НихромПродукция Описание Цены Стандарты Статьи Фото ФехральПродукция Описание Цены Стандарты Статьи Фото Нихром в изоляцииПродукция Цены Стандарты Статьи Фото ТитанПродукция Описание Цены Стандарты Статьи Фото ВольфрамПродукция Описание Цены Стандарты Статьи Фото МолибденПродукция Описание Цены Стандарты Статьи Фото КобальтПродукция Описание Цены Стандарты Статьи Фото Термопарная проволокаПродукция Описание Цены Стандарты Статьи Фото Провода термопарныеПродукция Цены Стандарты Статьи Фото НикельПродукция Описание Цены Стандарты Статьи Фото МонельПродукция Описание Цены Стандарты Статьи Фото КонстантанПродукция Описание Цены Стандарты Статьи Фото МельхиорПродукция Описание Цены Статьи Фото Твердые сплавыПродукция Описание Цены Стандарты Статьи Фото Порошки металловПродукция Цены Стандарты Статьи Фото Нержавеющая стальПродукция Описание Цены Стандарты Статьи Фото Жаропрочные сплавыОписание Цены Стандарты Статьи Фото ФерросплавыПродукция Описание Цены Стандарты Статьи Фото ОловоПродукция Описание Цены Стандарты Статьи Фото ТанталПродукция Описание Цены Стандарты Статьи Фото НиобийПродукция Описание Цены Стандарты Статьи Фото ВанадийПродукция Описание Цены Стандарты Статьи Фото ХромПродукция Описание Цены Стандарты Статьи Фото РенийПродукция Описание Цены Стандарты Статьи Фото
Основные сведения о жаростойких и жаропрочных сплавахЖаропрочные сплавы и стали — материалы, работающие при высоких температурах в течение заданного периода времени в условиях сложно-напряженного состояния и обладающие достаточным сопротивлением к коррозии в газовых средах.Активный интерес к подобным материалам стал проявляться в конце 30-х годов XX века, когда появилась необходимость в материалах способных работать при достаточно высоких температурах. Это связано с развитием реактивной авиации и газотурбинных двигателей. Основой жаростойких и жаропрочных сплавов могут быть никель, кобальт, титан, железо, медь, алюминий. Наиболее широкое распространение получили никелевые сплавы. Они могут быть литейными, деформируемыми и порошковыми. Наиболее распространенными среди жаропрочных являются литейные сложнолегированные сплавы на никелевой основе, способные работать до температур 1050-1100 °C в течение сотен и тысяч часов при высоких статических и динамических нагрузках. Классификация жаропрочных и жаростойких сплавовПоскольку речь идет о жаростойких и жаропрочных сталях и сплавах, то стоит дать определение терминам жаропрочность, жаростойкость.Термины и определенияЖаропрочность — способность сталей и сплавов выдерживать механические нагрузки при высоких температурах в течение определенного времени. При температурах до 600°С обычно применяют термин теплоустойчивость. Можно дать более строгое определение жаропрочности.Ползучесть — явление непрерывной деформации под действием постоянного напряжения. Длительная прочность — сопротивление материала разрушению при длительном воздействии температуры. Жаростойкость характеризует сопротивление металлов и сплавов газовой коррозии при высоких температурах. КлассификацияМожно выделить несколько классификаций сплавов и сталей, которые работают при повышенных и высоких температурах.Наиболее общей является следующая классификация жаростойких и жаропрочных сталей и сплавов:
Свойства жаростойких и жаропрочных сплавовДля жаропрочных сплавов и сталей основным полезным свойством с практической точки зрения является способность материала выдерживать механические нагрузки в условиях высоких температур. Существуют различные схемы нагружения жаропрочных материалов: статические растягивающие, изгибающие или скручивающие нагрузки, термические нагрузки вследствие изменений температуры, динамические переменные нагрузки различной частоты и амплитуды, динамическое воздействие скоростных газовых потоков на поверхность. При этом указанные материалы должны выдерживать соответствующий тип нагружения.В то же время, с точки зрения производства готовых изделий важную роль играют технологические свойства. При создании деформируемых сплавов необходимо обеспечить достаточную технологическую пластичность при обработке давлением, в том числе при температурах 700-800 °С, а литые сплавы должны иметь удовлетворительные литейные свойства (жидкотекучесть, пористость). Марки жаропрочных и жаростойких сплавовЖаропрочные стали и сплавы на никелевой основеВ настоящее время сплавы на никелевой основе имеют наибольшее значение в качестве жаропрочных материалов, предназначенных для работы при температурах от 700 до 1100°С.Сплав ХН77ТЮР (ЭИ437Б и ЭИ437БУВД)
Сплав ХН70ВМТЮ (ЭИ617) Химический состав по ГОСТ 5632-72, % (по массе): 13-16 Cr; 2-4 Мо; 5-7 W; 0,1-0,5 V; 1,8-2,3 Ti; 1,7-2,3 Al; ; остальное никель. Технологические данные:
Жаростойкие стали и сплавы на основе никеля и железаОсновными жаростойкими материалами, которые используют в газовых турбинах, печах и различного рода высокотемпературных установках с рабочей температурой до 1350 °С, являются сплавы на основе железа и никеля. Высокое сопротивление окислению сталей и сплавов связано в первую очередь с большим количеством хрома, входящего в состав сплавов. Например, максимальное содержание хрома (по массе) в количестве 26-29 % имеет сплав на основе никеля ХН70Ю.Сплав ХН70Ю (ЭИ652) Технологические данные:
Химический состав по ГОСТ 5632-72, % (по массе): 19-22 Cr; Технологические данные:
Химический состав по ГОСТ 5632-72, % (по массе): 23,5-26,5 Cr; 13-16 W; Технологические данные:
Химический состав по ГОСТ 5632-72, % (по массе): 14,5-16,5 Cr; 15-17 Mo; 3-4,5 W; Полуфабрикаты из указанных сплавов подвергаются термической обработке, которая заключается в закалке при температуре 1050-1090 °С и последующем охлаждении в воде. Применяются для сварки конструкций, работающих при повышенных температурах в достаточно агрессивных средах (серная, уксусная кислота, хлориды и др.). Высоколегированные сталиСталь СВ-06Х15Н60М15 (ЭП367)Химический состав по ГОСТ 2246-70, % (по массе): 14-16 Cr; 14-16 Mo; Указанная сталь не относится к категории жаропрочных или жаростойких, но используется для сварки конструкций из таких сплавов. Она применяется для сварки деталей из сплавов на никелевой основе, например, ХН78Т, ХН70ВМЮТ и подобных, а также для сварки разнородных металлов, например, хромистых сталей со сплавами на никелевой основе. Помимо сварки может осуществляться наплавка. Достоинства / недостатки жаростойких и жаропрочных сплавов
Области применения жаропрочных И жаростойких сплавовУказанные материалы применяются при изготовлении деталей ракетно-космической техники, в газовых турбинах двигателей самолетов, кораблей, энергетических установок, в нефтехимическом оборудовании. К таким деталям можно отнести рабочие лопатки, турбинные диски, кольца и другие элементы газовых турбин, а также камеры сгорания, узлы деталей печей и прочих изделий, длительно работающих при повышенных температурах. Диапазон рабочих температур, как правило, составляет 500-1350 °С. Полуфабрикаты из некоторых сплавов используются в качестве присадочного материала при сварке. Продукция из жаростойких и жаропрочных сплавов |
виды, свойства, применение :: SYL.ru
Технологические процессы производства, а также эксплуатация тепловых агрегатов нередко подразумевают использование огнеупоров. Необходимость такого решения обусловлена требованиями к изоляции и защите целевых объектов. Обычно применяются специальные материалы, выполненные на основе минерального сырья. К использованию допускаются огнеупорные изделия, наделенные достаточными свойствами температурного противодействия, которые регулируются нормативами.
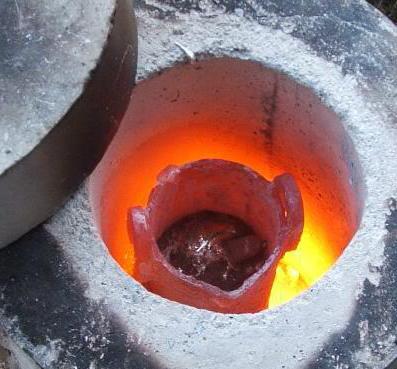
Основные свойства и характеристики огнеупоров
Целый комплекс физических качеств материала рассматривается с точки зрения его поведения под действием высоких температур. Огнеупорность является ключевым свойством, определяющим эффективность применения конкретного изделия. Она выражается в температурном пороговом значении, при достижении которого начинается процесс деформации. Минимальное значение для материалов такого типа составляет 1580 °C. Для сверхогнеупорных материалов это значение превышает 3000 °C. Также учитывается свойство деформации под нагрузкой. Оно указывает уже на механическую целостность изделия, которое находится под влиянием высоких температур. По этой характеристике оценивается огнеупорный материал для печей, испытывающий сжимающее усилие. Механическая стойкость рассчитывается на основе зависимости процессов изменения структуры от температурной нагрузки. Кроме термической стойкости, важна и химическая защищенность. Поскольку огнеупорам в разных эксплуатационных условиях приходится контактировать с агрессивными химическими средами, изначально оценивается и способность противостоять разрушениям такого рода. Специалисты, в частности, выделяют материалы, которые могут сохранять стойкость при воздействии кислых веществ, восстановительных газов и шлаков.
Классификация по форме поставки
Для удобства применения огнеупорных материалов производители изначально наделяют их определенной формой, но также существует и целая группа неформованных изделий. Стандартизация по формованным огнеупорам предполагает выпуск традиционных плиточных и листовых изделий. Такие разновидности используются в техническом обеспечении стен, потолков, конструкций и т. д. Распространены и материалы с индивидуальным форм-фактором. Подобные изделия производятся с расчетом на узкоспециализированные задачи применения. Например, в составе тепловых агрегатов, изоляционных компонентов оборудования, в печных сооружениях и двигателях. В свою очередь, огнеупорные листовые материалы имеют универсальное назначение и чаще задействуются в изоляции производственных помещений. Что касается неформованных изделий, то их применяют в качестве заполнителей. Как правило, это сыпучие материалы, которыми заполняют заранее подготовленные технологические ниши.
Классификация по составу
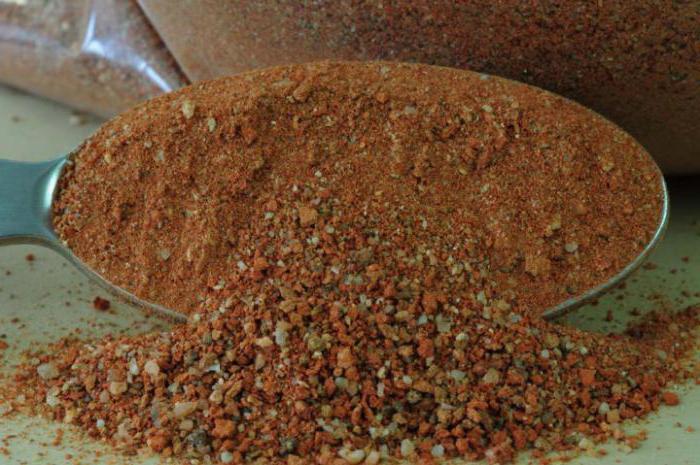
Независимо от типоразмера и форм-фактора, огнеупор должен эффективно выполнять основную задачу в виде термозащиты. Качество этой функции зависит уже от характеристик структуры материала изготовления. Так, существуют группы алюмосиликатных, безкислородных и волокнистых огнеупоров. В качестве сырья для алюмосиликатного материала используются оксиды кремния и алюминия. В производстве безкислородных термических изоляторов применяют, соответственно, компоненты, в составе которых отсутствуют кислородные соединения. К таким элементам относятся сульфиды, силициды, нитриды, карбиды и т. д. На основе специальных синтетических веществ изготавливают волокнистые изоляторы. Эту категорию широко представляют огнеупорные листовые материалы, сформированные из поликристаллических или высоко-глиноземных частиц. В качестве модификатора в состав волокнистых заготовок иногда добавляют и оксид циркония.
Классификация углеродистых огнеупоров
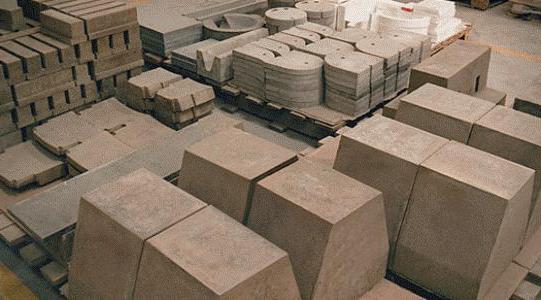
Это отдельная группа изоляционных материалов, которая объединяется применением свободного углерода. Наиболее распространены в этом семействе графитированные или угольные блоки, выполненные из термоантрацитов и смеси кокса. Для обеспечения связки между компонентами технологи задействуют каменноугольные смолы и битум. Близки по характеристикам к таким изделиям и графитированные материалы, изготавливаемые уже из нефтяного кокса. У этого изолятора отмечается графитовая структура и пониженное содержание золы, а температурный уровень для обжига составляет 2000 °С. Более сложен в технологическом отношении пирографит. Это огнеупорный материал, получение которого реализуется в ходе распада углеродосодержащих газовых смесей. Также помимо вышеназванных составляющих углеродистых термоизоляторов, производители нередко используют такие материалы, как шамот, корунд, активирующие пасты и суспензии.
Шамотные огнеупоры
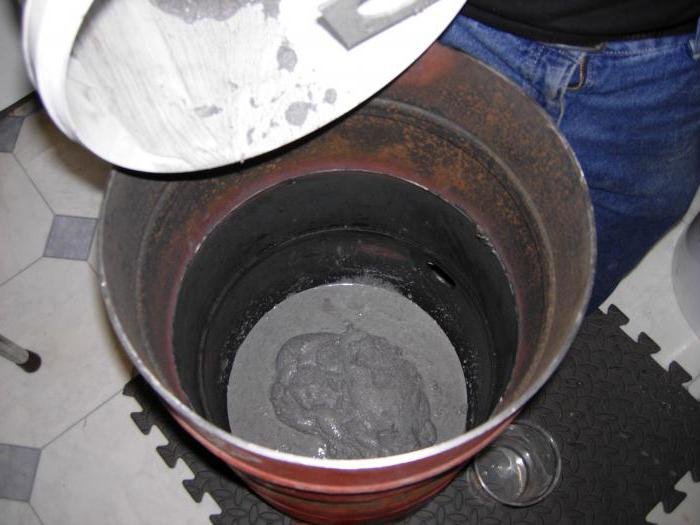
Это специализированные огнеупоры, предназначенные для футеровки печей. Внешне такое изделие может быть представлено разными формами. Стандартом считается та же огнеупорная плита, но могут быть и другие вариации – это зависит от конструкции конкретной печи, а также от параметров заготовочной формы. Основу состава представляют алюмосиликатные компоненты. В процессе обжига при повышенной температуре формируется первичный шамот, который затем измельчается и дополняется раствором глины и воды.
К свойствам шамота относится не только противостояние экстремальным температурам, но и безвредность контакта с техническими элементами котлов и печеней. Поскольку многие огнеупоры для поддержания изоляционной функции наделяются специальными химическими элементами, то их не рекомендуется использовать в условиях прямого взаимодействия с некоторыми металлами. В свою очередь, огнеупорный материал на основе шамота безопасен и для материалов топочных камер, и для изоляции футеровок.
Периклазовый огнеупор
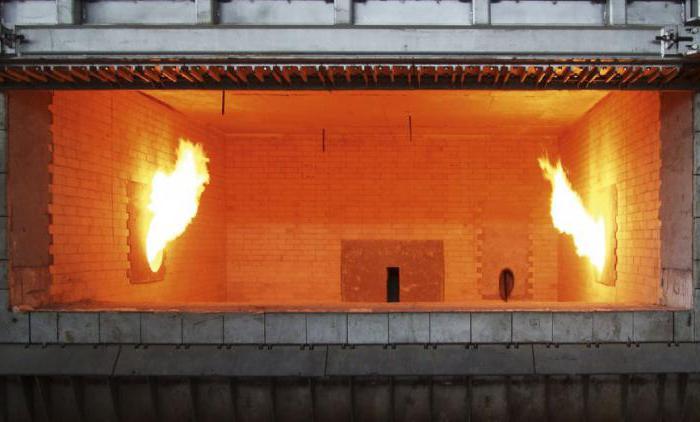
Такие изоляторы также называют магнезиальными, поскольку основу состава представляет сульфат магния. Они получаются в результате проведения безобжиговой технологической операции. И если в предыдущем случае шамот может представляться как огнеупорная глина, то периклаз является по большей части металлизированным изделием. Его часто применяют как часть сплава, на котором базируется печная футеровка. Вместе с магнезиальным компонентом в такой комплекс может входить сталь, медь и никель.
Есть и разновидность периклазоуглеродистых термостойких изоляторов, которые основываются на порошке. Изготовленная на базе периклазовых компонентов огнеупорная плита, в частности, может содержать порядка 25% графита и фенольную порошковую связку. Данная разновидность используется в защите поверхностей электродуговых печей и агрегатов, работающих с газовыми смесями. Также практикуется комбинированное применение периклазовых и шамотных изоляторов в составе единой конструкции.
Огнеупорное стекло
Уникальность данного материала заключается в том, что он в разных видах входит практически во все разновидности огнеупоров. Например, жидкое стекло может рассматриваться как плавкий изолятор в конструкции печей и котлов наряду с металлизированными плитами. Волокнистое огнеупорное стекло может входить в состав глиноземных изоляторов. Структурная универсальность материала обуславливает и гибкость применения. Такое стекло часто используется в случаях, когда необходимо произвести не просто техническую, но и декоративную защиту.
Сыпучие огнеупоры
В сущности это порошковые изделия, которые не проходят специальную формовку. Для них не обязательны процедуры выплавки или компоновки с целью получения определенных размеров. Самым популярным видом представления группы сыпучих изоляторов является огнеупорная смесь, но существуют и другие вариации. Среди них можно выделить суспензии, кусковые элементы, порошки и пасты. В зависимости от консистенции это могут быть полусухие или сухие и пластичные материалы.
Что касается использования, то сыпучие изоляторы применяются как заполнители. Неформованная огнеупорная смесь, например, входит в структуру изоляционной защиты сталелитейного оборудования. Таким образом предохраняются от теплового поражения отдельные детали мартеновских печей и сталеразливочных ковшей. Мелкофракционные сыпучие огнеупоры используют и в корпусах измерительных приборов.
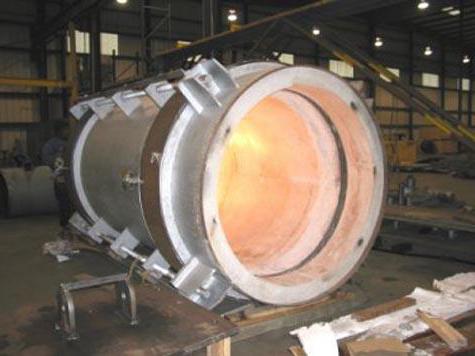
Огнеупорная глина
Промышленная термозащита, основанная на глинистых материалах, относится к группе шамотных изоляторов. Но в данном случае упор делается на сбалансированное сочетание химических элементов, в числе которых могут быть оксиды, кварц, алюмооксидная керамика и т. д. Комбинируя также уровни содержания кальция, натрия и магния технолог может получать огнеупорный материал с разными технико-эксплуатационными характеристиками. К примеру, водопоглощение может составлять 5-15 %, а огнеупорность достигает 2000 °С. При размере зерна в 2 мм пользователь может рассчитывать на защиту кладки из 30 блоков 20-киллограмовым пакетом глины. Что важно, огнеупоры такого типа быстро высыхают, позволяя в кратчайшие сроки после ремонта вводить печи и котлы в эксплуатацию.
Применение огнеупоров
Характер применения определяется набором свойств и формой конкретного изделия. Большинство огнеупоров ориентируются на футеровку печных сооружений и котельных конструкций. Это позволяет увеличивать срок службы агрегата в целом или отдельной его части. Используют такие материалы и в изготовлении спецодежды. Здесь можно отметить брезент огнеупорный, который отличается также износостойкостью и прочностью. Из него делают перчатки, фартуки и другие элементы одежды для промышленной и строительной сферы. В более узких отраслях, например, в упомянутом приборостроении могут использоваться и порошковые, и формовочные изделия. Они служат не только для защиты элементов прибора от повышенной температуры, но и для регуляции терморежима в соответствии с требованиями к условиям применения устройства.
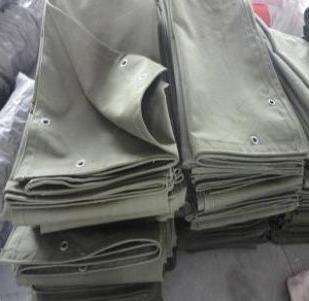
Заключение
Огнеупорные средства в современном виде наделяются множеством дополнительных качеств. Однако не стоит их рассматривать как полноценную защиту на случай пожара. Во-первых, стандартный огнеупорный материал по своим техническим параметрам не рассчитывается на такие задачи. Во-вторых, его нецелесообразно использовать в подобном качестве и с экономической точки зрения. Для противодействия огню существуют изоляторы другого типа, а огнеупоры все же ориентируются на локальное и целенаправленное создание барьера перед конкретным термическим воздействием.
Жаропрочные, жаростойкие и композиционные материалы
К таким материалам относятся:
- тугоплавкие металлы;
- спеченные сплавы тугоплавких металлов;
- дисперсно-упрочненные материалы;
- волокнистые композиционные материалы.
Тугоплавкие металлы
К тугоплавким металлам относятся цирконий, гафний, ванадий, ниобий, тантал, хром, молибден, вольфрам, рений. Наибольшее применение в качестве высокотемпературных конструкционных материалов нашли вольфрам, молибден, тантал, ниобий. В последнее время все шире применяются хром, ванадий и рений, которые хотя и менее тугоплавки, но благодаря своим специфическим свойствам начинают играть большую роль в производстве жаропрочных материалов.
Технология получения тугоплавких металлов включает получение порошков, формование заготовок и дальнейшая обработка.
Так, изделия из спеченного вольфрама изготовляют из порошка, полученного восстановлением водородом вольфрамового ангидрида или карбонильным методом. Порошки прессуют в стальных пресс-формах. Для улучшения прессуемости к порошку добавляют смазывающие и склеивающие вещества. Процесс спекания изделий проводят в две стадии. Первую стадию осуществляют в водороде при сравнительно для вольфрама, невысоких температурах (1100 –1300 °С). Вторую стадию спекания проводят при
температурах 2900 –3000 °С, которая создается пропусканием электрического тока через изделие, упрочненное предварительным спеканием. Эту стадию спекания, получившую название «сварка», осуществляют в водороде в специальных печах, которые называют сварочными аппаратами. Режим спекания в этом случае обычно контролируют не измерением температуры, а величиной пропускаемого тока. Крупногабаритные заготовки спекают в индукционных печах при температурах 2400 –2500 °С.
Аналогичная технология изготовления изделий из порошка молибдена. Порошок, полученный восстановлением молибдена водородом прессуют, как правило, со смазкой. Предварительное спекание проводят в водороде при 1100 –1200 °С. Затем изделия подвергаются сварке при силе тока, составляющей 90% от силы тока переплавки, что соответствует 2200 –2400 °С.
Спекание крупных заготовок можно проводить в вакуумной методической печи с графитовыми нагревателями, позволяющей обеспечить одновременно предварительное и окончательное спекание при температурах 1900 –1950 °С.
При изготовлении танталовых изделий исходный порошок, полученный натриетермическим восстановлением или электролизом, прессуют в заготовки. Перед прессованием в порошок тантала вводят раствор глицерина в спирте или какую-нибудь другую жидкую связку, которая при спекании удаляется полностью. Спекание заготовок проводят в вакууме. Заготовки предварительно спекают при 1000 –1200 °С. Спеченные заготовки охлаждают вместе с печью. Сварку проводят в вакууме, подбирая режим таким образом, чтобы обеспечить полное разложение и испарение примесей. При температуре сварки 2600 –2700 °С делают выдержку до полного удаления всех газов.
Заготовки после сварки охлаждают в вакууме и проковывают. Затем проводят вторичное спекание (отжиг) в вакуумном сварочном аппарате. В результате такой обработки получается беспористая заготовка с плотной структурой.
Аналогично рассмотренному получают спеченный ниобий и рений.
Изделия из порошков циркония и ванадия изготавливают по схожим технологиям. Порошки прессуют в пресс-формах и заготовки спекают в вакууме. Циркониевые заготовки спекают при 1200 – 1300 °С, а ванадиевые – при 1400 –1700 °С.
Спеченные сплавы тугоплавких металлов
Спеченные сплавы тугоплавких металлов обладают более высоким комплексом механических свойств при повышенных температурах чем чистые тугоплавкие металлы. Повышение этих свойств достигается легированием.
Структура большинства жаропрочных сплавов на основе тугоплавких металлов представляет собой гетерогенные сплавы, основой которых является твердый раствор. Упрочение при легировании объясняется тем, что в результате взаимодействия растворенных атомов с дислокациями происходит закрепление или блокирование дислокаций. В многих сплавах на основе тугоплавких металлов, содержащих повышенное количество примесей внедрения, образуются избыточные фазы типа карбидов, нитридов и других соединений, которые также способствуют упрочению сплавов.
Повышение свойств сплавов тугоплавких металлов достигается также применением термической обработки, заключающейся в закалке с высоких температур с последующим старением при температурах, близких к рабочим. В этом случае карбиды, нитриды и другие химические соединения, образуемые металлами (титан, цирконий, тантал, ниобий) с элементами внедрения, выполняют роль фаз — упрочнителей.
Известны порошковые вольфрамоникелевые сплавы, применяемые для изготовления ракетных сопел, а также ванадиевые сплавы, используемые для изготовления деталей, работающих при температурах до 1250 °С. Свойства сплавов приведены в таблице 1.
Состав | Твердость | Предел прочности, МПа при температуре, °С | ||
20 | 1100 | 1200 | ||
V+20%Nb+5%Ti+0,5%C | 3400 | – | 235 | 140 |
V+20%Nb+5%Ti+0,5%C+0,1%B | 4800 | 760 | 280 | 225 |
V+20%Nb+3%Ti+0,5%C+0,1%B | 3900 | – | 363 | 179 |
V+10%Nb+7%Ti+10%Ta+5%Mo+0,5%C | 3400 | 670 | 405 | – |
Высокотемпературная прочность спеченных ванадиевых сплавов не уступает прочности литых аналогичного состава, а в некоторых случаях и превосходит их.
Дисперсно-упрочненные материалы
Дисперсноупрочненные материалы представляют собой композиционные спеченные материалы, содержащие искусственно вводимые в них высокодисперсные, равномерно распределенные частицы фаз, не взаимодействующих с матрицей и не растворяющихся в ней до температуры ее плавления.
Наиболее эффективное упрочение обеспечивается при содержании упрочняющей фазы в количестве 3 – 15%, размере ее частиц до 1мкм и среднем расстоянии между ними 0,1 –0,5 мкм.
Дисперсноупроченные материалы сохраняют микрогетерогенное строение и дислокационную структуру, а следовательно, и работоспособность до 0,9–0,95 Tпл матрицы. Высокая работоспособность дисперсноупроченных материалов при повышенных температурах объясняется тем, что при наличии в матрице второй фазы скольжение дислокаций в зернах металла становится возможным при больших напряжениях, границы зерен блокируются, а рост зерен затормаживается практически до температуры плавления матрицы.
При создании дисперноупроченных материалов выбирают фазу–упрочнитель и способ введения ее в матрицу.
Фаза–упрочнитель должна иметь высокую термодинамическую прочность, малую величину скорости диффузии компонентов фазы в матрицу, высокую чистоту и большую суммарную поверхность частиц. К упрочняющим фазам с такими свойствами относятся оксиды некоторых металлов (чаще всего Al2O3, SiO2, ThO2, ZrO2, Cr2O3), карбиды, нитриды и другие соединения.
Способ введения частиц фазы–упрочнителя в матрицу влияет на структуру дисперсно-упрочненного материала, которая может быть дисперсной или агрегатной. Способами введения фазы–упрочнителя и получения смеси является:
- механическое смешивание порошков оксидов металла и упрочняющей фазы с последующим восстановлением оксидов основного металла;
- механическое смешивание порошков металла матрицы и упрочняющей фазы;
- поверхностным окислением порошка основного металла;
- химическое смешивание, предусматривающее совместное осаждение солей и их последующее восстановление с образованием металла и сохранением фазы–упрочнителя;
- внутренним окислением или азотированием порошков.
Первые три метода приводят к образованию агрегатной структуры, а последние два – к дисперсной.
В настоящее время разработаны и применяется целый ряд дисперсно-упрочненных материалов. В различных отраслях техники успешно используются:
- алюминиевые,
- вольфрамовые,
- молибденовые,
- железные,
- медные,
- кобальтовые,
- хромовые,
- никелевые,
- бериллиевые,
- платиновые сплавы.
Дисперсно-упрочненные алюминиевые сплавы
В алюминиевых сплавах в качестве упрочняющей фазы используется оксид алюминия Al2O3, легко образующийся в результате высокой склонности алюминия к поверхностному окислению и позволяющий получать равномерное распределение его в матрице. Содержание упрочняющей фазы (Al2O3) обычно находится в пределах 4 – 14%.
Длительная прочность дисперсно-упрочненных алюминиевых сплавов, называемых сплавами САП (спеченные алюминиевый порошок), при повышенных температурах превосходит прочность всех деформируемых алюминиевых сплавов. Все сплавы хорошо обрабатываются, их можно сваривать и паять.
Алюминиевые сплавы применяются в авиационной технике (обшивка гондол силовых установок в зоне выхлопа, жалюзи).
Вольфрамовые сплавы упрочняют обычно оксидами тория (ThO2) в количестве 0,75–2,0%. Для повышения прочности и пластичности при низких температурах вводят рений в количестве 3–5%.
Дисперсно-упрочненные вольфрамовые сплавы
Дисперсно-упрочненные вольфрамовые сплавы широко используют в ракетно–космической технике.
Молибденовые сплавы упрочняют карбидами, нитридами, оксидами. Карбидное упрочнение дает возможность получить сплавы с высоким пределом прочности при температуре 1400 °С. При температурах выше 1500–1600 °С эти сплавы сильно разупрочняются из-за рекристаллизации.
Упрочнение сплава оксидом тория (ThO2) дает высокий эффект даже в рекристализованном состоянии, а легированние вольфрамом и упрочнение карбидом тантала (TaС) дает возможность получения сплава с высокими механическими свойствами при температурах 1600–2000 °С.
Дисперсно-упрочненные молибденовые сплавы
Дисперсно-упрочненные молибденовые сплавы применяются в авиационной технике. Упрочненные железные сплавы получают введением в железо около 6% Al2O3. Это обеспечивает хорошие прочностные характеристики сплавов при температурах 650–950 °С. Более высокие свойства имеют дисперсноупрочненные стали. Так, хромоалюминиевая сталь, упрочненная Al2O3, и сложнолегированная, упрочненная TiO2, имеют характеристики при температуре 650 °С почти вдвое выше, чем упрочненные железные сплавы.
Дисперсно-упрочненные стали
Дисперсно-упрочненные стали превосходят литые по длительной прочности. Кроме того, в них снижается эффект охрупчивания под действием облучения. Поэтому они используются в реакторостроении, даже если они не имеют преимуществ перед стандартными материалами по прочности.
Дисперсно-упрочненные медные сплавы
Медные упрочненные сплавы получают путем введения оксидов алюминия, бериллия и тория. Для сохранения электропроводности и пластичности содержание оксидов недолжно превышать 1,5–2,0%.
Дисперсно-упрочненная медь обладает высоким сопротивлением ползучести и высокой жаропрочностью, что позволяет использовать ее для изготовления деталей, работающих при повышенных температурах (детали теплообменников, электровакуумных приборов). Медь, содержащая включения тугоплавких соединений, применяется для изготовления электродов точечной и роликовой сварки.
Дисперсно-упрочненные кобальтовые сплавы
При получении кобальтовых сплавов в качестве упрочняющей фазы применяют в основном оксид тория (ThO2) с содержанием последнего 2–4%. Так, временное сопротивление кобальтовых сплавов с 2% ThO2 составляет 1020 МПа при 25 °С и 140 МПа при 1090 °С.
Для повышения пластичности сплавы кобальта легируют никелем, а для повышения окалиностойкости – хромом.
Никелевые сплавы получают путем упрочнения никеля оксидами тория (ThO2) или гафния (HfO2). Содержание упрочняющей фазы составляет 2–3%.
Дисперсно-упрочненные никелевые сплавы
Дисперсно-упрочненные сплавы никеля очень технологичны. Их можно ковать, штамповать, вытягивать в широком интервале температур. Они обладают хорошей жаростойкостью и используются для изготовления деталей газовых турбин.
Дисперсно-упрочненные хромовые сплавы
При получении дисперсно-упрочненных хромовых сплавов следует иметь ввиду, что хром при комнатной температуре имеет повышенную хрупкость, и температура перехода в пластичное состояние зависит от количества и формы примесей внедрения и размера зерна. Измельчение зерна при введении дисперсной фазы положительно влияет на технологические свойства хрома.
В качестве упрочняющей фазы могут использоваться оксиды тория (ThO2) и оксиды магния (MgO).
Положительно влияют на жаропрочность дисперсно-упрочненного хрома добавки марганца, молибдена, тантала, ниобия.
Дисперсно-упрочненные бериллиевые сплавы
Дисперсно-упрочненные бериллиевые сплавы получают путем введения оксида бериллия (BeO), используя склонность к поверхностному окислению промышленных бериллиевых порошков.
Высокое сопротивление ползучести достигается при упрочнении сплавов карбидом бериллия (Be2C). При содержании 2,5% Be2C величина 100σ возрастает в 3 раза при 650°С по сравнению с чистым бериллием.
Дисперсно-упрочненные бериллиевые сплавы обладают высокой прочностью, высоким модулем упругости и большим коэффициентом рассеивания нейтронов.
Дисперсно-упрочненные платиновые сплавы
Платиновые сплавы хорошо работают при высоких температурах в окислительной среде. Упрочнение их осуществляется оксидами (ThO2) или карбидами (TiС), содержание которых для сохранения пластичности должно быть минимальным.
Дисперсно-упрочненные платиновые сплавы используются для изготовления нагревателей, термопар и термометров сопротивления.
Волокнистые композиционные материалы
Волокнистые композиционные материалы состоят из матрицы, которая содержит упрочняющие элементы в форме волокон (проволоки) или нитевидных кристаллов.
В волокнистых материалах матрица скрепляет волокна в единый монолит, защищая их от повреждений. Она является средой, передающей нагрузку на волокна, а в случае разрушения отдельных волокон перераспределяет напряжения.
Особенность волокнистой композиционной структуры заключается в равномерном распределении высокопрочных волокон в пластичной матрице. Объемная доля волокон может колебаться от 15 до 25%. Поверхности раздела в волокнистых композиционных материалах рассматриваются как самостоятельный элемент структуры в которой происходят процессы растворения, образования и роста новых фаз. Здесь формируется связь между упрочняющим волокном и матрицей. От совершенства такой связи зависит уровень свойств волокнистых композиционных материалов.
В качестве методов получения композиционных материалов используются горячее прессование, пропитку жидким металлом, электроосаждение, экструдирование и прокатку, сварку взрывом, эвтектическую кристаллизацию.
В настоящее время наиболее широко применяются волокнистые композиционные материалы на основе алюминия, магния, титана и никеля.
На основе алюминия можно получить волокнистые композиции алюминий-сталь, алюминий-молибден, алюминий-карбид кремния, алюминий-углерод и другие.
Композиционный материал алюминий-сталь получают сваркой взрывом или горячим прессованием. Упрочняющим материалом является высокопрочная стальная проволока.
Разработана технология получения композиционных материалов на основе алюминия, легированного магнием и кремнием, армированного нитевидными кристаллами.
Технология получения композиции алюминий-углерод состоит в пропитке волокон углерода жидким металлом. Для обеспечения смачивания и ограничения взаимодействия между матрицей и волокном используют покрытия из борида титана, никеля, меди, тантала и других соединений. Покрытые волокна протягивают через расплав. Композиционные материалы, полученные пропиткой волокон углерода, покрытые боридом титана имеют σВ=1120 МПа.
Композиционные материалы на магниевой основе получают методами горячего прессования или диффузионной сварки, непрерывного литья, пропитки жидким металлом, плазменного напыления с последующим прессованием, методом сварки взрывом.
Для армирования магния применяют высокопрочную стальную и титановую проволоку, волокна бора и углерода, нитевидные кристаллы карбида кремния.
Магниевые сплавы как матрицы композиционных материалов практически не реагируют с основными классами армирующих волокон, что позволяет применять для получения композиционных материалов жидкофазные технологии и является большим преимуществом этих сплавов.
Материал магний–бор (Mg–B), полученный методом непрерывного литья, заключающегося в пропускании армирующих волокон бора через ванну расплавленного магния и последующего формирования заготовки путем прохода пучка покрытых волокон через кристаллизатор-фильеру, имеет σВ=963 МПа при объемной доли волокон 0,30 и σВ=1330 МПа при объемной доли 0,75.
Титановые композиционные материалы изготавливаются при довольно высоких температурах (800–1000 °С). Наиболее распространенными упрочнителями для титановой матрицы являются волокна бора, молибдена, бериллия, карбида кремния, оксида алюминия.
Композиционный материал Ti–B, полученный методом диффузионной сварки при температуре 800–880 °С имеет σВ=900 МПа при объемной доли волокон 0,36.
Никелевые композиции изготавливают методами обработки давлением, пропитки раствором и порошковой металлургии.
В качестве матрицы чаще всего служат жаростойкие никелевые сплавы типа ХН60В и ХН77ТЮР, а упрочнителей – вольфрамовые волокна. Наиболее распространенным методом изготовления никелевых композиционных материалов является горячая прокатка.
ПОДЕЛИСЬ ИНТЕРЕСНОЙ ИНФОРМАЦИЕЙ
Огнеупорные материалы — Огнеупорные материалы
Огнеупорные материалы — это материалы применяемые для проведения металлургических процессов (плавка, отжиг, обжиг, испарение и дистилляция), конструирования печей, высокотемпературных агрегатов (реакторы, двигатели, конструкционные элементы и др).
Огнеупорные материалы отличаются повышенной прочностью при высоких температурах, химической инертностью. По составу огнеупорные материалы это керамические смеси тугоплавких оксидов, силикатов, карбидов, нитридов, боридов. В качестве огнеупорного материала применяется углерод (кокс, графит). В основном это неметаллические материалы, обладающие огнеупорностью не ниже 1580°C, применяются практически везде, где требуется ведение какого-либо процесса при высоких температурах.
Огнеупоры подразделяются на формованные (изделия) и неформованные (порошки, мертели и т. д.), также их классифицируют по следующим признакам:
- огнеупорность
- пористость
- химико-минеральный состав
- область применения
Классификация по огнеупорности
- огнеупорные (огнеупорность от 1580 до 1770 ° С)
- высокоогнеупорные (от 1770 до 2000 ° С)
- высшей огнеупорности (более 2000 ° С)
Классификация по пористости
- особоплотные (открытая пористость до 3 %)
- высокоплотные (открытая пористость от 3 до 10 %)
- плотные (открытая пористость от 10 до 16 %)
- уплотненные (открытая пористость от 16 до 20 %)
- среднеплотные (открытая пористость от 20 до 30 %)
- низкоплотные (пористость от 30 % до 45 %)
- высокопористые (общая пористость от 45 до 75 %)
- ультрапористые (общая пористость более 75 %)
Классификация по химико-минеральному составу
Следует различать кислые, нейтральные и основные огнеупоры. Более детальная классификация производится по их химическому составу:
- Кремнеземистые
- Алюмосиликатные
- Глиноземистые
- Глиноземоизвестковые
- Высокомагнезиальные
- Магнезиально-известковые
- Известковые
- Магнезиально-шпинелидные
- Магнезиально-силикатные
- Хромистые
- Цирконистые
- Оксидные
- Углеродистые
- Оксидоуглеродистые
- Карбидкремниевые
- Бескислородные
Область применения
Огнеупоры имеют очень много областей применения, но всех их можно разбить на две основные группы, это огнеупоры (огнеупорные изделия, например, кирпич) общего назначения, и огнеупоры, спроектированные специально для какого-либо теплового агрегата.
Периклазоуглеродистые огнеупоры [periclase (magnesite)-carbon refractories] — огнеупоры, изготавливающиеся из периклаз. порошка с добавлением 6—25 % природного или искусственного графита и органич. связки (напр., фенольной порошкообразной с этиленгли-колем или бакелита). Периклазоуглеродистые огнеупоры применяют для футеровки устройств для подачи газа снизу в конвертерах с комбинированной продувкой и ответств. участков стен мощных электродуговых печей; для шлак, пояса электродуг. печей и сталеразлив. ковшей, а также шиберных затворов;
Углеродистые огнеупоры [carbon refractories] — огнеупоры, состоящие преимущественно из своб. углерода или содержащие углерод в качестве основного компонента. К углеродистым огнеупорам относят: угольные и графитир. блоки, изготовляемые из кокса и термоантрацита с каменноугольной смолой, пеком, битумом, антрац. маслом, обжигаемые при 1100—1450 °С; графитир. изделия из нефтяного кокса с графит. структурой и малым содержанием золы, получаемые обжигом при / > 2000 °С; пирографит — продукт разложения углеродсодержащего газа на нагретой поверхности и др. К углеродистым огнеупорам относят также углеродсодержащие огнеупоры, изготовляемые из графита, огнеупорной глины, шамота (в т.ч. высокоглиноземистого), корунда и т.п. Углеродистые огнеупоры отличаются высокой теплопроводностью, низким ТКЛР, хорошей стойкостью при взаимодействии с расплавами металлов и шлаками. Углеродистые огнеупоры применяют для футеровки нижнего строения домен, печей, электротермич. печей, агрегатов для плавки свинца, меди и др., а также для изготовления погружных стаканов, стопоров-моноблоков, вкладышей для изложниц, тиглей для плавки цветных металлов и др. Неформов. углеродистые огнеупоры из кокс, порошков на каменноуг. смоле применяют для заполнения швов кладки, углеродсодержащие — для футеровки желобов домен, печей и др.;
Шамотные огнеупоры [fireclay refractories] — алюмосиликатные огнеупоры, содержащие, мае. %, 28-45 А12О3 и 50-70 SiO2. Технология производства формов. шамотных огнеупоров включает: обжиг глины (каолина) при 1300-1500 °С во вращ. или шахтных печах, измельчение полученного шамота, смешивание со связ. глиной и водой (иногда с добавлением других связывающих материалов), формование, сушку и обжиг при 1300—1400 °С. Ш. о. применяют для футеровки домен, печей, сталеразлив. ковшей, нагреват. и обжиг, печей, котельных топок и др., а тж. для изготовления сифонных изделий для разливки стали. Неформов. Шамотные огнеупоры изготовляют из измельченного шамота и связ. материалов и применяют в виде мертелей, набивных масс, порошков, заполнителей бетонов и др. при выполнении и ремонте огнеуп. футеровок разных тепловых агрегатов.
асбестовые, базальтовые, кварцевые, кремнеземные и углеродные
Негорючая ткань – это специальный тип материала, обеспечивающий эффективную защиту от действия высоких температур и открытого пламени.
Благодаря специальному составу она может относительно длительное время пребывать в огне или под тепловым излучением, не меняя своих характеристик, сохраняя защитные свойства.
Широкую популярность огнеупорные материалы получили в таких отраслях:
- металлургическая;
- энергетическая;
- химическая;
- нефтеперерабатывающая;
- производство спецодежды и пр.
Область применения огнеупорных тканей
Негорючая строительная ткань широкое практическое применение получила в роли теплоизоляционного материала, защищающего от пламени, теплового потока.
Благодаря тепловой и механической устойчивости она активно используется в роли прокладочного материала в разных промышленных отраслях.

Спецодежда для сталеваров
Область применения огнезащитного полотна также распространяется на отрасль по производству спецодежды. Из него выпускаются защитные костюмы пожарных, сталеваров, работников нефтеперерабатывающих заводов, химических лабораторий.
Огнеупорные ткани для спецодежды – это гарантированная защита человека от теплового воздействия в случае его пребывания в области возгорания, взрыва, сильного теплового облучения.
Виды негорючих тканей
Для решения перечисленных выше задач по защите от теплового излучения и открытого огня существует несколько типов огнеупорных материалов. Рассмотрим кратно их основные особенности.
Асбестовые
Для производства асбестовых спецтканей используют природные силикаты, которые отличаются очень тонкими волокнами и могут использоваться в качестве теплозащитного материала.

Огнеустойчивая асбестовая ткань
Асбест является устойчивым к температурам вплоть до +500ºС, характеризуется хорошими изоляционными свойствами и рассчитан для применения в качестве противопожарной кошмы и материала для придания огнеустойчивости строительным конструкциям.
Использовать огнеупорные асбестовые ткани для пошива одежды не рекомендуется, поскольку они выделяют асбестовые микрочастицы, которые вредны человеку при их вдыхании. Только дополнительная обработка может исключить этот недостаток, но это приведет к существенному удорожанию спецодежды.
Кварцевые
Для получения этого противопожарного полотна используют волокна, вытягиваемые из натурального кварца при высоких температурах.
Материал из кварцевых нитей выдерживает температурный режим в пределах до +1400ºС без изменения структуры, рабочих характеристик. При длительном пребывании в огне он может выдержать даже температуру в +2000ºС.

Кварцевая огнеупорная ткань
Кварцевая ткань получила широкое применение в энергетической и химической отрасли в качестве технического материала, а также для пошива огнезащитной одежды. Основным ее преимуществом является максимальная безопасность для человека.
Базальтовые
Эти спецткани производятся из волокон базальта, получаемых методом расплавления и вытягивания. Огнезащитное полотно с базальтовой основой способно выдерживать температуру до +700ºС.

Базальтовая огнезащитная ткань
Также выпускается и нетканый материал, который получил широкое применение в качестве огнезащиты различных металлоконструкций, а также в роли материала, которым заполняют пустоты противопожарных преград.
Кремнеземные
Кремнеземные негорючие ткани по своему составу напоминают кварцевые огнеустойчивые материалы. Отличие между ними заключается в том, что кремнеземное полотно содержит меньше диоксида кремния.
Вследствие этого оно способно выдерживать несколько меньшие температуры – до +1200ºС. Изменение характеристик материала и его разрушение начинается с температур +1800ºС.

Кремнеземная огнеустойчивая ткань
Кремнеземная спецткань полностью безопасна для человека. Она используется для огнеустойчивых и изоляционных покрытий, для создания защит из негорючей ткани для печей.
Углеродные
Спецткань этого типа производится с помощью классических ткацких технологий. Для этого используются длинные и короткие углеродные нити, получаемые из полиакрилонитрила и вискозы.
Углеволокно устойчиво к повышенным температурам, химическим препаратам и растяжению.

Углеродная огнеупорная ткань
Оно отличается небольшим весом, поэтому активно используется для пошива защитной одежды, которая будет эксплуатироваться при температурных режимах, не превышающих +370ºС.
Арамидные
Арамидная огнеупорная ткань производится из арамидных нитей, которые сплетают особым образом, создавая специальную структуру полотна. Нити могут переплетаться саржевым, полотняным, вафельным или атласным способом.

Армидная огнезащитная ткань
Благодаря такому сложному строению спецткани она характеризуется высокой устойчивостью к механическим повреждениям. Кроме этого, материал устойчив к высоким температурам – выдерживает нагревание в пределах +250…400°С, а кратковременно – температуру около +1000°С.
Полиэфирные
При добавлении соединений фосфора к волокну, синтезированному из полиэфиров, оно становится термоустойчивым и способным противостоять горению.
Для производства полиэфирных тканей используются разные плетения, в результате чего получается молескин, бархат, репс, жаккард и др.

Полиэфирная огнезащитная ткань
Эти материалы имеют приятный вид и хорошие защитные свойства от высокой температуры. При попадании изделий из полиэфирной ткани в область открытого пламени она не плавится, слегка обугливается, не выделяя вредных веществ.
Пропитка
Существует еще один подход к производству огнеустойчивых спецтканей, позволяющий любому материалу придать огнеустойчивость. Он основан на пропитывании волокон специальным веществом, не поддерживающим горение.
Этот метод технологически прост и не требует больших финансовых вложений.

Огнезащитная пропитка для ткани «Огнеза»
Единственным его недостатком является потеря со временем эффекта огнеустойчивости. Пропитки хватает приблизительно на год, после этого требуется дополнительная обработка.
Преимущества и недостатки
К основным преимуществам огнеупорных материалов относятся:
- защищают от теплового потока;
- не горят в открытом пламени;
- кратковременно выдерживают тепловой удар в несколько тысяч градусов;
- устойчивы к механическим повреждениям;
- защищают от химических веществ;
- имеют увеличенную биозащиту;
- устойчивы к воздействию влаги.
Кроме положительных сторон, огнезащитные материалы имеет несколько недостатков. Есть некоторые ткани, которые:
- при нагревании могут выделять токсичные вещества;
- меняют свои характеристики под воздействием прямых солнечных лучей;
- в процессе эксплуатации выделяют микрочастицы, опасные для дыхательной системы человека.
Если правильно применять огнеупорную спецткань для ее целевого предназначения, то действие всех перечисленных недостатков на организм человека можно полностью исключить.
Заключение
Большой выбор огнеупорных тканей с различными характеристиками позволит использовать их в разных отраслях деятельности человека.
Потребительский рынок насыщен предложениями огнезащитных тканей для спецодежды, бытового или промышленного применения.
Благодаря широкому распространению такого рода материалов обеспечивается эффективная защита от теплового излучения и прямого контакта с огнем живых организмов, увеличивается пожарная безопасность объектов.
Видео: Проверка огнестойкости базальтовой ткани
Жаропрочные сплавы — Википедия
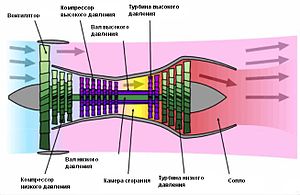
Жаропрочные сплавы — металлические материалы, обладающие высоким сопротивлением пластической деформации и разрушению при действии высоких температур и окислительных сред. Начало систематических исследований жаропрочных сплавов приходится на конец 1930-х годов — период нового этапа в развитии авиации, связанного с появлением реактивной авиации и газотурбинных двигателей (ГТД).
Жаропрочные сплавы могут быть на алюминиевой, титановой, железной, медной, кобальтовой и никелевой основах. Наиболее широкое применение в авиационных двигателях получили никелевые жаропрочные сплавы, из которых изготавливают рабочие и сопловые лопатки, диски ротора турбины, детали камеры сгорания и т. п. В зависимости от технологии изготовления никелевые жаропрочные сплавы могут быть литейными, деформируемыми и порошковыми. Наиболее жаропрочными являются литейные сложнолегированные сплавы на никелевой основе, способные работать до температур 1050—1100 °C в течение сотен и тысяч часов при высоких статических и динамических нагрузках[1].
Первые жаропрочные стали для газотурбинных двигателей были разработаны в Германии фирмой Krupp в 1936—1938 годах. Высоколегированная аустенитная сталь Тинидур создавалась как материал рабочих лопаток турбины на температуры 600—700 °C. Тинидур — аустенитная сталь с дисперсионным твердением (Ni3Ti) и карбидным упрочнением. В 1943—1944 годах годовое производство Тинидур составляло 1850 тонн. Институтом Deutsche Versuchsanstalt für Luftfahrt (DVL) и фирмой Heraeus Vacuumschmelze были разработаны аустенитые стали (сплавы по английской терминологии) DVL42 и DVL52 на более высокие рабочие температуры 750—800 °C. Составы сталей приведены в таблице.
Химические составы германских аустенитных жаропрочных сталей для газотурбинных двигателей[2][3][4]Наименование | %C | %Mn | %Si | %Ni | %Co | %Cr | %Mo | %W | %Ti | %Al | % др. элементов |
---|---|---|---|---|---|---|---|---|---|---|---|
Тинидур | до 0,14 | 0,6-1,0 | 0,6-1,0 | 29,0-31,0 | 14,5-15,5 | 1,8-2,2 | 0,2 | Fe основа | |||
DVL42 | до 0,1 | 0,6-1,0 | 0,4-0,8 | 30-35 | 22-25 | 12-17 | 4-6 | 4-6 | 1,5-2,0 | Fe основа | |
DVL52 | до 0,1 | 0,6-1,0 | 0,4-0,8 | 30-35 | 22-25 | 12-17 | 4-6 | 4-6 | 4-5 %Ta | ||
Хромадур | 0,9-0,12 | 17,5-18,5 | 0,55-0,7 | 11,0-14,0 | 0,7-0,8 | V 0,60-0,70 0,18-0,23 N2 |
В Германии 1940-х годов среди разработчиков авиационных ГТД существовало стремление повысить температуру газа перед турбиной до 900 °C. С этой целью институт DVL совместно с рядом фирм экспериментировал с аустенитными сложнолегированными сплавами. В ходе войны была признана невозможность подобного решения по причине острого дефицита в Германии легирующих элементов. В результате исследования приняли два направления: 1. создание полых охлаждаемых воздухом лопаток (рабочих и сопловых) при соответствующем снижении легирования используемых материалов; 2. исследование возможностей керамических материалов. Оба направления работ являлись пионерскими, по каждому из них были получены значимые результаты.
Первые серии реактивного двигателя Jumo-004A выпускались с 1942 года с монолитными рабочими и сопловыми лопатками из материала Тинидур фирмы Крупп. Позднее заменены полыми охлаждаемыми лопатками из того же материала, что позволило повысить температуру газа перед турбиной до 850 °C (серия Jumo-004E). С 1944 года на серийных модификациях двигателя Jumo-004B применялись полые охлаждаемые рабочие лопатки из менее дефицитной стали Cromadur.
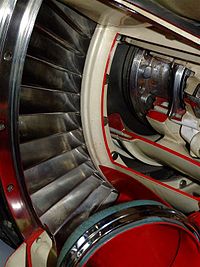
К 1942 году в Великобритании создан жаропрочный сплав Нимоник-80 — первый в серии высокожаропрочных дисперсионно-твердеющих сплавов на никель-хромовой основе. Создатель сплава — Уильям Гриффитс англ. Griffiths W.T.. Основа сплава Нимоник-80 — нихром (80 %Ni — 20 %Cr), известный с начала XX века своей высокой жаростойкостью и высоким электрическим сопротивлением. Ключевыми легирующими элементами сплава нимоник-80 являлись титан (2,5 %) и алюминий (1,2 %), образующие упрочняющую фазу. Количество упрочняющей гамма-штрих фазы в сплаве составляло 25-35 об%[5]. Нимоник-80 использовался в деформированном состоянии для изготовления рабочих лопаток турбины одного из первых газотурбинных двигателей Роллс-Ройс Нин (англ.), стендовые испытания которого начались в октябре 1944 года. Лопатки турбины из сплава нимоник-80 обладали высокой длительной прочностью при температурах 750—850 °C.
В СССР аналогами сплава нимоник-80 являются никелевые жаропрочные сплавы ЭИ437, ЭИ437А (ХН77ТЮ) и ЭИ437Б (ХН77ТЮР), срочным порядком созданные к 1948 году сотрудниками ВИАМ, ЦНИИЧермет и завода «Электросталь» при участии Ф. Ф. Химушина[6].
Основу жаропрочных сплавов, как правило, составляют элементы VIII группы таблицы Менделеева. До 1940-х годов основу жаропрочных сплавов составляли железо или никель. Добавлялось значительное количество хрома для увеличения коррозионной стойкости. Добавки алюминия, титана или ниобия увеличивали сопротивление ползучести. В некоторых случаях образовывались хрупкие фазы, такие, например, как карбиды M23C6. В конце 40-х годов прекратилось, в основном, использование железа как основы жаропрочных сплавов, предпочтение начали отдавать сплавам на основе никеля и кобальта. Это позволило получить более прочную и стабильную гранецентрированную матрицу.
В конце 1940-х годов была обнаружена возможность дополнительного упрочнения жаропрочных сплавов путём легирования молибденом. Позже для этой же цели начали применять добавки таких элементов, как вольфрам, ниобий, тантал, рений и гафний. (См. Карбид тантала-гафния, хотя в жаропрочных сплавах гафний не образует подобных карбидов, а повышает прочность и пластичность «механически», вызывая закручивание границ зёрен, т. н. «гафниевый эффект». Помимо этого, он участвует в образовании дополнительных количеств гамма-штрих фазы[7]).
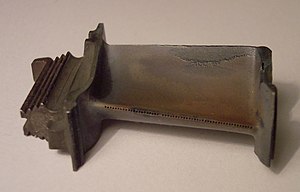
В 1950-х годах компаниями Pratt & Whitney и General Electric были разработаны сплавы Уаспалой и M-252, легированные молибденом и предназначенные для лопаток авиационных двигателей. Затем были разработаны такие сплавы, как Hastelloy alloy X, Rene 41, Инконель, в том числе Inco 718, Incoloy 901 и др.
Согласно оценкам экспертов, за период 1950—1980-х годов химические составы никелевых жаропрочных сплавов изменялись наиболее значительно за счет введения алюминия и замещающих его элементов в γ{\displaystyle \gamma }’ фазе. Указанное привело к увеличению объемной доли γ{\displaystyle \gamma }’ фазы от 25-35 об.% в сплавах нимоник 80 и U-700 до 65-70 об.% в современных лопаточных материалах[5].
Легирование[править | править код]
Жаропрочные сплавы на основе никеля, как правило, обладают сложным химсоставом. Он включает 12 — 13 компонентов, тщательно сбалансированных для получения необходимых свойств. Содержание таких примесей, как кремний (Si), фосфор (P), сера (S), кислород (O) и азот (N) также контролируется. Содержание таких элементов, как селен (Se), теллур (Te), свинец (Pb) и висмут (Bi) должно быть ничтожно малым, что обеспечивается подбором шихтовых материалов с низким содержанием этих элементов, так как избавиться от них в ходе плавки не представляется возможным. Эти сплавы обычно содержат 10—12 % хрома (Cr), до 8 % алюминия (Al) и титана (Ti), 5-10 % кобальта (Co), а также небольшие количества бора (B), циркония (Zr) и углерода (C). Иногда добавляются молибден (Mo), вольфрам (W), ниобий (Nb), тантал (Ta) и гафний (Hf).
Легирующие элементы в этих сплавах можно сгруппировать следующим образом:
- Элементы, образующие с Ni аустенитную γ{\displaystyle \gamma }-матрицу с гранецентрированной кристаллической решёткой — Co, Fe, Cr, Mo и W
- Элементы, образующие упрочняющую γ{\displaystyle \gamma }’ фазу (Ni3X) — Al, Ti, Nb, Ta, Hf. При этом Ti, Nb и Ta входят в состав фазы и упрочняют её.
- Элементы, образующие сегрегации по границам зёрен — B, C и Zr
К карбидообразующим элементам относятся Cr, Mo, W, Nb, Ta и Ti. Al и Cr образуют оксидные плёнки, защищающие изделия от коррозии.
Типичный химсостав деформируемых жаропрочных сплавов на никелевой основе[8]Сплав | %Ni | %Cr | %Co | %Mo | %Al | %Ti | %Nb | %C | %B | Zr | % др. элементов |
---|---|---|---|---|---|---|---|---|---|---|---|
Inconel X-750 | 73,0 | 18,0 | — | — | 0,8 | 2,5 | 0,9 | 0,04 | — | — | 6,8 % Fe |
Udimet 500 | 53,6 | 18,0 | 18,5 | 4,0 | 2,9 | 2,9 | — | 0,08 | 0,006 | 0,05 | |
Udimet 700 | 53,4 | 15,0 | 18,5 | 5,2 | 4,3 | 3,5 | — | 0,08 | 0,03 | — | |
Waspaloy | 58,3 | 19,5 | 13,5 | 4,3 | 1,3 | 3,0 | — | 0,08 | 0,006 | 0,06 | |
Astroloy | 55,1 | 15,0 | 17,0 | 5,2 | 4,0 | 3,5 | — | 0,06 | 0,03 | — | |
Rene 41 | 55,3 | 19,0 | 11,0 | 10,0 | 1,5 | 3,1 | — | 0,09 | 0,005 | — | |
Nimonic 80A | 74,7 | 19,5 | 1,1 | — | 1,3 | 2,5 | — | 0,06 | — | — | |
Nimonic 90 | 57,4 | 19,5 | 18,0 | — | 1,4 | 2,4 | — | 0,07 | — | — | |
Nimonic 105 | 53,3 | 14,5 | 20,0 | 5,0 | 1,2 | 4,5 | — | 0,2 | — | — | |
Nimonic 115 | 57,3 | 15,0 | 15,0 | 3,5 | 5,0 | 4,0 | — | 0,15 | — | — |
Сплав | %Ni | %Cr | %Co | %Mo | %Al | %Ti | %Nb | %C | %B | Zr | % др. элементов |
---|---|---|---|---|---|---|---|---|---|---|---|
B-1900 | 64,0 | 8,0 | 10,0 | 6,0 | 6,0 | 1,0 | — | 0,10 | 0,015 | 0,1 | 4,0 % Ta |
MAR-M200 | 60,0 | 9,0 | 10,0 | — | 5,0 | 2.0 | 1.0 | 0,13 | 0,015 | 0,05 | 12,0 % W |
Inconel 738 | 61,0 | 16,0 | 8,5 | 1,7 | 3,4 | 3,4 | 0,9 | 0,12 | 0,01 | 0,10 | 1,7 % Ta, 3,6 % W |
Rene 77 | 58,0 | 14,6 | 15,0 | 4,2 | 4,3 | 3,3 | — | 0,07 | 0,016 | 0,04 | |
Rene 80 | 60,0 | 14,0 | 9,5 | 4,0 | 3,0 | 5,0 | — | 0,17 | 0,015 | 0,03 | 4,0 %W |
Фазовый состав[править | править код]
К основным фазам жаропрочных сплавов относятся:
- Гамма-фаза (γ{\displaystyle \gamma }) является матрицей с г.ц.к. кристаллической решёткой. В твёрдом растворе этой фазы содержится большое количество Co, Cr, Mo, W
- Гамма-штрих (γ{\displaystyle \gamma }’) фаза образует частицы преципитата, имеющего также г.ц.к. кристаллическую решётку. В эту фазу входят такие элементы, как Al и Ti. Объёмная доля этой фазы, когерентной аустенитной матрице достаточно велика
- Карбиды. Содержание углерода в сплавах относительно невелико (0,05-0,2 %). Он соединяется с карбидообразующими элементами — Ti, Ta, Hf
- Зернограничная γ{\displaystyle \gamma }’-фаза. Эта фаза образуется в виде плёнки по границам зёрен в процессе термической обработки.
- Бориды Выделяются по границам зёрен в виде редких частиц
- Фазы т. п. у. (топологически плотно упакованные фазы) имеют пластинчатую морфологию. Пример: фазы σ{\displaystyle \sigma }, μ{\displaystyle \mu } и фаза Лавеса. Эти фазы приводят к охрупчиванию материала и являются нежелательными.
Термическая обработка[править | править код]
Деформируемые никелевые жаропрочные сплавы содержат в матрице дисперсные выделения карбидов типа MC. Гомогенизационный отжиг даёт возможность подготовить матрицу к получению равномерного распределения частиц упрочняющей фазы γ{\displaystyle \gamma }’ в процессе последующего старения. Для примера, для сплава Inco 718 гомогенизационный отжиг продлится в течение 1 часа при 768 °C, а старение проводится в два этапа: 8 часов при 718 °C и 8 часов при 621 °C. После гомогенизационного отжига важно выдержать скорость охлаждения, чтобы препятствовать выделению нежелательных фаз. Охлаждение между этапами старения проводится плавно в течение 2 часов.
Одним из факторов, определяющих жаропрочность, является высокое сопротивление ползучести. Жаропрочность сплавов оценивается пределами длительной прочности или ползучести при высоких температурах, и связана, в первую очередь, с их структурой и составом. По структуре жаропрочные сплавы должны быть многофазными с прочными границами зёрен и фаз[1]. В никелевых жаропрочных сплавах сказанное обеспечивается многокомпонентным легированием. При этом жаропрочность сплавов тем выше, чем больше объёмная доля упрочняющих фаз и чем выше их термическая стабильность, то есть устойчивость против растворения и коагуляции при повышении температуры.
Длительная прочность[править | править код]
Никелевые жаропрочные сплавы используются при температурах 760—980 °C. Литые жаропрочные сплавы имеют высокую длительную прочность при более высоких температурах. Например, сплав MAR-M246 имеет длительную прочность 124 МПа после 1000 часов выдержки при 982 °C.
Жаропрочные сплавы на никелево-железной основе используются при температурах 650—815 °C. Их длительная прочность намного ниже.
Длительная прочность жаропрочных сплавов при трёх температурах, МПа[9]Сплав | 650 °C 100 часов | 650 °C 1000 часов | 815 °C 100 часов | 815 °C 1000 часов | 982 °C 100 часов | 982 °C 1000 часов |
---|---|---|---|---|---|---|
Inconel X-750 | 552 | 469 | 179 | 110 | 24 | |
Udimet 700 | 703 | 400 | 296 | 117 | 55 | |
Astroloy | 772 | 407 | 290 | 103 | 55 | |
IN-100 | 503 | 379 | 172 | 103 | ||
MAR-M246 | 565 | 448 | 186 | 124 |
Монокристаллические жаропрочные сплавы[править | править код]
В 1970—1980 годы началось применение литых жаропрочных сплавов, полученных методами направленной кристаллизации и монокристаллических сплавов на никелевой основе. Применение этих материалов (на никелевой основе) позволило увеличить прочность и термическую долговечность лопаток газовых турбин.
Химический состав жаропрочных сплавов,полученных методами направленной кристаллизации[9]
Сплав | %Cr | %Co | %W | %Mo | %Ta | %Nb | %Ti | %Al | %Hf | %B | %Zr | %C |
---|---|---|---|---|---|---|---|---|---|---|---|---|
MAR-M200+Hf | 9,0 | 10,0 | 12,0 | — | — | 1,0 | 2,0 | 5,0 | 2,0 | 0,015 | 0,08 | 0,14 |
MAR-M246+Hf | 9,0 | 10,0 | 10,0 | 2,5 | 1,5 | — | 1,5 | 5,5 | 1,5 | 0,015 | 0,05 | 0,15 |
MAR-M247 | 8,4 | 10,0 | 10,0 | 0,6 | 3,0 | — | 1,0 | 5,5 | 1,4 | 0,015 | 0,05 | 0,15 |
RENE 80H | 14,0 | 9,5 | 4,0 | 4,0 | — | — | 4,8 | 3,0 | 0,75 | 0,015 | 0,02 | 0,08 |
Сплав | %Cr | %Co | %W | %Mo | %Ta | %Nb | %Ti | %Al | %Hf |
---|---|---|---|---|---|---|---|---|---|
Pratt & Whitney № 1 | 10,0 | 5,0 | 4,0 | — | 12,0 | — | 1,5 | 5,0 | — |
Pratt & Whitney № 2 (3 % Re) | 5,0 | 10,0 | 6,0 | 2,0 | 8,7 | — | — | 5,6 | 0,1 |
CMSX-2 | 8,0 | 5,0 | 8,0 | 0,6 | 6,0 | — | 1,0 | 5,5 | — |
SRR99 | 8,5 | 5,0 | 9,5 | — | 2,8 | — | 2,2 | 5,5 | — |
Уже ранний опыт эксплуатации лопаток газотурбинных двигателей Jumo-004 показал (исследования К. Гебхардт, фирма Крупп, Эссен), что на практике срок службы лопаток определяется усталостной прочностью, и подавляющее число разрушений лопаток являются усталостными[10].
Ещё в начале XX века компанией Хэйнс (англ. Haynes) были получены патенты на сплавы системы Co — Cr и Co — Cr — W. Эти сплавы, именуемые «стеллитами» использовались вначале для производства режущего инструмента. и износостойких деталей. В 1930-х годах был разработан литейный Co — Cr — Mo сплав для зубного протезирования Vitallium. Аналогичный по составу сплав HS-21 начал использоваться десятилетие спустя в турбонагревателях и газовых турбинах. Тогда же начали использовать сплав системы Co — Ni — Cr для направляющих лопаток газотурбинных двигателей. В 1943 г. был разработан литейный сплав Co — Ni — Cr — W (X-40) также применяемый при изготовлении лопаток. В 1950—1970 годы были разработаны новые никелевые жаропрочные сплавы, изготовленные путём вакуумной выплавки и упрочняемые за счёт выделения фазы γ{\displaystyle \gamma }’. Это привело к уменьшению использования сплавов на основе кобальта.
Особенности жаропрочных сплавов на кобальтовой основе[править | править код]
- Температура плавления у сплавов на кобальтовой основе — более высокая. По этой причине повышены характеристики длительной прочности. Эти жаропрочные сплавы могут работать при более высоких температурах, по сравнению со сплавами на основе никеля и железа
- Высокое содержание хрома повышает сопротивление горячей коррозии
- Сплавы характеризуются повышенным сопротивлением термической усталости и имеют хорошую свариваемость.
Дисперсноупрочненные жаропрочные сплавы[править | править код]
Важной проблемой в разработке конструкционных материалов с повышенной прочностью и пластичностью является обеспечение их стабильности и однородности физико-механических свойств во всем интервале температур эксплуатации от криогенных и вплоть до предплавильных температур. В настоящее время наиболее перспективным путем решения этой проблемы является упрочнение базового сплава дисперсными наночастицами тугоплавких оксидов[источник не указан 627 дней]. Такие материалы принято называть ODS (oxide dispersion strengthened) сплавами[11]. Базой для ODS-сплавов наиболее часто служат аустенитные жаропрочные сплавы на основе Ni, Cr и Fe. В качестве упрочняющих частиц, как правило, используют тугоплавкие оксиды Al2O3, TiO2, ThO2, La2O3, BeO и Y2O3. ODS- суперсплавы получают методом механического легирования, который включает следующие стадии: 1) совместное перемалывание в шаровых мельницах порошков исходных компонент суперсплава с добавлением мелкодисперсных конгломератов тугоплавкого оксида; 2) запайка дегазированного порошка в герметичный стальной контейнер; 3) компактирование экструзией; 4) горячая опрессовка; 5) зонная рекристаллизация. ODS- суперсплав (Inconel MA758) на основе оксида иттрия Y2O3 был разработан в 90-х годах прошлого века.
Поскольку турбинные лопатки, изготовленные из литейных жаропрочных сплавов работают при высоких температурах и в агрессивной среде, возникает необходимость в их защите от горячей коррозии. С этой целью используют диффузионные покрытия двух типов, т. н. пакетная цементация и покрытия, наносимые в газовой фазе. В процессе покрытия происходит обогащение поверхностного слоя алюминием и образование алюминида никеля, как матрицы покрытия.
Процесс пакетной цементации[править | править код]
Процесс происходит при более низкой температуре (около 750 °C). Детали помещаются в коробки со смесью порошков: активный материал, содержащий алюминий и образующий покрытие, активатор (хлорид или фторид) и термический балласт, например, окись алюминия. При высокой температуре образуется газообразный хлорид (или фторид) алюминия, который переносится на поверхность изделия. Затем происходит распад хлорида алюминия и диффузия алюминия вглубь объема. Образуется т. н. «зелёное покрытие», очень хрупкое и тонкое. После этого проводится диффузионный отжиг (несколько часов при температурах около 1080 °C). При этом образуется окончательное покрытие.
Покрытие в газовой фазе[править | править код]
Процесс идёт при более высокой температуре около 1080 °C. Активный материал, содержащий алюминий, не находится в непосредственном контакте с изделием. Нет необходимости и в термическом балласте. Процесс отличается диффузией вовне. Также требуется диффузионный отжиг.
Более современной технологией защиты лопаток является плазменное напыление термобарьерных покрытий. Как правило, термобарьерное покрытие состоит из нескольких слоев — подслой, слой MeCrAlY, слой керамики (часто применяют оксид циркония, стабилизированный иттрием). Для разных двигателей аттестованы вакуумное или атмосферное плазменное напыление, однако все современные разработки выполняются на атмосферной плазме, как более дешевой в эксплуатации.
- ↑ 1 2 Авиация. Энциклопедия. М.: Большая Российская энциклопедия, 1994, с. 201
- ↑ Luft.-Forschung, Bd 18(1941), N 8, S. 275—279
- ↑ Pomp A., Krisch A.: Zur Frage der Dauerstandfestigkeit warmfester Staehle bei 600, 700 und 800 °C. Mitteilungen der KWI fuer Eisenforschung (Abhandl. 400), 1940
- ↑ Report on Visit to Germany and Austria to investigate Alloys for Use at High Temperature. BIOS Final Report N 396, London, 1946
- ↑ 1 2 Giamei A.F., Pearson D.D., Anton D.L. Materials Research Society Symposium Proc. 1985, v. 39, pp. 293—307
- ↑ Туманов А. Т., Шалин Р. Е., Старков Д. П. Авиационное материаловедение. — в кн.: Развитие авиационной науки и техники в СССР. Историко-технические очерки. М.: Наука, 1980, с. 332—334
- ↑ Суперсплавы II под ред. Симса, Столоффа, Хагеля. Перевод на русский язык. М., Металлургия, 1995, т 1, стр. 29
- ↑ http://www.msm.cam.ac.uk/phase-trans/2003/nickel.html
- ↑ 1 2 3 4 Superalloys
- ↑ Report on Visit to Germany and Austria to investigate Alloys for use at a High Temperatures/ — BIOS Final Report No 396. London 1946, p. 13.
- ↑ К.А. Ющенко, Ю.А. Семеренко, Е.Д. Табачникова, А.В. Подольский, Л.В. Скибина, С.Н. Смирнов, В.С. Савченко. Inconel MA758: новый наноструктурный суперсплав. Акустические и механические свойства в интервале температур 4,2—310 К // Металлофиз. новейшие технол. — 2013. — Т. 35, вып. 2. — С. 225-231.
- Суперсплавы II. Жаропрочные материалы для аэрокосмических и промышленных энергоустановок. — М.: «Металлургия», 1995.
- Строение и свойства авиационных материалов. — М.: «Металлургия», 1989.
- Лекции о суперсплавах на сайте университета Кембриджа.
- Химушин Ф. Ф. Жаропрочные стали и сплавы. — М.: «Металлургия», 1969.
Огнеупорная термостойкая (жаростойкая) плитка для печи и камина: описание
Для защиты наружных поверхностей бытового печного оборудования, промышленных отопительных установок от внешних механических повреждений, сильного нагрева, для исключения случаев ожогов людей используют огнестойкие покрытия, выполненные из натурального камня, керамической продукции, элементы из огнеупорного (огнестойкого) бетона.
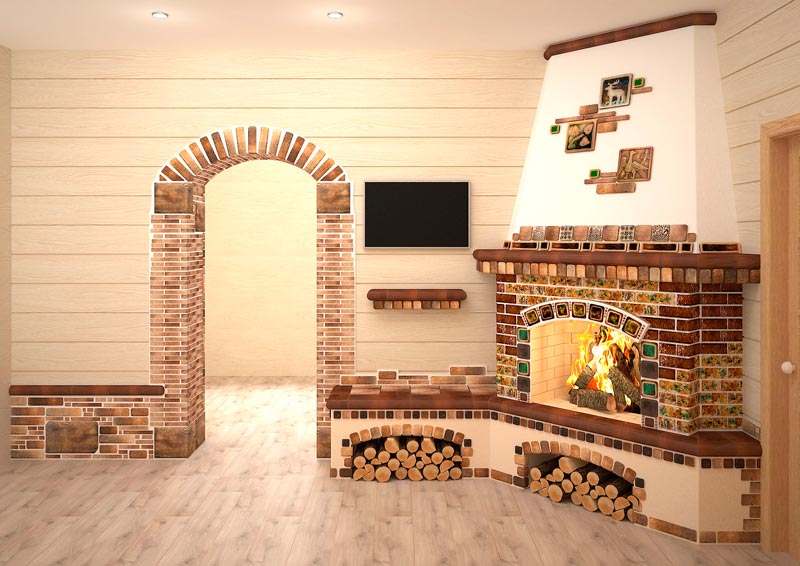
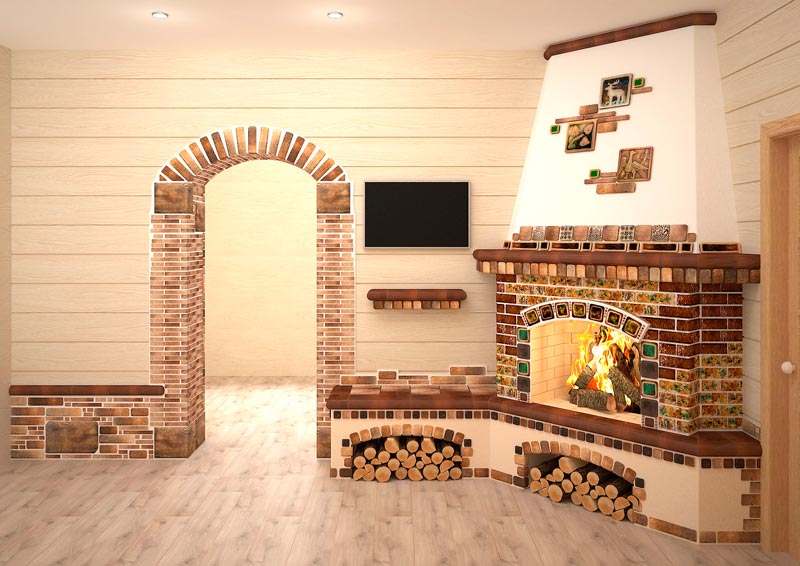
Что такое и назначение
Огнеупорная плитка – это, согласно определениям приведенным в ГОСТ 28874-2004 и ГОСТ Р 52918-2008, разновидность формованных огнеупорных материалов (изделий), так как она характеризуется определенными геометрическими формами, типовыми размерами, имеющимися у всей серийной продукции.
Основное назначение плитки, изготовленной как из натуральных отделочных пород камней, так и из искусственных керамических материалов, независимо от ее видов, будь она потолочная, фасадная или напольная – это декоративная, защитная облицовка поверхностей строительных конструкций, отопительного бытового, промышленного оборудования, среди которых печь, камин, без которых невозможна современная баня, сауна, жилой или дачный дом.
Керамическая жаростойкая плитка является многофункциональной продукцией, позволяющей решить несколько задач, стоящих перед заказчиками – от строителей, возводящих объекты различного назначения, до собственников частной недвижимости:
- Создать неповторимый интерьер в жилом, дачном доме, бане, сауне, использовав подходящую/понравившуюся по внешнему виду, фактуре, цвету, рисунку огнеупорную плитку для декоративной облицовки внешних поверхностей печей, каминов, включая противопожарные разделки и отступки; а также стационарных мангалов, барбекю, размещенных на приусадебных участках.
- Обеспечить защиту от перегрева отопительного оборудования, снизить возможность получения термических повреждений людьми, пользующимися им в быту, на производстве.
- Повысить теплоемкость печей, каминов, увеличить равномерную теплоотдачу агрегатов отопления за счет создания ровных, гладких наружных поверхностей, эффективно выполняющих роль тепловых экранов.
Свойства и характеристики
Любые виды (типы) огнеупорной плиточной продукции, независимо от материалов, способов их изготовления, должны обладать свойствами, предъявляемыми строительными, противопожарными, санитарными нормами:
- Огнестойкостью – способностью выдерживать кратковременное температурное воздействие до 1000 ℃.
- Максимальной температурой нагрева на внешней поверхности в период эксплуатации в нормальных условиях, что в зависимости от категории, назначения печного оборудования варьируется в диапазоне от 100 ℃ (умеренный нагрев) до 120℃ (высокотемпературный нагрев). Значение предельных температур для каждого вида огнеупорной плитки определяется в ходе испытаний, указывается в сопроводительной технической документации на каждую партию продукции.
- Отсутствием в составе токсичных веществ, в том числе образующихся при высокотемпературном нагреве, что решается использованием огнеупорного натурального сырья или природных материалов без вредных примесей.
- Теплопроводностью, теплоемкостью, важными свойствами, позволяющими не уменьшить теплоотдачу печного оборудования, выполненного из огнеупорного кирпича.
- Малой пористостью, высокой плотностью, низким показателем водопоглощения, так все эти свойства неразрывно связаны.
- Прочностью на излом, точечную ударную нагрузку.
- Стойкостью окрасочных слоев, эмалевых покрытий к внешним воздействиям.
- Устойчивостью к выгоранию первоначальных цветов, рисунков.
Технические характеристики:
- Типовые размеры продукции, оптимальным из которых считается 120х120 мм.
- Толщина – до 8 мм.
- Коэффициент теплового расширения – не больше 8 %.
Не стоит забывать о внешней эстетичности, приемлемой стоимости огнеупорной плитки, что часто служат основными критериями при ее выборе.
Виды
Для облицовки используют два общих вида (группы) огнеупорной плитки, различающиеся материалами и способами изготовления:
- Из натуральных материалов – мрамора, гранита, диабаза, базальта, кварцита, изготовленные с применением режущего промышленного оборудования.
- Искусственная керамика, производимая из огнеупорного сырья, проходящая длительный цикл от его добычи до обжига готовых штучных материалов. Среди них, согласно ГОСТ Р 52918, различают глазурованные огнеупорные изделия, с нанесенным стекловидным защитным слоем – глазурью; бикерамические плитки, спрессованные из нескольких слоев огнеупоров различного минерально-химического состава.
Востребованы заказчиками следующие виды огнеупорной плитки:
- Терракотовая, являющаяся имитацией натурального камня, кирпича, характеризующаяся шершавой поверхностью. Выпускаются глазурованные варианты. Производится из высокоплотной каолиновой глины. Не боится влаги, поэтому применяется не только внутри помещений, включая бани, сауны, но и снаружи. Отличается прочностью, долговечностью, высокой теплоотдачей, адгезией при укладке, жаростойкостью, легкостью в уходе, относительно невысокой стоимостью.
- Майолика – это глазурованная плитка с пористой структурой, проходящая при производстве обжиг дважды – до и после нанесения рисунка. Традиционные цвета – белый и синий. Не рекомендована для укладки в помещениях бань, саун из высокого коэффициента водопоглощения. Зачастую это плитка ручной росписи, поэтому цены на изделия высокие.
- Кафельная плитка – это недорогой, однако, не самый удачный выбор для облицовки печей. Хотя она огнеупорна, но часто трескается, не выдерживая резких перепадов температуры, в том числе в сезонно отапливаемых помещениях – банях, домах на дачных участках, где она может просто осыпаться.
- Клинкерная плитка с матовой или глазурованной поверхностью производится из нескольких видов огнеупорных глин. Долговечна, не выгорает со временем.
- Изразцы в разрезе имеют коробчатую форму с бортиками, имеют как гладкую, так и рифленую поверхность, покрытую эмалью или глазурью. Характеризуются отличной теплоотдачей, прекрасным внешним видом, большим количеством выпускаемых элементов декора, позволяющими создать при облицовке каминов, печей произведения искусства. Так как большая часть изразцов – это результаты ручного труда, соответственно, высока стоимость этого вида огнеупорной плитки
- Шамотная – это наиболее жаростойкий вариант плитки для облицовки, устойчивый к любым внешним воздействиям. Если раньше шамотные огнеупоры использовали в основном в промышленности, то теперь выпускается плитка и для бытовых целей.
- Керамогранит – это искусственный камень, имитирующий как натуральные породы, такие как мрамор, гранит, так и терракот, майолику. Выпускается стандартной, сложной геометрической формы.
- Мрамор отлично поддается обработке, шлифовке, веками используется для внутренней отделки интерьера помещений, в том числе при облицовке каминов, печей. Это дорогой, но практически вечный материал можно увидеть, как снаружи, так и внутри многих историко-архитектурных памятников.
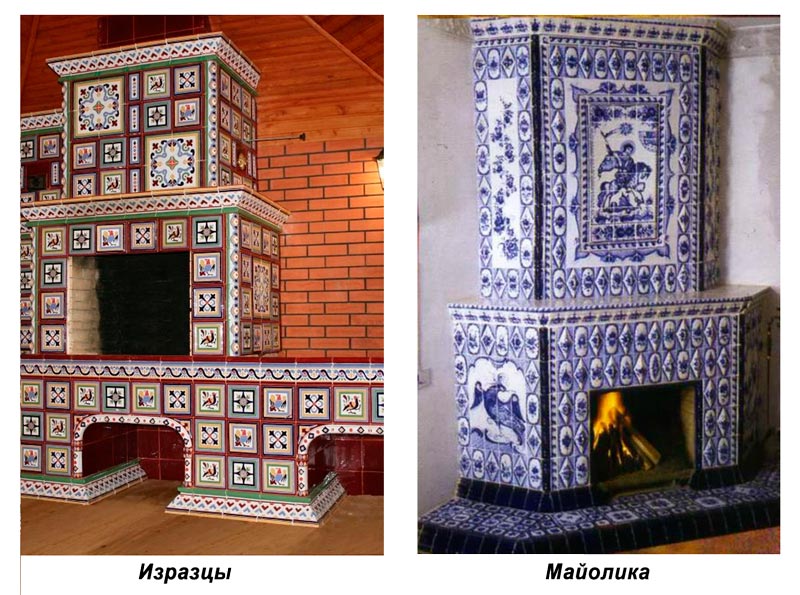
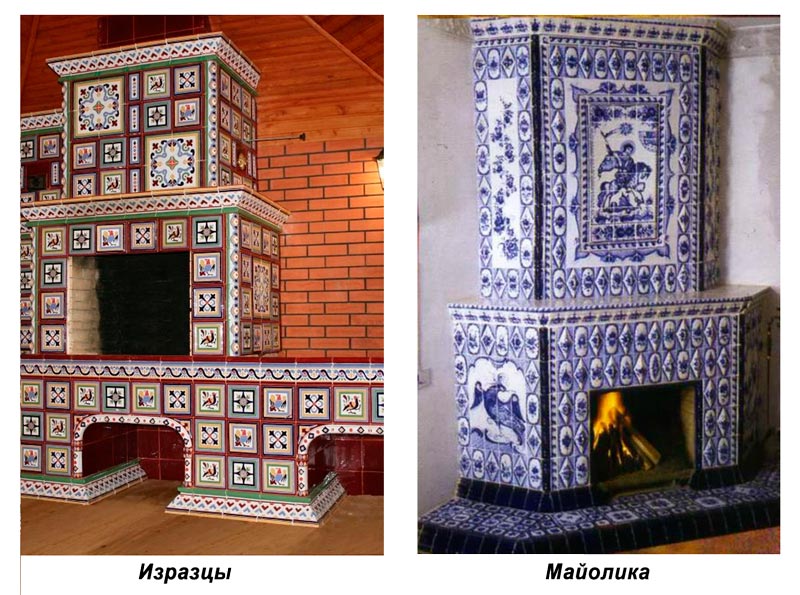
Правила выбора и критерии
Выбор огнеупорного материала для выполнения наружной облицовки камина, печи в бане, жилом частном, в том числе загородном доме должен проводиться прежде всего с учетом того, подходит ли он по своим свойствам, техническим характеристикам, химическому составу к тому виду поверхности, на которую необходимо уложить термостойкую плитку.
Конечно, важен и внешний вид, обязательно оптимальное сочетание рисунков, цветовых решений выбранной огнеупорной плитки с основной оттеночной гаммой дизайна интерьера сауны, кухни или гостиной, необходимо определиться матовой, глазурованной, плоской или рельефной будет ее лицевая поверхность.
Неоценимую помощь в решении этого комплексного вопроса могут оказать печные мастера, специалисты по отделке помещений, которым обычно необходима визуальная оценка печного оборудования, а также работники торговых организаций, реализующих плиточную продукцию.
При самостоятельном выборе стоит учитывать следующие критерии, которым должна отвечать качественная огнеупорная плитка, изготовленная в соответствии с техническими условиями серийного производства:
- Средняя толщина штучного изделия – 6–8 мм. Более тонкая плитка является хрупкой, с толстой могут возникнуть проблемы как при укладке, так и в процессе последующей эксплуатации печного оборудования из-за падения тепловой отдачи в воздушную среду помещения.
- Геометрические размеры плитки как в одной упаковке, так и в выбранной для приобретения партии продукции, должны быть идентичными, в противном случае усложнится процесс укладки, пострадает внешний вид готовых поверхностей. Проверка габаритов, ровности огнеупорной плитки прост: достаточно приложить два изделия лицевой, потом внутренней стороной друг к другу, чтобы понять, насколько они совпадают, нет ли между ними просвета, указывающего на кривизну поверхностей.
- Лицевая сторона плитки не должна иметь как механических повреждений, так следов заводского брака – каверн, неровностей на гладкой поверхности, неполного глазурования; а также несовпадения, изменения цвета, рисунка в пределах выбранной партии товара.
- Обнаруженные при отборе на отдельных штучных изделиях трещины, сколы – это тревожный сигнал, что продукция является очень хрупкой, легко повреждается, поэтому велика вероятность того, что в процессе эксплуатации при высокотемпературном воздействии может лопнуть лицевая сторона отдельных огнеупорных плиток, либо часть купленного товара пострадает еще при транспортировке до места кладочных работ.
При выборе следует не смешивать огнеупорную плитку разных видов, производителей, так как их свойства, технические параметры, несмотря на внешнее сходство, могут сильно различаться, а это может фатально сказаться в процессе эксплуатации, например, из-за разного коэффициента теплового расширения, что зачастую приводит к обрушению фрагментов печной облицовки.
Лучший вариант выбора – это огнеупорная плитка с элементами декора в одной цветовой, оттеночной гамме от одного производителя, не отличающаяся по свойствам, техническим характеристикам. При заказе, приобретении необходим излишек по площади в 10-15%, так как часть материала неизбежно уйдет в отходы при обрезке, а оставшееся количество станет запасом для замены случайно поврежденных плиток в процессе длительной эксплуатации.
Клей для укладки
Так как штукатурные, клеевые смеси на основе цементного связующего начинают быстро терять свои свойства при сильном нагреве, разрушаться, то для укладки всех огнеупорных видов плиточной продукции необходимо использовать специальные огнестойкие клеи, мастики, в основном приготовленные из тонкодисперсной шамотной глины с различными модифицирующими добавками.
Кроме огнестойких клеев, следует также использовать жаростойкие затирки для заполнения швов.
Особенности укладки
Огнеупорную плитку применяют для облицовки как вновь возведенных отопительных агрегатов, так и для обновления внешнего вида эксплуатируемого оборудования, ведь с ее помощью можно преобразить любой интерьер, чему способствует огромное количество готовой продукции, вариантов укладки плитки.
Залогом успеха служат:
- Правильный выбор материала по толщине, размерам, сочетанию цветовых решений, рисунков.
- Неукоснительное выполнение всего комплекса подготовительных работ.
- Аккуратная кладка плитки.
- Правильный уход в процессе эксплуатации.
Процессу укладки огнеупорной плитки, в отличие от ее напольных, настенных аналогов, эксплуатирующихся при нормальной температуре, присущи свои особенности:
- Проведение тщательной очистки внешней поверхности печного оборудования от потеков кладочного раствора, пыли. При подготовке к облицовке ранее эксплуатировавшихся печей, каминов необходимо полностью удалить старую штукатурку, плитку, следы клея с кирпичных поверхностей.
- Произвести увлажнение малярной кистью для удаления мелкой пыли.
- Выполнить проверку ровности кирпичной кладки при помощи отвеса, строительного уровня.
- При необходимости для выравнивания поверхностей использовать стекловолоконную сетку с последующим шпатлеванием слоем огнеупорной мастики или нанести на нее клеевую термостойкую смесь.
- Приготовить раствор термически стойкого клея, необходимого для укладки огнеупорной плитки, а также пластиковые крестики для контроля ширины швов.
- Нанести шпателем клей ровным слоем на тыльную поверхность плитки, удалив излишки. Слой наносимого клея не должен превышать 10 мм, иначе велик шанс появления трещин после прогрева печного отопления, в процессе последующей эксплуатации.
- Аккуратно клеить плитку на подготовленную поверхность, плотно прижимая ее к ней.
- Затирка швов – это заключительный этап укладки, также требующий внимательности и аккуратности, ведь от его результатов во многом будет зависеть, как выглядит получившаяся отделка печи, камина или стационарного мангала.
Уход за выложенной огнеупорной плиткой не требует особого труда, достаточно по мере необходимости убирать загрязнения с помощью мыльного раствора, тщательно вытирая поверхности после влажной уборки. Но, ни в коем случае не стоит использовать моющие растворы с абразивными частицами, так как ими можно повредить глазурованные, гладкие поверхности огнеупорной плитки.