовсе не обязательно использование дорогостоящего оборудования.
В случае если Вам необходимы услуги мелкосерийного производства Top 3D Shop к вашим услугам.
разновидности, технология процесса, стоимость наиболее популярных моделей

На крупных предприятиях по вторичной переработке пластиковых отходов, на сортировочных заводах и даже в небольших цехах постоянно возникает вопрос хранения и транспортировки пластикового вторсырья.
Особенно это касается ПЭТ бутылок, канистр и другой объемной тары.
Они занимают много места, достаточно накладны в перевозке и существенно ухудшают санитарные условия.
Поэтому прессование является актуальным технологическим решением для уплотнения пластиковой тары.
В данной статье пойдет речь о прессовом оборудовании, его актуальной стоимости и особенностях работы с ним.
Предназначение прессов для ПЭТ бутылок
По своему функционалу прессы для пластиковых бутылок мало чем отличаются от остальных. Но есть существенное отличие – это наличие камеры для защиты от выпадения сырья из рабочей зоны.
Иногда можно встретить агрегаты с прямоугольными или округлым защитным корпусом.
Основные функции:
- формируют кипы и брикеты;
- экономят место для хранения;
- облегчают транспортировку;
- экономят деньги на перевозке и хранении.
Виды
Прессы для ПЭТ бутылок можно разделить по нескольким параметрам.
По способу сжатия
По способу приложения сжимающего усилия на плиты прессы бывают:
- Горизонтального исполнения. Основное преимущество — это возможность установки данного типа оборудования с высокой производительностью в помещениях с невысокими потолками. Помимо пластиковых бутылок, подходит для уплотнения всех основных видов вторичного сырья — ветошь, бумага, картон, алюминий, пленки и т.д. Размеры кип уплотненного материала зависят от габаритов агрегата и его производительности. Горизонтальные прессы для ПЭТ бутылок, как правило, устанавливаются на высокопроизводительных линиях сортировки отходов. Они удачно вписываются в технологическую цепочку благодаря возможности автоматического управления процессом прессования.
- Вертикального исполнения. Более распространенный вариант благодаря широкой вариации габаритных размеров и способов исполнения управления приводным механизмом. Такого типа пресс можно встретить и на кустарном мини-заводе, и на крупном предприятии. Агрегаты такого вида отличаются относительной доступностью и удобством работы. Объем и масса упакованного материала зависит от габаритов плит и от усилия смыкания.
По виду привода
Бывают такими:
- Механический. Подходят для уплотнения небольших брикетов, где требуется небольшое усилие замыкания и короткое время его приложения.
- Гидромеханический. Плиты приводятся в движение рычажным механизмом. Он позволяет реализовать плавный ход пресса. На старте, когда это необходимо, скорость плит большая, а сила замыкания маленькая. И наоборот, в рабочем цикле скорость сведения плит небольшая при значительных усилиях.
- Гидравлический. Самый распространенный вид. Их основное преимущество перед первыми двумя видами заключается в том, что сила давления плит не зависит от скорости их движения. Они позволяют получать кипы любого размера и формы, в зависимости от габаритов и производительности.
По типу управления
Виды:
- Ручное. Применяется исключительно в оборудовании с механическим приводом и при небольшом усилии прессования.
- Полуавтоматическое. Достаточно распространенный тип для оборудования с ручной загрузкой. После заполнения камеры агрегата сырьем оператор приводит в движение плиты машины.
- Автоматическое. Такое исполнение можно встретить на заводах с большим потоком. Прессы в таком случае оборудуются автоматической загрузкой с конвейера.
По производительности
Здесь деление очень условное, поскольку размеры готовых брикетов и их вес напрямую зависят от размеров оборудования и усилия его смыкания.
Главный ориентир при выборе пресса для пластиковых бутылок – это планируемый объем перерабатываемого вторичного сырья.
То есть на стадии закупки оборудования должно быть понимание примерного потока сырья. Для мусороперерабатывающих заводов и пунктов сбора отходов оптимальным значение является вес кипы от 90 до 300 килограмм.
Необходимо закладывать небольшой коэффициент запаса по мощности (примерно 25%).
Технология процесса
Итак, как прессуют ПЭТ-бутылки? На первый взгляд ничего сложного здесь быть не может. Но на практике все же возникают некоторые трудности. Основная проблема – это закрытые крышками ёмкости. При сжимании воздуху просто некуда деться.
Если речь идет о крупном заводе с мощным прессовым оборудованием, то проблем нет. Усилие смыкания плит настолько велико, что бутылка просто разрывается.
Но если же предстоит работать на маломощном агрегате, то следует провести подготовку:
- Проткнуть ножом или острым предметом тару. Такая операция подходит для станков, которые имеют малую производительность и загружаются в ручную.
- Полностью удалить крышки с бутылок. Трудоемкий процесс. Актуален только при наличии большого количества дешевой рабочей силы. Некоторые переработчики при приемке сырья заведомо оговаривают наличие или отсутствие крышек на бутылках. Есть интересный ход – только частично открутить крышку, буквально на 2-3 оборота, для выхода воздуха.
- Установка дополнительного оборудования – перфоратора. Эта машина представляет из себя прокатные ролики, оборудованные шипами. При прохождении через них бутылка прокалывается в нескольких местах, через которые затем выходит воздух.
В кустарных цехах по сбору вторичного пластика рабочие перед загрузкой пресса дополнительно сжимают бутылки, наступив на них ногой. Так загрузка машины увеличивается, а на прессах с ручным управлением таких нехитрым способом можно повысить плотность упаковки отходов.
Как изготовить пресс своими руками?
Для организации работы небольшого цеха по сбору пластиковых бутылок можно самостоятельно изготовить пресс.
Для этого потребуются следующие материалы:
- металлические балки для изготовления рамной конструкции и опор;
- гидравлический насос — подойдет даже обычный домкрат;
- плиты металлические для изготовления рабочей части станка;
- электрический двигатель;
- листовой металл для изготовления корпусной части.
Принцип работы такого пресса основан на усилении ручного воздействия при помощи гидравлического цилиндра и поршня.
Производительность такого станка будет определятся силой сжимания, которую обеспечивает гидроцилиндр.
Размер брикета определяют геометрические параметры камеры. В интернете можно найти массу схем по сборке пресса самостоятельно. В частности, статья об изготовлении пресса для пластиковых бутылок своими руками есть на нашем сайте.
Стоимость
Изготовление прессов не относится к высокотехнологичным производствам, поэтому очень удачные модели можно встретить и у российских производителей. К тому же, зачастую такие станки очень массивные и тяжелые, транспортировка из зарубежных стран может быть накладной.
Ниже рассмотрим цену наиболее популярных моделей прессов для пластиковых бутылок с гидравлическим управлением:
Кроме того, можно найти объявления о продаже б/у оборудования на соответствующих платформах.
Видео по теме
Предлагаем посмотреть, как прессуют ПЭТ бутылки на специальном оборудовании:
Вывод
Пресс — это простое, но в то же время необходимое оборудование, которое помогает существенно упростить работу с объемными пластиковыми бутылками.
При относительно небольших денежных вложениях экономия достигается колоссальная.
Вконтакте
Google+
Одноклассники
Как сделать очень простой и компактный гидравлический пресс из шприцов своими руками!

Всем доброго времени суток! В сегодняшней статье я бы хотел поделиться с вами очень интересной и даже возможно кому-то полезной самоделкой, а именно сегодняшняя статья будет посвящена гидравлическому прессу своими руками! Данный пресс хоть и очень простой и ни имеет ни какой электроники, но он все равно очень эффективный. Имея небольшие размеры его можно использовать в быту для своих нужд. К примеру этот пресс может спокойно расколоть грецкий орех или сдавить алюминиевую банку. Самоделка очень интересная так что не будем тянуть.
И так просто гидравлического пресса понадобится:
-ровные деревянные доски, толщиной 2-3 см
-капельница
-три разветвителя для капельницы
-две маленькие трубочки
-6 шприцов
-двойник для капельницы
-палочки от мороженого
-болты
Из инструментов также понадобится:
-термо клей
-электро лобзик
-канцелярский нож
-скотч
-шестигранник
-электро дрель
И так первым делом необходимо сделать разметку на доске таким образом чтобы получилось 3 квадрата по 15 см с каждой стороны и 2 прямоугольника со сторонами 38 см и 15 см. После его берём электролобзик и вырезаем заготовочки следующим образом:
Возьмём электро дрель и с помощью сверла под ваши винты или саморезы сверлим 18 отверстий на расстоянии 3,5 мм в общем так как показано на фото:

Теперь меняем обычное сверло на перьевое и делаем 8 сквозных отверстий так как показано на фото:
Начинаем сборку конструкции.
Для этого с помощью саморезов скрепляем две длинные и одну квадратную дощечку следующим образом:
Берём два шприца и у одного с помощью канцелярского ножа отрезаем переднюю часть, а у второго заднюю часть:

Соединяем оба шприца с помощью скотча, можно все это дело укрепить с помощью холодной сварки или супер клея, главное чтобы было герметично и крепко:
Теперь для «мега» шприца нужно сделать поршень аналогичным способом: у одного отрезаем переднюю часть, а у второго заднюю, соединяем обе половинки с помощью термо клея и делаем укрепление места соединения кусочками от палочки от мороженого:


Тестируем. Герметичность очень важна!

Берём трубочку от капельницы и отрезаем от неё отрезок длиной 10 см, после его надеваем на «носик» мега шприца:

Всего нужно сделать 4 таких вот заготовочек, после чего вставляем их в квадратную дощечку с самыми большими отверстиями:

На поршни наносим термо клей и на них приклеиваем небольшой брусочек как можно ровнее, тем самым получается единый большой поршень который и будет выступать в роли давящего поршня:
Возьмём другую квадратную дощечку и вставим «мега» поршень тонкими трубочками в неё вот таким вот образом:

После чего вставляем его в предыдущую заготовку, так чтобы совпали отверстия под саморезы, вставляем уже упомянутые саморезы в отверстия и закручиваем с помощью шестигранника:
Теперь необходимо взять два разветвителя для капельницы и надеть их так как показано на фото:


Затем нужно сделать два клапана:
Берём маленькую бусинку такого размера чтобы она была чуть больше диаметра «носика» шприца, после чего берём оставшиеся передние части шприцов и склеиваем их в месте так как показано на фото, заранее положив внутрь бусинку:


Теперь необходимо собрать всю гидравлику, для этого соединяем капельницу с клапанами и шприцом через разветвитель вот таким вот образом:
Берём два небольших брусочка и склеиваем их так как показано на фото:

Приклеиваем шприц поршнем вверх, как можно ровнее:


Теперь берём стакан с обычной водой и окрашиваем в тот цвет который вам нравится, автор видео покрасил в голубой, как по мне этот цвет смотрится лучше всего:
Один конец гидравлики опускаем в стакан с покрашенной водой, а второй конец в пустой стакан:

Заполняем всю эту конструкцию водой с помощью шприца, стакан который в начале был пустой должен наполниться, после его наполнения нужно перелить жидкость обратно в первый стакан:
Берём обе конструкции и соединяем трубочки от капельниц всё тем же разветвителей, должно получиться так как показано на фото, после этого можно украсить пресс подписав его:


Ну вот и все! Самодельный мини гидравлический пресс готов и осталось только его протестировать, для этого кладём к примеру орех под поршень и начинаем перекачивать воду с помощью маленького шприца в мега поршень, при этом он начинает двигаться и сдавливает орех. После чего просто отодвигаем поршень назад и достаем орешек. Также данный пресс спокойно может раздавить алюминиевую банку из под газировки. Можно экспериментировать и с другими предметами и даже подсчитать его мощность и силу давления на предмет главного поршня.
Думаю можно увеличить мощность пресса путем увеличения количества «мега» шприцов либо увеличением объема этих самых шприцов.
Вот подробное видео от автора по сборке и испытанным данной самоделки:
Ну и всем спасибо за внимание!
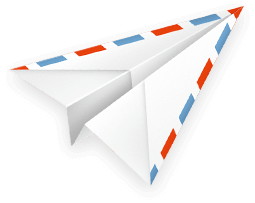
Получайте на почту подборку новых самоделок. Никакого спама, только полезные идеи!
*Заполняя форму вы соглашаетесь на обработку персональных данных
Становитесь автором сайта, публикуйте собственные статьи, описания самоделок с оплатой за текст. Подробнее здесь.