История производства и использования железа — Википедия
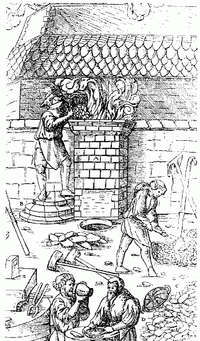
История производства и использования железа берёт своё начало в доисторической эпохе, скорее всего, с использования метеоритного железа. Выплавка в сыродутной печи применялась в XII веке до н. э. в Индии, Анатолии и на Кавказе. Также отмечается использование железа при выплавке и изготовлении орудий и инструментов в 1200 году до н. э. в Африке южнее Сахары[2][3]. Уже в первом тысячелетии до н. э. использовалось кованое железо (англ. Wrought iron). Об обработке железа упоминается в первой книге Библии (Быт. 4:22).
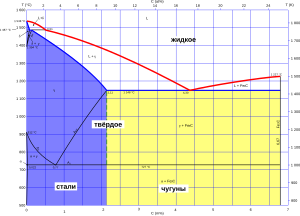
Материал, в обиходе называемый «железом», как правило, является сталью или чугуном и представляет собой сплав железа (Fe), как химического элемента, с углеродом (C). Кроме железа и углерода сплав содержит незначительные количества других химических элементов.
При концентрации углерода в сплаве менее 0,3 % получается мягкий пластичный тугоплавкий (температура плавления железа 1539 °C) сплав, за которым и закрепляется название его основного ингредиента — железа. Представление о том железе, с которым имели дело наши предки, сейчас можно получить, исследовав механические свойства гвоздя.
При концентрации углерода в сплаве от 0,3 до 2,14 % сплав называется «сталью». В первозданном виде сталь походит по своим свойствам на железо, но, в отличие от него, поддается закалке: при резком охлаждении после нагрева до определённых температур сталь приобретает большую твёрдость — замечательное достоинство, однако, почти совершенно сводимое на нет приобретённой в процессе той же закалки хрупкостью.
При концентрации углерода в сплаве свыше 2,14 % сплав называется «чугуном». Чугун — хрупкий легкоплавкий сплав, пригодный для литья, но не поддающийся обработке ковкой. Чугун насыщен графитовыми включениями, делающими его неоднородным и механически непрочным. Температура плавления чугуна варьируется от 1150 до 1300 °C.
Технологии производства и обработки железа и сплавов[править | править код]
Для производства железа исторически применялось несколько технологий, которые сложно расположить в хронологическом порядке.
Метеоритное железо[править | править код]
Сыродутная печь[править | править код]
Первым устройством для получения железа из руды стала одноразовая сыродутная печь (сыродутный горн, домница). Несмотря на наличие недостатков способ получения железа с использованием такой печи долгое время оставался единственным способом получения железа из руды. На Руси появление первых домниц относят к IX веку[5].
Впервые железо научились обрабатывать народы Анатолии. Древние греки считали, что открывателями железа был народ халибов. В литературе этот народ назывался устойчивым выражением «отец железа». Слово «сталь» на греческом языке («Χάλυβς») происходит от этого этнонима.
«Железная революция» началась на рубеже I тысячелетия до нашей эры в Ассирии. Железные мечи научились изготавливать представители Гальштатской культуры. С VIII века до нашей эры сварочное железо быстро стало распространяться в Европе, в III веке до нашей эры оно вытеснило бронзу в Галлии, во II веке новой эры появилось в Германии, а в VI веке уже широко употреблялось в Скандинавии; племенами же, проживающими на территории будущей Руси — киммерийцами, а позже скифами и сарматами — железо использовалось ещё до н. э.. В Японии железный век наступил только в VII веке нашей эры.
Известный популяризатор науки Айзек Азимов так описывает историю перехода человечества из бронзового века в железный[6]:
![]() | Где-то около XV—XIV вв. до н. э. техника выплавки и науглероживания железа была разработана в кавказских предгорьях в Урарту. Эта страна находилась тогда под властью Хеттского царства, которое находилось на высшей точке своей мощи. Хеттские цари тщательно охраняли монополию на новую технику, ибо понимали её важность. Вначале получали только маленькие партии железа, и в течение нескольких столетий оно стоило порой в сорок раз дороже серебра. Но ещё до того, как выплавку можно было увеличить, а хеттам — этим воспользоваться, им пришёл конец. Хеттское царство было разрушено во время беспорядков, последовавших за движением «народов моря», и хеттская монополия на железо была нарушена. Технология выплавки железа быстро распространялась в том числе, конечно, в Ассирию, которая граничила с «железным царством» Урарту. | ![]() |
Первым шагом в зарождающейся чёрной металлургии было получение железа путём восстановления его из окиси. Болотная руда перемешивалась с древесным углём и закладывалась в печь. При высокой температуре, создаваемой горением угля, углерод начинал соединяться не только с атмосферным кислородом, но и с тем кислородом, который был связан с атомами железа.
После выгорания угля в печи оставалась так называемая «крица» — комок пористого восстановленного железа с примесью большого количества шлаков. Крицу потом снова разогревали и подвергали обработке ковкой, выколачивая шлак из железа. Полученный брусок железа (в котором всё же оставалось 2—4 % шлака) назывался «кричной болванкой». Долгое время ковка была основным процессом в технологии производства железа, причём, с приданием изделию формы она была связана в последнюю очередь. Ковкой получался сам материал.
Сварное оружие[править | править код]
Сталь производилась уже из готового железа путём насыщения углеродом последнего. При высокой температуре и недостатке кислорода углерод, не успевая окисляться, пропитывал железо. Чем больше было углерода, тем твёрже оказывалась сталь после закалки.
Как можно было заметить, ни один из перечисленных выше сплавов не обладает таким свойством, как упругость. Железный сплав может приобрести это качество, только если в нём возникает чёткая кристаллическая структура, что происходит, например, в процессе застывания из расплава. Проблема же древних металлургов заключалась в том, что расплавить железо они не могли. Для этого требуется разогреть его до 1540 °C, в то время как технологии древности позволяли достичь температур в 1000‑1300 °C. Вплоть до середины XIX века было невозможно расплавить железо и сталь с содержанием углерода менее 0,4 %, так как плавкость железных сплавов снижается по мере уменьшения концентрации углерода.
Таким образом ни железо, ни сталь сами по себе для изготовления оружия не годились. Орудия и инструменты из чистого железа выходили слишком мягкими, а из чистой стали — слишком хрупкими. Потому, чтобы изготовить, например, меч, приходилось делать «бутерброд» из двух пластин железа, между которыми закладывалась стальная пластина. При заточке мягкое железо стачивалось и появлялась стальная режущая кромка.
Такое оружие, сваренное из нескольких слоёв с разными механическими свойствами, называлось сварным. Общими недостатками этой технологии являлись излишняя массивность и недостаточная прочность изделий. Сварной меч не мог пружинить, вследствие чего неизбежно ломался или гнулся при ударе о непреодолимую преграду.
Отсутствием упругости недостатки сварного оружия не исчерпывались. В дополнение к упомянутым недостаткам, его, например, невозможно было «толком» заточить. Железу можно было придать какую угодно остроту (хотя и стачивалось оно быстро), но и тупилась мягкая режущая кромка из железа почти мгновенно. Сталь же точиться не желала — режущая кромка крошилась. Здесь налицо полная аналогия с карандашами — мягкий грифель легко сделать острым, но он сразу затупится, а твёрдый до особой остроты не доведёшь — десять раз сломается. Так что, бритвы приходилось делать из железа и затачивать заново ежедневно.
В целом же сварное оружие не превосходило остротой столовый нож. Уже одно это обстоятельство требовало делать его достаточно массивным для придания удовлетворительных рубящих свойств.
Единственной мерой, позволяющей достичь сочетания остроты и твёрдости в рамках технологии сварки, была закалка изделия уже после его заточки. Применим же этот метод становился в случае, если стальная режущая кромка приваривалась просто к железному обуху, а не заключалась в «бутерброд» из железа. Либо после заточки могли быть закалены клинки, у которых железный сердечник покрывался снаружи сталью. Недостатком такого метода было то, что заточка оказывалась возможна лишь однажды. Когда стальное лезвие повреждалось и тупилось, весь клинок приходилось перековывать.
Тем не менее именно освоение техники сварки — несмотря на все её недостатки — произвело настоящий переворот во всех сферах человеческой деятельности и привело к огромному возрастанию производительных сил. Сварные орудия были вполне функциональны и, при том, общедоступны. Только с их распространением каменные орудия оказались окончательно вытеснены, и наступил век металла.
Железные орудия решительно расширили практические возможности человека. Стало возможным, например, строить рубленные из брёвен дома — ведь железный топор валил дерево уже не в три, как медный, а в 10 раз быстрее, чем каменный. Широкое распространение получило и строительство из тёсаного камня. Он, естественно, употреблялся и в эпоху бронзы, но большой расход сравнительно мягкого и дорогого металла решительно ограничивал такие эксперименты. Значительно расширились также и возможности земледельцев.
Булатная сталь и дамаск[править | править код]
Увидеть железо жидким металлурги смогли только в XIX веке, однако ещё на заре железной металлургии — в начале I тысячелетия до нашей эры — индийские мастера сумели решить проблему получения высокоуглеродистой стали с композитной структурой. Такую сталь называли булатом, но из-за сложности изготовления и отсутствия необходимых материалов в большей части мира эта сталь так и осталась индийским секретом на долгое время.
Более технологичный путь получения упругой стали, при котором не требовались ни особо чистая руда, ни графит, ни специальные печи, был найден в Китае во II веке нашей эры. Сталь перековывали до двенадцати раз, при каждой ковке складывая заготовку вдвое, в результате чего получался отличный оружейный материал, называемый «дамаском», из которого, в частности, делались японские катаны (мечи). Количество слоёв стали рассчитывается по формуле A=2Nx{\displaystyle A=2^{N}x}, где N{\displaystyle N} — количество проковок, а x{\displaystyle x} — изначальное количество видов (слоёв) стали, сковываемой в «бутерброд». При каждой ковке количество слоёв удваивалось, а после 12 проковок количество слоёв достигало 4096, и слои становились неразличимы.
Штукофен[править | править код]
Более высокую, по сравнению с сыродутной печью, ступень в развитии чёрной металлургии представляли собой постоянные высокие печи, называемые в Европе штукофенами. Это действительно была высокая печь — с четырёхметровой трубой для усиления тяги. Мехи штукофена «качались» уже несколькими людьми, а иногда и водяным двигателем. Штукофен имел дверцы, через которые раз в сутки извлекалась крица.
Изобретены штукофены были в Индии в начале первого тысячелетия до новой эры. В начале нашей эры они попали в Китай, а в VII веке вместе с «арабскими» цифрами арабы заимствовали из Индии и эту технологию. В конце XIII века штукофены стали появляться в Германии и Чехии (а ещё до того были на юге Испании) и в течение следующего века распространились по всей Европе.
Производительность штукофена была несравненно выше, чем сыродутной печи — в день он давал до 250 кг железа, а температура в нём оказывалась достаточна для науглероживания части железа до состояния чугуна. Однако штукофенный чугун при остановке печи застывал на её дне, смешиваясь со шлаками, а очищать металл от шлаков умели тогда только ковкой, но как раз ей-то чугун и не поддавался. Его приходилось выбрасывать.
Иногда, впрочем, штукофенному чугуну пытались найти какое-то применение. Например, древние индусы отливали из грязного чугуна гробы, а турки в начале XIX века — пушечные ядра. Трудно судить, сколь хорошими были гробы, но ядра из него получались невысокого качества.
Ядра для пушек из железистых шлаков в Европе отливали ещё в конце XVI века. Из литой брусчатки делались дороги. В Нижнем Тагиле до сих пор сохранились здания с фундаментами из литых шлаковых блоков[7].
Блауофен[править | править код]
Металлурги давно заметили связь между температурой плавления и выходом продукта — чем выше была температура, тем большую часть содержащегося в руде железа удавалось восстановить. Потому рано или поздно им приходила мысль улучшить штукофен — добавить предварительный подогрев воздуха и увеличить высоту трубы. В середине XV века в Европе появились печи нового типа — блауофены, которые сразу преподнесли сталеварам неприятный сюрприз.
Более высокая температура действительно значительно повысила выход железа из руды, но она же повысила и долю железа науглероживающегося до состояния чугуна. Теперь уже не 10 %, как в штукофене, а 30 % выхода составлял чугун — «свиное железо», ни к какому делу не годное. В итоге, выигрыш часто не окупал модернизации.
Блауофенный чугун, как и штукофенный, застывал на дне печи, смешиваясь со шлаками. Он выходил несколько лучшим, так как его самого было больше, следовательно, относительное содержание шлаков выходило меньше, но продолжал оставаться малопригодным для литья. Чугун, получаемый из блауофенов, оказывался уже достаточно прочен, но оставался ещё очень неоднородным. Из него выходили только предметы простые и грубые — кувалды, наковальни, пушечные ядра.
Кроме того, если в сыродутных печах могло быть получено только железо, которое потом науглероживалось, то в штукофенах и блауофенах внешние слои крицы оказывались состоящими из стали. В блауофенных крицах стали было даже больше, чем железа. С одной стороны, это было хорошо, но вот отделить сталь от железа оказалось весьма затруднительно. Содержание углерода становилось трудно контролировать. Только долгой ковкой можно было добиться однородности его распределения.
В своё время, столкнувшись с этими затруднениями, индусы не стали двигаться дальше, а занялись тонким усовершенствованием технологии и пришли к получению булата. Но индусов в ту пору интересовало не количество, а качество продукта. Европейцы, экспериментируя с чугуном, скоро открыли передельный процесс, поднявший металлургию железа на качественно новый уровень.
Доменная печь[править | править код]
Следующим этапом в развитии металлургии стало появление доменных печей. За счёт увеличения размера, предварительного подогрева воздуха и механического дутья, в такой печи всё железо из руды превращалось в чугун, который расплавлялся и периодически выпускался наружу. Производство стало непрерывным — печь работала круглосуточно и не остывала. За день она выдавала до полутора тонн чугуна. Перегнать же чугун в железо в горнах было значительно проще, чем выколачивать его из крицы, хотя ковка все равно требовалась — но теперь уже выколачивали шлаки из железа, а не железо из шлаков.
Хотя найденные в Китае чугунные изделия восходят к V веку до нашей эры[8], самые ранние доменные печи, производящие чугун в «чушках» (слитках), который мог переплавляться в очищенный чугун в вагранках, датируются III—II веками до нашей эры. Подавляющее большинство обнаруженных ранних мест доменного производства относятся к периоду после введения государственной монополии на соль и железорудную промышленность в 117 году до нашей эры (период правления императора У-ди, 141—87 до н. э.) в эпоху династии Хань (202 год до нашей эры — 220 год нашей эры). Большинство железоделательных мест, открытых до 117 года до нашей эры, занимались лишь литьём из заготовок, выплавленных в доменных печах в других районах, отдалённых от населённых пунктов[9][10].
В Европе доменные печи впервые были применены на рубеже XV—XVI веков. На Ближнем Востоке и в Индии эта технология появилась только в XIX веке (в значительной степени, вероятно, потому, что водяной двигатель из-за характерного дефицита воды на Ближнем Востоке не употреблялся). Наличие в Европе доменных печей позволило ей обогнать в XVI веке Турцию если не по качеству металла, то по валу. Это оказало несомненное влияние на исход борьбы, особенно когда оказалось, что из чугуна можно лить пушки.
Георгий Агрикола так описывает средневековую технологию плавки[11]:
![]() | Обычай выдающихся плавильщиков, умеющих управлять четырьмя элементами (имеются в виду земля, воздух, огонь и вода — вне цитаты), таков. Они смешивают в правильных пропорциях руды, содержащие земли, и загружают их в печи. Затем льют нужное количество воды и умело управляют движением воздуха, поступающего из мехов, забрасывая руду туда, где огонь горит с наибольшей силой. Мастер равномерно обрызгивает водой внутреннее пространство печи, слегка увлажняя древесный уголь с тем, чтобы к нему приставали мелкие частицы руды; иначе эти частицы приводятся в движение силой дутья и огня и уносятся вместе с дымом. | ![]() |
Также Агрикола верно объясняет необходимость изменения конструкции печи в зависимости от типа руд[11]:
![]() | Так как природа руд, подлежащих плавке, бывает различной, плавильщикам приходится устраивать горн то выше, то ниже и устанавливать трубу, куда вводятся насадки мехов под меньшим или большим углом для того, чтобы дутье при надобности было более или менее сильным. Если руды нагреваются и плавятся легко, то для работы плавильщиков необходим низкий горн, а труба должна быть установлена под небольшим углом, чтобы дутье было легкое. Наоборот, если руды нагреваются и плавятся медленно, то требуется высокий горн, а труба должна быть установлена с крутым уклоном, чтобы обеспечить сильное дутье. Для руд этого рода нужна весьма горячая печь, в которой сначала расплавляются шлаки, штейны или легкоплавкие камни для того, чтобы руда не могла пригореть к поду горна и закрыть выпускное отверстие. | ![]() |
Передельный процесс[править | править код]
С XVI века в Европе получил распространение так называемый передельный процесс в металлургии — технология, при которой железо ещё при получении за счёт высокой температуры плавления и интенсивного науглероживания перегонялось в чугун, а уже затем, жидкий чугун, освобождаясь от лишнего углерода при отжиге в горнах, превращался в сталь.
Из передельной стали уже можно было изготавливать кривые мечи (например, сабли), чего не позволяла сделать сварная технология.
Применение угля, коксование, пудлингование, горячее дутьё[править | править код]
С начала XVII века европейской кузницей стала Швеция, производившая половину железа в Европе. В середине XVIII века её роль в этом отношении стала стремительно падать в связи с очередным изобретением — применением в металлургии каменного угля.
Прежде всего надо сказать, что до XVIII века включительно каменный уголь в металлургии практически не использовался — из-за высокого содержания вредных для качества продукта примесей, в первую очередь — серы. С XVII века в Англии каменный уголь, правда, начали применять в пудлинговочных печах для отжига чугуна, но это позволяло достичь лишь небольшой экономии древесного угля — большая часть топлива расходовалась на плавку, где исключить контакт угля с рудой было невозможно.
Потребление же топлива в металлургии уже тогда было огромно — домна (доменная печь) пожирала воз угля в час. Древесный уголь превратился в стратегический ресурс. Именно изобилие дерева в самой Швеции и принадлежащей ей Финляндии позволило шведам развернуть производство таких масштабов. Англичане, имевшие меньше лесов (да и те были зарезервированы для нужд флота), вынуждены были покупать железо в Швеции до тех пор, пока не научились использовать каменный уголь. Его ввёл в употребление в XVII веке Клемент Клерк и его мастера кузнечных дел и литья.
С 1709 году в местечке Коулбрукдейл Абрахам Дарби, основатель целой династии металлургов и кузнецов, использовал кокс для получения чугуна из руды в доменной печи. Из него поначалу делали лишь кухонную утварь, которая отличалась от работы конкурентов лишь тем, что её стенки были тоньше, а вес меньше. В 1750-х годах сын Дарби (Абрахам Дарби II) построил ещё несколько домен, и к этому времени его изделия были ещё и дешевле, чем изготовленные на древесном угле. В 1778 году внук Дарби, Абрахам Дарби III, из своего литья построил в Шропшире знаменитый Железный мост, первый мост в Европе, полностью состоящий из металлических конструкций.
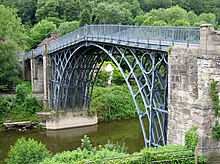
Для дальнейшего улучшения качества чугуна в 1784 году Генри Корт разработал процесс пудлингования. Среди многих металлургических профессий того времени, пожалуй, самой тяжелой была профессия пудлинговщика. Пудлингование было основным способом получения железа почти на протяжении всего XIX века. Это был очень тяжёлый и трудоёмкий процесс. Работа при нём шла так. На подину пламенной печи загружались чушки (слитки) чугуна; чушки расплавляли. По мере выгорания из металла углерода и других примесей температура плавления металла повышалась, и из жидкого расплава начинали «вымораживаться» кристаллы довольно чистого железа. На подине печи собирался комок слипшейся тестообразной массы. Рабочие-пудлинговщики приступали к операции накатывания крицы при помощи железного лома. Перемешивая ломом массу металла, они старались собрать вокруг лома комок, или крицу, железа. Такой комок весил до 50—80 кг и более. Крицу вытаскивали из печи и подавали сразу под молот — для проковки с целью удаления частиц шлака и уплотнения металла[7].
Рост производства и улучшение качества английского металла к концу XVIII века позволило Великобритании полностью отказаться от импорта шведского и российского железа. Развернулось сооружение каналов, позволявших перевозить уголь и металлы.
С 1830 по 1847 год производство металла в Англии возросло более чем в 3 раза. Применение горячего дутья при плавке руды, начавшееся в 1828 году, втрое сократило расход топлива и позволило использовать в производстве низшие сорта каменного угля, С 1826 по 1846 год экспорт железа и чугуна из Великобритании увеличился в 7,5 раза[12].
Конвертерное производство и мартеновские печи[править | править код]
В 1856 году Генри Бессемер получил патент на новую технологию производства стали (бессемеровский процесс). Он изобрёл конвертер — устройство, в котором сквозь жидкий чугун, получаемый в доменных печах, продувался воздух. В конвертере происходит выгорание углерода, растворённого в железе, что позволяет получать сталь в существенно больших количествах, чем это было ранее доступно.
Альтернативой применения конвертера на протяжении XX века являлась мартеновская печь, в которой также происходило дожигание углерода. К концу XX века мартеновские печи стали очевидно устаревшей технологией и были вытеснены кислородно-конвертерным производством стали.
В середине XX века был изобретён турбодетандер, позволяющий снизить затраты на производство кислорода. Кислород стал достаточно дешёвым, чтобы получить массовое применение в сталелитейной промышленности. Продувка расплавленного чугуна кислородом существенно разогревает металл, что упрощает производство (железо не «вымораживается», а остаётся жидким), позволяет также в конвертер сбрасывать металлолом для переплавки, а также в ряде случаев улучшает качество металла за счёт отсутствия растворённого в металле азота.
Электрометаллургия[править | править код]
Способность постоянного электрического тока восстанавливать металлы была обнаружена ещё в самом начале XIX века, однако отсутствие мощных источников электроэнергии ограничивало применение этих процессов лабораторными исследованиями. Появление в начале XX века мощных электростанций позволило создать промышленные технологии электрометаллургии. Изначально такие процессы применялись для производства цветных металлов, но к середине XX века пришли и в чёрную металлургию. Широкое применение нашли процессы электрической рудовосстанавливающей плавки, при которой железная руда, смешенная с незначительным количеством углерода, подвергается воздействию мощной электрической дуги, где происходит электрическое восстановление железа на катоде и выгорание примесей на аноде. Таким способом удаётся получить чугун высокого качества, сократить расход кислорода и снизить уровень выбросов углекислого газа. Передельные электрометаллургические процессы дают возможность плавить чугун в вакууме, в среде защитного газа, в присутствии химически активных легирующих элементов, что позволяет получать легированные стали высокого качества и специальные стали (жаропрочные, радиационно стойкие). Стали, получение которых возможно только электрометаллургическими процессами называют электросталями.
Восстановление водородом[править | править код]
Доменные печи и конвертерное производство является достаточно современным, но весьма грязным для экологии процессом. При том, что большая часть железа получается в кислородно-конвертерном производстве, велики и выбросы углекислого и угарного газов в атмосферу. Модной альтернативой становится прямое восстановление железа из руды водородом. При этом образующиеся частички железа расплавляются в электрических печах, после чего добавляется углерод и получается сталь.
Кузнецы-любители[править | править код]
Первыми производство железных изделий организовали кузнецы-любители — обычные крестьяне, промышлявшие таким ремеслом в свободное от обработки земли время. Кузнец сам находил «руду» (болотная руда вблизи ржавого болота или красный песок), сам выжигал уголь, сам строил сыродутную печь и выплавлял железо, сам ковал, сам обрабатывал.
Умение мастера на данном этапе закономерно было ограничено выковыванием изделий самой простой формы. Инструментарий же его состоял из мехов, каменных молота и наковальни и точильного камня. Железные орудия производились с помощью каменных инструментов.
Если удобные для разработки залежи руды имелись поблизости, то и целая деревня могла заниматься производством железа, но такое было возможным только при наличии устойчивой возможности выгодного сбыта продукции, чего практически не могло быть в условиях натурального хозяйства.
При такой организации производства железа, никогда не удавалось за его счёт полностью покрыть все потребности в самом простом оружии и самых необходимых орудиях труда. Из камня продолжали изготавливаться топоры, из дерева — гвозди и плуги. Металлические доспехи оставались недоступными даже для вождей. Концентрация железных изделий составляла всего порядка 200 граммов на душу населения[источник не указан 1111 дней].
На таком уровне доступности железа находились в начале нашей эры наиболее отсталые племена среди бриттов, германцев и славян. В XII‑XIII веке прибалты и финны сражаясь с крестоносцами пользовались ещё каменным и костяным оружием. Все эти народы умели уже делать железо, но ещё не могли получить его в необходимом количестве.[источник не указан 1111 дней]
Профессиональные кузнецы[править | править код]
Следующим этапом развития чёрной металлургии были профессиональные кузнецы, которые всё ещё сами выплавляли металл, но на добычу железоносного песка и выжигания угля чаще уже отправляли других мужиков — в порядке натурального обмена. На этом этапе кузнец, обычно, уже имел помощника-молотобойца и как-то оборудованную кузницу.
С появлением кузнецов концентрация железных изделий возрастала в 4‑5 раз. Теперь уже каждый крестьянский двор мог быть обеспечен персональным ножом и топором. Возрастало и качество изделий. Кузнецы профессионалы, как правило, владели техникой сварки и могли вытягивать проволоку. В принципе, такой умелец мог получить и дамаск, если знал как, но производство дамаскового оружия требовало такого количества железа, что не могло ещё быть сколько-то массовым.
В XVIII-XIX веках деревенские кузнецы умудрялись даже изготовлять стволы к нарезному оружию, но в этот период они уже пользовались оборудованием, которое сделали не сами. Некоторого масштаба перенос ремесленного производства из города в деревню становился возможным на таком этапе развития города, когда стоимость даже довольно сложного оборудования оказывалась незначительной.
Средневековые же деревенские кузнецы сами делали свои орудия труда. Как умели. Поэтому рядовой мастер обычно преуспевал в изготовлении предметов простой плоской формы, но положительно затруднялся, когда требовалось изготовить трёхмерное изделие, или состыковать несколько изделий между собой — что, например, требовалось для создания надёжного шлема. Изготовить же такое сложное изделие, как спусковой механизм для арбалета, деревенскому кузнецу было непосильно — для этого ведь потребовались бы даже измерительные устройства.
Не было у кустарных кузнецов и специализации — и мечи, и иголки, и подковы делал один и тот же мастер. Более того, во все времена сельские кузнецы были заняты в первую очередь именно изготовлением наиболее необходимых односельчанам простейших производственных и бытовых орудий, но не оружия.
Впрочем, последнее отнюдь не отменяет того обстоятельства, что в примитивных культурах даже самый заурядный кузнец считался несколько сродни колдуну, хотя, более адекватно его можно уподобить художнику. Выковывание даже обычного меча было настоящим искусством.
Теоретически всё выглядело просто: надо только наложить одна на другую три полоски металла, проковать их, и клинок готов. На практике, однако, возникали проблемы — с одной стороны надо было добиться прочной сварки и даже взаимопроникновения слоев, а с другой, нельзя было нарушать равномерность толщины слоя (а она-то и была — с лист бумаги) и, тем более, допустить, чтобы слой разорвался. А, ведь, обработка производилась тяжёлым молотом.
До разделения труда между городом и деревней годовое производство железа не превышало 100 граммов в год на человека, форма изделий была очень простой, а качество — низким, и, когда описывается вооружение какого-нибудь варяга, систематически упускается из вида, что речь идёт об оружии вождя, откопанном в его кургане. Варвары, которым курганы не полагались, вооружались существенно проще. На данном уровне развития производительных сил (характерном, например, для галлов, франков, норманнов, Руси X века) тяжёлое вооружение могло иметься только у аристократии — не более одного воина в броне на 1000 человек населения.
На новый уровень металлообрабатывающая промышленность вступила только тогда, когда стало возможным разделение труда и возникновение специальностей. Мастер железо покупал, причём уже нужного качества, покупал инструменты, необходимые по его профилю, и нанимал подмастерьев. Если уж он и делал ножи, то сдавал их на реализацию ящиками. Если делал мечи, то не по два в год, а по четыре в неделю. И, естественно, обладал большим опытом в их изготовлении.
Но для возникновения специализации непременно требовался город — хоть на несколько тысяч жителей — чтобы мастер мог всё купить и продать. Даже очень крупные призамковые посёлки (а их население тоже иногда достигало нескольких тысяч человек) не давали такой возможности — ведь в них не только ничего не производилось на продажу в другие поселения, но и отсутствовал даже внутренний товарообмен.
Чем более был развит обмен, тем больше могло быть мастеров и их специализаций, сформироваться разделение труда. Но для значительного развития обмена требовались деньги и сравнительная стабильность.
Ещё больший прогресс мог быть достигнут организацией мануфактуры, но вокруг неё требовалось выстроить уже 50-тысячный город, и наличие ещё нескольких таких же поблизости.
Тем не менее, даже после сосредоточения ремесленного производства в городах, колоритная фигура кузнеца оставалась непременным элементом пасторального ландшафта вплоть до начала, а кое-где и до середины XX века. Долгое время крестьяне просто не имели возможности покупать городские изделия. На ранних этапах развития обмена квалифицированные ремесленники обслуживали только господствующие классы — в первую очередь военные сословия.
После распространения штукофенов[править | править код]
Кустарное производство железа, однако, перестало практиковаться сразу после распространения штукофенов. Кузнецы начали покупать железо в слитках, а ещё чаще — железный лом, на предмет перековки мечей на орала.
Когда же развитие товарности хозяйства сделало ремесленные изделия доступными широким массам, кузнецы ещё долго занимались починкой сделанных в городах орудий.
Параллельно с решением организационных моментов улучшение методов обработки металлов требовало и совершенствования техники. Поскольку же основным методом была ковка, то усовершенствованию подлежали в первую очередь молоты.
Дело было в том, что, если ковка осуществлялась ручным молотом, то и размер изделия оказывался ограничен физическими возможностями кузнеца. Человек был способен отковать деталь весом не более нескольких килограммов. В большинстве случаев этого оказывалось достаточно, но при изготовлении, скажем, деталей осадных машин без механического молота, приводимого в движение водяным колесом, мулами или рабочими, было уже не обойтись.
Проблема выковывания массивных (до нескольких центнеров) деталей была решена ещё в античности, но в период средних веков она обрела новую остроту, так как крицы, получаемые из штукофенов, тоже нельзя было отковать кувалдой.
Конечно, можно было делить их на небольшие части, но, при этом, в каждой оказалось бы своё, причём неизвестное, содержание углерода, а потом, для изготовления мало-мальски крупного изделия полученные куски пришлось бы сковывать обратно.
Всё это было крайне невыгодно. Ковать крицу надо было целиком. Потому, штукофен по-хорошему требовалось комплектовать даже не одной, а тремя водяными машинами — одна качала мехи, другая — орудовала молотом, третья — откачивала воду из шахты. Без третьей тоже было никак — кустарными заготовками штукофен рудой было не обеспечить.
Впрочем, объёмы производства зависели не столько от технологий, сколько от организации труда. Если металлург не отвлекался на другие задачи, то и сыродутных печей он мог наделать куда больше. Так, в Риме производство достигло 1.5 килограмма на человека в год, и этого не хватало — железо в Рим возили даже из Китая. В Европе же и Азии даже с использованием штукофенов производство редко достигало килограмма. Но с появлением доменных печей в Европе этот показатель разом утроился, а
StudyPort.Ru — Производство железа
Получение железа из железной руды производится в две стадии. Оно начинается с подготовки руды-измельчения и нагревания. Руду измельчают на куски диаметром не более 10 см. Затем измельченную руду прокаливают для удаления воды и летучих примесей.
На второй стадии железную руду восстанавливают до железа с помощью оксида углерода в доменной печи. Восстановление проводится при температурах порядка 700 °С:
Для повышения выхода железа этот процесс проводится в условиях избытка диоксида углерода СО2.
Моноксид углерода СО образуется в доменной печи из кокса и воздуха. Воздух сначала нагревают приблизительно до 600 °С и нагнетают в печь через особую трубу- фурму. Кокс сгорает в горячем сжатом воздухе, образуя диоксид углерода. Эта реакция экзотермична и вызывает повышение температуры выше 1700°С:
Диоксид углерода поднимается вверх в печи и реагирует с новыми порциями кокса, образуя моноксид углерода. Эта реакция эндотермична:
Железо, образующееся при восстановлении руды, загрязнено примесями песка и глинозема (см. выше). Для их удаления в печь добавляют известняк. При температурах, существующих в печи, известняк подвергается термическому разложению с образованием оксида кальция и диоксида углерода:
Оксид кальция соединяется с примесями, образуя шлак. Шлак содержит силикат кальция и алюминат кальция:
Железо плавится при 1540 °С. Расплавленное железо вместе с расплавленным шлаком стекают в нижнюю часть печи. Расплавленный шлак плавает на поверхности расплавленного железа. Периодически из печи выпускают на соответствующем уровне каждый из этих слоев.
Доменная печь работает круглосуточно, в непрерывном режиме. Сырьем для доменного процесса служат железная руда, кокс и известняк. Их постоянно загружают в печь через верхнюю часть. Железо выпускают из печи четыре раза в сутки, через равные промежутки времени. Оно выливается из печи огненным потоком при температуре порядка 1500°С. Доменные печи бывают разной величины и производительности (1000-3000 т в сутки). В США существуют некоторые печи новой конструкции с четырьмя выпускными отверстиями и непрерывным выпуском расплавленного железа. Такие печи имеют производительность до 10000 т в сутки.
Железо, выплавленное в доменной печи, разливают в песочные изложницы. Такое железо называется чугун. Содержание железа в чугуне составляет около 95%. Чугун представляет собой твердое, но хрупкое вещество с температурой плавления около 1200°С.
Литое железо получают, сплавляя смесь чугуна, металлолома и стали с коксом. Расплавленное железо разливают в формы и охлаждают.
Сварочное железо представляет собой наиболее чистую форму технического железа. Его получают, нагревая неочищенное железо с гематитом и известняком в плавильной печи. Это повышает чистоту железа приблизительно до 99,5%. Его температура плавления повышается до 1400 °С. Сварочное железо имеет большую прочность, ковкость и тягучесть. Однако для многих применений его заменяют низкоуглеродистой сталью (см. ниже).
Химические реакции при выплавке чугуна из железной руды
В основе производства чугуна лежит процесс восстановления железа из его окислов окисью углерода.
Известно, что окись углерода можно получить, действуя кислородом воздуха на раскалённый кокс. При этом сначала образуется двуокись углерода, которая при высокой температуре восстанавливается углеродом кокса в окись углерода:
Восстановление железа из окиси железа происходит постепенно. Сначала окись железа восстанавливается до закиси-окиси железа:
Далее закись-окись железа восстанавливается в закись железа:
и, наконец, из закиси железа восстанавливается железо:
Скорость этих реакций растёт с повышением температуры, с увеличением в руде содержания железа и с уменьшением размеров кусков руды. Поэтому процесс ведут при высоких температурах, а руду предварительно обогащают, измельчают, и куски сортируют по крупности: в кусках одинаковой величины восстановление железа происходит за одно и то же время. Оптимальные размеры кусков руды и кокса от 4 до 8—10 см. Мелкую руду предварительно спекают (агломерируют) путём нагревания до высокой температуры. При этом из руды удаляется большая часть серы.
Железо восстанавливается окисью углерода практически полностью. Одновременно частично восстанавливаются кремний и марганец. Восстановленное железо образует сплав с углеродом кокса. кремнием, марганцем, и соединениями, серы и фосфора. Этот сплав—жидкий чугун. Температура плавления чугуна значительно ниже температуры плавления чистого железа.
Пустая порода и зола топлива также должны быть расплавлены. Для понижения температуры плавления в состав “плавильных” материалов вводят, кроме руды и кокса, флюсы (плавни) — большей частью известняк СаСО3 и доломит CaCO3×МgСО3. Продукты разложения флюсов при нагревании образуют с веществами, входящими в состав пустой породы и золы кокса, соединения с более низкими температурами плавления, преимущественно силикаты и алюмосиликаты кальция и магния, например, 2CaO×Al2O3×SiO2, 2CaO×Mg0×2Si02.
Химический состав сырья, поступающего на переработку, иногда колеблется в широких пределах. Чтобы вести процесс при постоянных и наилучших условиях, сырьё “усредняют” по химическому составу, т. е. смешивают руды различного химического состава в определённых весовых отношениях и получают смеси постоянного состава. Мелкие руды спекают вместе с флюсами, получая “офлюсованный агломерат”. Применение офлюсованного агломерата даёт возможность значительно ускорить процесс.
Производство стали
Стали подразделяются на два типа. Углеродистые стали содержат до 1,5% углерода. Легированные стали содержат не только небольшие количества углерода, но также специально вводимые примеси (добавки) других металлов. Ниже подробно рассматриваются различные типы сталей, их свойства и применения.
Кислородно-конвертерный процесс. В последние десятилетия производство стали революционизировалось в результате разработки кислородно-конвертерного процесса (известного также под названием процесса Линца-Донавица). Этот процесс начал применяться в 1953 г. на сталеплавильных заводах в двух австрийских металлургических центрах-Линце и Донавице.
В кислородно-конвертерном процессе используется кислородный конвертер с основной футеровкой (кладкой). Конвертер загружают в наклонном положении расплавленным чугуном из плавильной печи и металлоломом, затем возвращают в вертикальное положение. После этого в конвертер сверху вводят медную трубку с водяным охлаждением и через нее направляют на поверхность расплавленного железа струю кислорода с примесью порошкообразной извести (СаО). Эта “кислородная продувка”, которая длится 20 мин, приводит к интенсивному окислению примесей железа, причем содержимое конвертера сохраняет жидкое состояние благодаря выделению энергии при реакции окисления. Образующиеся оксиды соединяются с известью и превращаются в шлак. Затем медную трубку выдвигают и конвертер наклоняют, чтобы слить из него шлак. После повторной продувки расплавленную сталь выливают из конвертера (в наклонном положении) в ковш.
Кислородно-конвертерный процесс используется главным образом для получения углеродистых сталей. Он характеризуется большой производительностью. За 40-45 мин в одном конвертере может быть получено 300-350 т стали.
В настоящее время всю сталь в Великобритании и большую часть стали во всем мире получают с помощью этого процесса.
Электросталеплавильный процесс. Электрические печи используют главным образом для превращения стального и чугунного металлолома в высококачественные легированные стали, например в нержавеющую сталь. Электропечь представляет собой круглый глубокий резервуар, выложенный огнеупорным кирпичом. Через открытую крышку печь загружают металлоломом, затем крышку закрывают и через имеющиеся в ней отверстия опускают в печь электроды, пока они не придут в соприкосновение с металлоломом. После этого включают ток. Между электродами возникает дуга, в которой развивается температура выше 3000 °С. При такой температуре металл плавится и образуется новая сталь. Каждая загрузка печи позволяет получить 25-50 т стали.
Сталь получается из чугуна при удалении из него большей части углерода, кремния, марганца, фосфора и серы. Для этого чугун подвергают окислительной плавке. Продукты окисления выделяются в газообразном состоянии и в виде шлака.
Так как концентрация железа в чугуне значительно выше, чем других веществ, то сначала интенсивно окисляется железо. Часть железа переходит в закись железа:
Реакция идёт с выделением тепла.
Закись железа, перемешиваясь с расплавом, окисляет кремний марганец и углерод:
Si+2FeO=SiO2+2Fe
Mn+FeO=MnO+Fe
C+FeO=CO+Fe
Первые две реакции экзотермичны. Особенно много тепла выделяется при окислении кремния.
Фосфор окисляется в фосфорный ангидрид, который образует с окислами металлов соединения, растворимые в шлаке. Но содержание серы снижается незначительно, и поэтому важно чтобы в исходных материалах было мало серы.
После завершения окислительных реакций в жидком сплаве содержится ещё закись железа, от которой его необходимо освободить. Кроме того, необходимо довести до установленных норм содержание в стали углерода, кремния и марганца. Поэтому к концу плавки добавляют восстановители, например ферромарганец (сплав железа с марганцем) и другие так называемые “раскислители”. Марганец реагирует с закисью железа и “сраскисляет” сталь:
Мп+FеО=МnО+Fe
Передел чугуна в сталь осуществляется в настоящее время различными способами. Более старым, применённым впервые в середине XIX в. является способ Бессемера.
Способ Бессемера. По этому способу передел чугуна в сталь проводится путём продувания воздуха через расплавленный горячий чугун. Процесс протекает без затраты топлива за счёт тепла, выделяющегося при экзотермических реакциях окисления кремния, марганца и других элементов.
Процесс проводится в аппарате, который называется по фамилии изобретателя конвертером Бессемера. Он представляет собой грушевидный стальной сосуд, футерованный внутри огнеупорным материалом. В дне конвертера имеются отверстия, через которые подаётся в аппарат воздух. Аппарат работает периодически. Повернув аппарат в горизонтальное положение, заливают чугун и подают воздух. Затем поворачивают аппарат в вертикальное положение. В начале процесса окисляются железо, кремний и марганец, затем углерод. Образующаяся окись углерода сгорает над конвертером ослепительно ярким пламенем длиной до 8 л. Пламя постепенно сменяется бурым дымом. Начинается горение железа. Это указывает, что период интенсивного окисления углерода заканчивается. Тогда подачу воздуха прекращают, переводят конвертер в горизонтальное положение и вносят раскислители.
Процесс Бессемера обладает рядом достоинств. Он протекает очень быстро (в течение 15 минут), поэтому производительность аппарата велика. Для проведения процесса не требуется расходовать топливо или электрическую энергию. Но этим способом можно переделывать в сталь не все, а только отдельные сорта чугуна. К тому же значительное количество железа в бессемеровском процессе окисляется и теряется (велик “угар” железа).
Значительным усовершенствованием в производстве стали в конвертерах Бессемера является применение для продувкя вместо воздуха смеси его с чистым кислородом (“обогащённого воздуха”), что позволяет получать стали более высокого качества.
Мартеновский способ. Основным способом передела чугуна в сталь является в настоящее время мартеновский. Тепло, необходимое для проведения процесса, получается посредством сжигания газообразного или жидкого топлива. Процесс получения стали осуществляется в пламенной печи – мартеновской печи.
Примеси, содержащиеся в шихте, окисляются свободным, кислородом топочных газов и кислородом, входящим в состав железной руды, окалины и ржавчины.
Плавильное пространство мартеновской печи представляет собой ванну, перекрытую сводом из огнеупорного кирпича. В передней стенке печи находятся загрузочные окна, через которые завалочные машины загружают в печь шихту. В задней стенке находится отверстие для выпуска стали. С обеих сторон ванны расположены головки с каналами для подвода топлива и воздуха и отвода продуктов горения. Печь ёмкостью 350 т имеет длину 25 м и ширину 7 м.
Мартеновская печь работает периодически. После выпуска стали в горячую печь загружают в установленной последовательности лом, железную руду, чугун, а в качестве флюса — известняк или известь. Шихта плавится. При этом интенсивно окисляются: часть железа, кремний и марганец. Затем начинается период быстрого окисления углерода, называемый периодом “кипения”, — движение пузырьков окиси углерода через слой расплавленного металла создаёт впечатление, что он кипит.
В конце процесса добавляют раскислители. За изменением состава сплава тщательно следят, руководствуясь данными экспресс-анализа, позволяющего дать ответ о составе стали в течение нескольких минут. Готовую сталь выливают в ковши. Для повышения температуры пламени газообразное топливо и воздух предварительно подогревают в регенераторах. Принцип действия регенераторов тот же, что и воздухонагревателей доменного производства. Насадка регенератора нагревается отходящими из печи газами, и когда она достаточно нагреется, через регенератор начинают подавать в печь воздух. В это время нагревается другой регенератор. Для регулирования теплового режима печь снабжается автоматическими приспособлениями.
В мартеновской печи, в отличие от конвертера Бессемера, можно перерабатывать не только жидкий чугун, но и твёрдый, а также отходы металлообрабатывающей промышленности и стальной лом. В шихту вводят также и железную руду. Состав шихты можно изменять в широких пределах и выплавлять стали разнообразного состава, как углеродистые, так и легированные.
Российскими учёными и сталеварами разработаны методы скоростного сталеварения, повышающие производительность печей. Производительность печей выражается количеством стали, получаемым с одного квадратного метра площади пода печи в единицу времени.
Производство стали в электропечах. Применение электрической энергии в производстве стали даёт возможность достигать более высокой температуры и точнее её регулировать. Поэтому в электропечах выплавляют любые марки сталей, в том числе содержащие тугоплавкие металлы — вольфрам, молибден и др. Потери легирующих элементов в электропечах меньше, чем в других печах. При плавке с кислородом ускоряется плавление шихты и особенно окисление углерода в жидкой шихте, Применение кислорода позволяет ещё более повысить качество электростали, так как в ней остаётся меньше растворённых газов и неметаллических включений.
В промышленности применяют два типа электропечей: дуговые и индукционные. В дуговых печах тепло получается вследствие образования электрической дуги между электродами и шихтой. В индукционных печах тепло получается за счёт индуцируемого в металле электрического тока.
Сталеплавильные печи всех типов — бессемеровские конвертеры, мартеновские и электрические — представляют собой аппараты периодического действия. К недостаткам периодических процессов относятся, как известно, затрата времени на загрузку и разгрузку аппаратов, необходимость изменять условия по мере течения процесса, трудность регулирования и др. Поэтому перед металлургами стоит задача создания нового непрерывного процесса.
Применения в качестве конструкционных материалов сплавов железа.
Некоторые d-элементы широко используются для изготовления конструкционных материалов, главным образом в виде сплавов. Сплав-это смесь (или раствор) какого-либо металла с одним или несколькими другими элементами.
Сплавы, главной составной частью которых служит железо, называются сталями. Выше мы уже говорили, что все стали подразделяются на два типа: углеродистые и легированные.
Углеродистые стали | ||
Тип стали | Содержание углерода, % | Применения |
Низкоуглеродистая | 0,2 | Общее машиностроение: корпуса автомашин, проволока, трубы, болты и гайки |
Среднеуглеродистая | 0,3-0,6 | Балки и фермы, пружины |
Высокоуглеродистая | 0,6-1,5 | Сверла, ножи, молотки, резцы |
Углеродистые стали. По содержанию углерода эти стали в свою очередь подразделяются на низкоуглеродистую, среднеуглеродистую и высокоуглеродистую стали. Твердость углеродистых сталей возрастает с повышением содержания углерода. Например, низкоуглеродистая сталь является тягучей и ковкой. Ее используют в тех случаях, когда механическая нагрузка не имеет решающего значения. Различные применения углеродистых сталей указаны в таблице. На долю углеродистых сталей приходится до 90% всего объема производства стали.
Легированные стали. Такие стали содержат до 50% примеси одного или нескольких металлов, чаще всего алюминия, хрома, кобальта, молибдена, никеля, титана, вольфрама и ванадия.
Нержавеющие стали содержат в качестве примесей к железу хром и никель. Эти примеси повышают твердость стали и делают ее устойчивой к коррозии. Последнее свойство обусловлено образованием тонкого слоя оксида хрома (III) на поверхности стали.
Инструментальные стали подразделяются на вольфрамовые и марганцовистые. Добавление этих металлов повышает твердость, прочность и устойчивость при высоких температурах (жаропрочность) стали. Такие стали используются для бурения скважин, изготовления режущих кромок металлообрабатывающих инструментов и тех деталей машин, которые подвергаются большой механической нагрузке.
Кремнистые стали используются для изготовления различного электрооборудования: моторов, электрогенераторов и трансформаторов.
История производства и использования железа Википедия
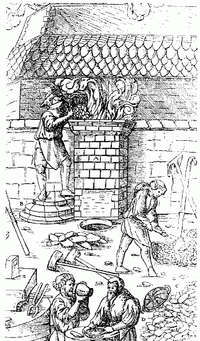
История производства и использования железа берёт своё начало в доисторической эпохе, скорее всего, с использования метеоритного железа. Выплавка в сыродутной печи применялась в XII веке до н. э. в Индии, Анатолии и на Кавказе. Также отмечается использование железа при выплавке и изготовлении орудий и инструментов в 1200 году до н. э. в Африке южнее Сахары[2][3]. Уже в первом тысячелетии до н. э. использовалось кованое железо (англ. Wrought iron). Об обработке железа упоминается в первой книге Библии (Быт. 4:22).
Свойства железных сплавов[ | ]
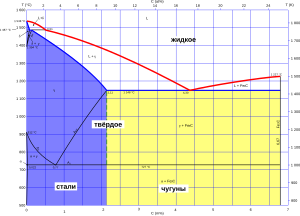
Материал, в обиходе называемый «железом», как правило, является сталью или чугуном и представляет собой сплав железа (Fe), как химического элемента, с углеродом (C). Кроме железа и углерода сплав содержит незначительные количества других химических элементов.
При концентрации углерода в сплаве менее 0,3 % получается мягкий пластичный тугоплавкий (температура плавления железа 1539 °C) сплав, за которым и закрепляется название его основного ингредиента — железа. Представление о том железе, с которым имели дело наши предки, сейчас можно получить, исследовав механические свойства гвоздя.
При концентрации углерода в сплаве от 0,3 до 2,14 % сплав называется «сталью
История производства и использования железа
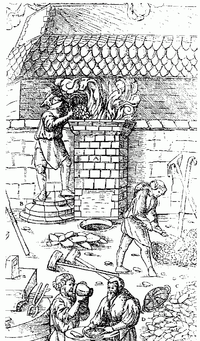
История производства и использования железа берет свое начало в доисторической эпохе, скорее всего, с использования метеоритного железа. Выплавка в сыродутной печи применялась в 12 веке до н. э. в Индии, Анатолии и на Кавказе. Также отмечается использование железа при выплавке и изготовлении орудий и инструментов в 1200 году до н. э. в Африке южнее Сахары[1]. Уже в первом тысячелетии до н. э. использовалось кованное железо.
Свойства железных сплавов
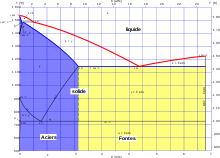
Более-менее общеизвестно, что материал, в обиходе называемый железом, даже в простейшем случае представляет собой сплав собственно железа, как химического элемента, с углеродом. При концентрации углерода менее 0,3 % получается мягкий пластичный тугоплавкий (Температура плавления железа выше 1500С) металл, за которым и закрепляется название его основного ингредиента — железа. Представление о том железе, с которым имели дело наши предки, сейчас можно получить, исследовав механические свойства гвоздя.
При концентрации углерода более 0,22 %, но менее 2,14 % сплав называется сталью. В первозданном виде сталь походит по своим свойствам на железо, но, в отличие от него, поддается закалке — при резком охлаждении сталь приобретает большую твёрдость — замечательное достоинство, однако, почти совершенно сводимое на нет благоприобретенной в процессе той же закалки хрупкостью.
Наконец, при концентрации углерода свыше 2,14 % мы получаем чугун. Хрупкий, легкоплавкий, хорошо пригодный для литья, но не поддающийся обработке ковкой, металл. Чугун насыщен графитовыми включениями, делающими металл неоднородным и механически непрочным. Температура плавления чугуна порядка 1150С.
Технологии производства и обработки железа и сплавов
С производством железа связано достаточно много технологий, которые сложно расположить в хронологическом порядке.
Метеоритное железо
Использование железа началось намного раньше, чем его производство. Иногда находили куски серовато-чёрного металла, который, перекованный в кинжал или наконечник копья, давал оружие более прочное и пластичное, чем бронза, и дольше держал острое лезвие. Затруднение состояло в том, что этот металл находили только случайно. Теперь мы можем сказать, что это было метеоритное железо. Поскольку железные метеориты представляют собой железоникелевый сплав, можно предположить[источник не указан 332 дня], что качество отдельных уникальных кинжалов, например, могло соперничать с современным ширпотребом. Однако, та же уникальность, приводила к тому, что такое оружие оказывалось не на поле боя, а в сокровищнице очередного правителя.
Сыродутная печь
Первым устройством для получения железа из руды была одноразовая сыродутная печь. При огромном количестве недостатков, долгое время это был единственный способ получить металл из руды.
Впервые железо научились обрабатывать народы Анатолии. Древнегреческая традиция считала открывателем железа народ халибов, для которых в литературе использовалось устойчивое выражение «отец железа», и само название стали в греческом языке (Χάλυβς) происходит именно от этнонима.
«Железная революция» началась на рубеже I тысячелетия до н. э. в Ассирии. С VIII века до н.э. сварное железо быстро стало распространяться в Европе, в III веке до н. э. вытеснило бронзу в Галлии, во II веке новой эры появилось в Германии, а в VI веке нашей эры уже широко употреблялось в Скандинавии и в племенах, проживающих на территории будущей Руси. В Японии железный век наступил только в VIII веке нашей эры.
- Известный популяризатор науки А.Азимов так описывает историю перехода человечества из бронзового века в железный[2]:
- Где-то около XV—XIV вв. до н. э. техника выплавки и науглероживания железа была разработана в кавказских предгорьях в Урарту. Эта страна находилась тогда под властью Хеттского царства, которое находилось на высшей точке своей мощи. Хеттские цари тщательно охраняли монополию на новую технику, ибо понимали ее важность. Вначале получали только маленькие партии железа, и в течение нескольких столетий оно стоило порой в сорок раз дороже серебра. Но еще до того, как выплавку можно было увеличить, а хеттам — этим воспользоваться, им пришел конец. Хеттское царство было разрушено во время беспорядков, последовавших за движением «народов моря», и хеттская монополия на железо была нарушена. Технология выплавки железа быстро распространялась в том числе, конечно, в Ассирию, которая граничила с «железным царством» Урарту.
- Торговля железом восстановила процветание Ассирии. Открылся путь для новых завоеваний.
- Вторгшиеся в Грецию дорийские племена обладали железным оружием, именно поэтому они так легко покорили вооруженных бронзой ахейцев. Было железо и у «народов моря», и, когда филистимляне захватывали ханаанское побережье, в сражениях они использовали железное оружие, Но они были не настолько глупы, чтобы раскрывать секрет выплавки железа. Пока им удавалось хранить эту техническую тайну, израильтянам приходилось обороняться более примитивным оружием. Благодаря железу филистимляне не только легко закрепились на побережье, но и обложили данью ближайшие к ним племена. Около двух веков (до прихода к власти Давида в 1013 г. до н. э.) им удавалось господствовать над более многочисленными израильскими племенами.
Первым шагом в зарождающейся чёрной металлургии было получение железа путём восстановления его из окиси. Руда перемешивалась с древесным углем и закладывалась в печь. При высокой температуре, создаваемой горением угля, углерод начинал соединяться не только с атмосферным кислородом, но и с тем, который был связан с атомами железа.
После выгорания угля в печи оставалась так называемая крица — комок пористого восстановленного железа с примесью большого количества шлаков. Крицу потом снова разогревали и подвергали обработке ковкой, выколачивая шлак из железа. Полученный брусок железа (в котором все же оставалось 2-4% шлака) назывался кричной болванкой. Долгое время в металлургии железа именно ковка была основным элементом технологического процесса, причём, с приданием изделию формы она было связана в последнюю очередь. Ковкой получался сам материал.
Сварное оружие
Сталь производилась уже из готового железа путём науглероживания последнего. При высокой температуре и недостатке кислорода углерод, не успевая окисляться, пропитывал железо. Чем больше было углерода, тем твёрже оказывалась сталь после закалки.
Как можно было заметить, ни один из перечисленных выше сплавов не обладает таким свойством, как упругость. Железный сплав может приобрести это качество, только если в нем возникает чёткая кристаллическая структура, что происходит, например, в процессе застывания из расплава. Проблема же древних металлургов заключалась в том, что расплавить железо они не могли. Для этого требуется разогреть его до 1540 градусов, в то время как технологии древности позволяли достичь температур в 1000−1300 градусов. Вплоть до середины XIX века было невозможно расплавить железо и сталь с содержанем углерода менее 0,4%, так как плавкость железных сплавов возрастает по мере увеличения концентрации углерода.
Таким образом, ни железо, ни сталь сами по себе для изготовления оружия не годились. Орудия и инструменты из чистого железа выходили слишком мягкими, а из чистой стали — слишком хрупкими. Потому, чтобы изготовить, например, меч, приходилось делать бутерброд из двух пластин железа, между которыми закладывалась стальная пластина. При заточке мягкое железо стачивалось и появлялась стальная режущая кромка.
Такое оружие, сваренное из нескольких слоев с разными механическими свойствами, называлось сварным. Общими недостатками этой технологии являлись излишняя массивность и недостаточная прочность изделий. Сварной меч не мог пружинить, вследствие чего неизбежно ломался или гнулся при ударе о непреодолимую преграду.
Отсутствием упругости недостатки сварного оружия не исчерпывались. В дополнение к упомянутым недостаткам, его, например, невозможно было толком заточить. Железу можно было придать какую угодно остроту (хотя и стачивалось оно со страшной скоростью), но и тупилась мягкая режущая кромка из железа почти мгновенно. Сталь же точиться не желала — режущая кромка крошилась. Здесь налицо полная аналогия с карандашами — мягкий грифель легко сделать очень острым, но он сразу затупится, а твёрдый до особой остроты не доведешь — десять раз сломается. Так что, бритвы приходилось делать из железа и затачивать заново ежедневно.
В целом же, сварное оружие не превосходило остротой столовый нож. Уже одно это обстоятельство требовало делать его достаточно массивным для придания удовлетворительных рубящих свойств.
Единственной мерой, позволяющей достичь сочетания остроты и твёрдости в рамках технологии сварки, была закалка изделия уже после его заточки. Применим же этот метод становился в случае, если стальная режущая кромка приваривалась просто к железному обуху, а не заключалась в «бутерброд» из железа. Либо после заточки могли быть закалены клинки, у которых железный сердечник оковывался снаружи сталью.
Недостатком такого метода было то, что заточка оказывалась возможна лишь однажды. Когда стальное лезвие иззубривалось и тупилось, весь клинок приходилось перековывать.
Тем не менее, именно освоение техники сварки — несмотря на все её недостатки — произвело настоящий переворот во всех сферах человеческой деятельности и привело к огромному возрастанию производительных сил. Сварные орудия были вполне функциональны и, при том, общедоступны. Только с их распространением каменные орудия оказались окончательно вытеснены, и наступил век металла.
Железные орудия решительно расширили практические возможности человека. Стало возможным, например, строить рубленные из брёвен дома — ведь железный топор валил дерево уже не в три, как медный, а в 10 раз быстрее, чем каменный. Широкое распространение получило и строительство из тёсаного камня. Он, естественно, употреблялся и в эпоху бронзы, но большой расход сравнительно мягкого и дорогого металла решительно ограничивал такие эксперименты. Значительно расширились также и возможности земледельцев.
Булатная сталь и дамаск
Увидеть железо жидким металлурги смогли только в XIX веке, однако, ещё на заре железной металлургии — в начале I тысячелетия до новой эры — индийские мастера сумели решить проблему получения высокоуглеродистой стали с композитной структурой. Такую сталь называли булатом, но из-за сложности изготовления и отсутствия необходимых материалов в большей части мира эта сталь так и осталась индийским секретом на долгое время.
Более технологичный путь получения упругой стали, при котором не требовались ни особо чистая руда, ни графит, ни специальные печи, был найден в Китае во II веке нашей эры. Сталь перековывали очень много раз, при каждой ковке складывая заготовку вдвое, в результате чего получался отличный оружейный материал, называемый дамаском, из которого, в частности, делались японские катаны.
Штукофен
Более высокую, по сравнению с сыродутной печью, ступень в развитии чёрной металлургии представляли собой постоянные высокие печи называемые в Европе штукофенами. Это действительно была высокая печь — с четырёхметровой трубой для усиления тяги. Мехи штукофена качались уже несколькими людьми, а иногда и водяным двигателем. Штукофен имел дверцы, через которые раз в сутки извлекалась крица.
Изобретены штукофены были в Индии в начале первого тысячелетия до новой эры. В начале нашей эры они попали в Китай, а в VII веке вместе с «арабскими» цифрами арабы заимствовали из Индии и эту технологию. В конце XIII века штукофены стали появляться в Германии и Чехии (а ещё до того были на юге Испании) и в течение следующего века распространились по всей Европе.
Производительность штукофена была несравненно выше, чем сыродутной печи — в день он давал до 250 кг железа, а температура в нем оказывалась достаточна для науглероживания части железа до состояния чугуна. Однако штукофенный чугун при остановке печи застывал на её дне, смешиваясь со шлаками, а очищать металл от шлаков умели тогда только ковкой, но как раз ей-то чугун и не поддавался. Его приходилось выбрасывать.
Иногда, впрочем, штукофенному чугуну пытались найти какое-то применение. Например, древние индусы отливали из грязного чугуна гробы, а турки в начале XIX века — пушечные ядра. Трудно судить, как гробы, но ядра из него получались — так себе.
- Ядра для пушек из железистых шлаков в Европе отливали еще в конце XVI в. Из литой брусчатки делались дороги. В Нижнем Тагиле до сих пор сохранились здания с фундаментами из литых шлаковых блоков.[3]
Блауофен
Металлурги давно заметили связь между температурой плавления и выходом продукта — чем выше она была, тем большую часть содержащегося в руде железа удавалось восстановить. Потому рано или поздно им приходила мысль форсировать штукофен предварительным подогревом воздуха и увеличением высоты трубы. В середине XV века в Европе появились печи нового типа — блауофены, которые сразу преподнесли сталеварам неприятный сюрприз.
Более высокая температура действительно значительно повысила выход железа из руды, но она же повысила и долю железа науглероживающегося до состояния чугуна. Теперь уже не 10 %, как в штукофене, а 30 % выхода составлял чугун — «свиное железо», ни к какому делу не годное. В итоге, выигрыш часто не окупал модернизации.
Блауофенный чугун, как и штукофенный, застывал на дне печи, смешиваясь со шлаками. Он выходил несколько лучшим, так как его самого было больше, следовательно, относительное содержание шлаков выходило меньше, но продолжал оставаться малопригодным для литья. Чугун получаемый из блауофенов оказывался уже достаточно прочен, но оставался ещё очень неоднородным — из него выходили только предметы простые и грубые — кувалды, наковальни. Уже прилично выходили пушечные ядра.
Кроме того, если в сыродутных печах могло быть получено только железо, которое потом науглероживалось, то в штукофенах и блауофенах внешние слои крицы оказывались состоящими из стали. В блауофенных крицах стали было даже больше, чем железа. С одной стороны, это казалось хорошо, но, вот, разделить-то сталь и железо оказывалось весьма затруднительно. Содержание углерода становилось трудно контролировать. Только долгой ковкой можно было добиться однородности его распределения.
В своё время, столкнувшись с этими затруднениями, индусы не стали двигаться дальше, а занялись тонким усовершенствованием технологии и пришли к получению булата. Но, индусов в ту пору интересовало не количество, а качество продукта. Европейцы, экспериментируя с чугуном, скоро открыли передельный процесс, поднимающий металлургию железа на качественно новый уровень.
Доменная печь
Следующим этапом в развитии металлургии стало появление доменных печей. За счёт увеличения размера, предварительного подогрева воздуха и механического дутья, в такой печи всё железо из руды превращалось в чугун, который расплавлялся и периодически выпускался наружу. Производство стало непрерывным — печь работала круглосуточно и не остывала. За день она выдавала до полутора тонн чугуна. Перегнать же чугун в железо в горнах было значительно проще, чем выколачивать его из крицы, хотя ковка все равно требовалась — но теперь уже выколачивали шлаки из железа, а не железо из шлаков.
Доменные печи впервые были применены на рубеже XV-XVI веков в Европе. На Ближнем Востоке и в Индии эта технология появилась только в XIX веке (в значительной степени, вероятно, потому, что водяной двигатель из-за характерного дефицита воды на Ближнем Востоке не употреблялся). Наличие в Европе доменных печей позволило ей обогнать в XVI веке Турцию если не по качеству металла, то по валу. Это оказало несомненное влияние на исход борьбы, особенно когда оказалось, что из чугуна можно лить пушки.
Передельный процесс и пудлинговочная печь
С XVI века в Европе получил распространение так называемый передельный процесс в металлургии — технология, при которой железо ещё при получении за счёт высокой температуры плавления и интенсивного науглероживания перегонялось в чугун, а уже затем, жидкий чугун, освобождаясь от лишнего углерода при отжиге в горнах, превращался в сталь.
Из передельной стали уже можно было изготавливать кривые мечи (например, сабли), чего не позволяла сделать сварная технология.
- Среди многих металлургических профессий того времени, пожалуй, самой тяжелой была профессия пудлинговщика. Пудлингование было основным способом получения железа почти на протяжении всего XIX в. Это был очень тяжелый и трудоемкий процесс. Работа при нем шла так: На подину пламенной печи загружались чушки чугуна; их расплавляли. По мере выгорания из металла углерода и других примесей температура плавления металла повышалась и из жидкого расплава начинали «вымораживаться» кристаллы довольно чистого железа. На подине печи собирался комок слипшейся тестообразной массы. Рабочие-пудлинговщики приступали к операции накатывания крицы при помощи железного лома. Перемешивая ломом массу металла, они старались собрать вокруг лома комок, или крицу, железа. Такой комок весил до 50 — 80 кг и более. Крицу вытаскивали из печи и подавали сразу под молот — для проковки с целью удаления частиц шлака и уплотнения металла.[3]
Применение угля и коксование
С начала XVII века европейской кузницей стала Швеция, производившая половину железа в Европе. В середине XVIII века её роль в этом отношении стала стремительно падать в связи с очередным изобретением — применением в металлургии каменного угля.
Прежде всего надо сказать, что до XVIII века включительно каменный уголь в металлургии практически не использовался — из-за высокого содержания вредных для качества продукта примесей, в первую очередь — серы. С XVII века в Англии каменный уголь, правда, начали применять в пудлинговочных печах для отжига чугуна, но это позволяло достичь лишь небольшой экономии древесного угля — большая часть топлива расходовалась на плавку, где исключить контакт угля с рудой было невозможно.
Устранять серу коксованием научились в Англии в 1735 году, после чего появилась возможность использовать для выплавки железа большие запасы каменного угля. Но за пределами Англии эта технология распространилась только в XIX веке.
Потребление же топлива в металлургии уже тогда было огромно — домна пожирала воз угля в час. Древесный уголь превратился в стратегический ресурс. Именно изобилие дерева в самой Швеции и принадлежащей ей Финляндии позволило шведам развернуть производство таких масштабов. Англичане, имевшие меньше лесов (да и те были зарезервированы для нужд флота), вынуждены были покупать железо в Швеции до тех пор, пока не научились использовать каменный уголь.
Конвертерное производство и мартеновские печи
В 1856 г. Г. Бессемер получил патент на новую технологию производства стали (Бессемеровский процесс). Он изобрёл конвертер — устройство, в котором сквозь жидкий чугун, получаемый в доменных печах, продувался воздух. В конвертере происходит выгорание углерода, растворённого в железе, что позволяет получать сталь в существенно больших количествах, чем это было ранее доступно.
Альтернативой применения конвертера на протяжении ХХ века являлась мартеновская печь, в которой также происходило дожигание углерода. К концу XX века мартеновские печи стали очевидно устаревшей технологией и были вытеснены кислородно-конвертерным производством стали.
В середине XX века был изобретён турбодетандер, позволяющий снизить затраты на производство кислорода. Кислород стал достаточно дешевым, чтобы получить массовое применение с сталелитейной промышленности. Продувка расплавленного чугуна кислородом существенно разогревает металл, что упрощает производство (железо не «вымораживается», а остаётся жидким), позволяет также в конвертер сбрасывать металлолом для переплавки, а также в ряде случаев улучшает качество металла за счет отсутствия растворённого в металле азота.
Восстановление водородом
Доменные печи и конвертерное производство является достаточно современным, но весьма грязным для экологии процессом. При том, что большая часть железа получается в кислородно-конвертерном производстве, велики и выбросы углекислого и угарного газов в атмосферу. Модной альтернативой становится прямое восстановление железа из руды водородом. При этом образующиеся частички железа расплавляются в электрических печах, после чего добавляется углерод и получается сталь.
Обработка металла
Кузнецы-любители
Самой первой формой организации производства железных изделий были кузнецы-любители. Обычные крестьяне, которые в свободное от обработки земли время промышляли таким ремеслом. Кузнец этого сорта сам находил «руду» (ржавое болото или красный песок), сам выжигал уголь, сам выплавлял железо, сам ковал, сам обрабатывал.
Умение мастера на данном этапе закономерно было ограничено выковыванием изделий самой простой формы. Инструментарий же его состоял из мехов, каменных молота и наковальни и точильного камня. Железные орудия производились с помощью каменных.
Если удобные для разработки залежи руды имелись поблизости, то и целая деревня могла заниматься производством железа, но такое было возможным только при наличии устойчивой возможности выгодного сбыта продукции, чего практически не могло быть в условиях натурального хозяйства.
Если же, допустим, на племя из 1000 человек имелся десяток производителей железа, каждый из которых за год соорудил бы пару-тройку сыродутных печей, то их трудами обеспечивалась концентрация железных изделий всего порядка 200 граммов на душу населения. И не в год, а вообще.
Цифра эта, конечно, очень приблизительная, но факт тот, что, производя железо таким способом, никогда не удавалось за его счёт полностью покрыть все потребности в самом простом оружии и самых необходимых орудиях труда. Из камня продолжали изготавливаться топоры, из дерева — гвозди и плуги. Металлические доспехи оставались недоступными даже для вождей.
Такого уровня возможностями обладали наиболее примитивные племена бриттов, германцев и славян в начале нашей эры. Каменным и костяным оружием отбивались прибалты и финны от крестоносцев — а это уже оказывались XII-XIII века. Все эти народы, конечно, умели уже делать и железо, но ещё не могли получить его в необходимом количестве.
Профессиональные кузнецы
Следующим этапом развития чёрной металлургии были профессиональные кузнецы, которые все ещё сами выплавляли металл, но на добычу железоносного песка и выжигания угля чаще уже отправляли других мужиков — в порядке натурального обмена. На этом этапе кузнец, обычно, уже имел помощника-молотобойца и как-то оборудованную кузницу.
С появлением кузнецов концентрация железных изделий возрастала в четыре-пять раз. Теперь уже каждый крестьянский двор мог быть обеспечен персональным ножом и топором. Возрастало и качество изделий. Кузнецы профессионалы, как правило, владели техникой сварки и могли вытягивать проволоку. В принципе, такой умелец мог получить и дамаск, если знал как, но производство дамаскового оружия требовало такого количества железа, что не могло ещё быть сколько-то массовым.
В XVIII-XIX веках деревенские кузнецы умудрялись даже изготовлять стволы к нарезному оружию, но в этот период они уже пользовались оборудованием, которое сделали не сами. Некоторого масштаба перенос ремесленного производства из города в деревню становился возможным на таком этапе развития города, когда стоимость даже довольно сложного оборудования оказывается незначительной.
Средневековые же деревенские кузнецы сами делали свои орудия труда. Как умели. Поэтому рядовой мастер обычно преуспевал в изготовлении предметов простой плоской формы, но положительно затруднялся, когда требовалось изготовить трёхмерное изделие, или состыковать несколько изделий между собой — что, например, требовалось для создания надёжного шлема. Изготовить же такое сложное изделие, как спусковой механизм для арбалета, деревенскому кузнецу не грозило — для этого, ведь, потребовались бы даже измерительные устройства.
Не было у кустарных кузнецов и специализации — и мечи, и иголки, и подковы делал один и тот же мастер. Более того, во все времена сельские кузнецы были заняты в первую очередь именно изготовлением наиболее необходимых односельчанам простейших производственных и бытовых орудий, но не оружия.
Впрочем, последнее отнюдь не отменяет того обстоятельства, что в примитивных культурах даже самый заурядный кузнец считался несколько сродни колдуну, хотя, более адекватно его можно уподобить художнику. Выковывание даже обычного меча было настоящим искусством.
Теоретически всё выглядело просто: надо только наложить одна на другую три полоски металла, проковать их, и клинок готов. На практике, однако, возникали проблемы — с одной стороны надо было добиться прочной сварки и даже взаимопроникновения слоев, а с другой, нельзя было нарушать равномерность толщины слоя (а она-то и была — с лист бумаги) и, тем более, допустить, чтобы слой разорвался. А, ведь, обработка производилась тяжёлым молотом.
До разделения труда между городом и деревней годовое производство железа не превышало 100 граммов в год на человека, форма изделий была очень простой, а качество низким, и, когда описывается вооружение какого-нибудь варяга, систематически упускается из вида, что речь идёт об оружии вождя, откопанном в его кургане. Варвары, которым курганы не полагались, вооружались существенно проще. На данном уровне развития производительных сил (характерном, например, для галлов, франков, норманнов, Руси X века) тяжёлое вооружение могло иметься ещё только у аристократии — не более одного воина в броне на 1000 человек населения.
На новый уровень металлообрабатывающая промышленность вступала только, когда становилось возможным разделение труда и возникновение специальностей. Мастер железо покупал, причём покупал уже нужного качества, мастер покупал себе инструменты — необходимые по его профилю, и нанимал подмастерий. Если уж он делал ножи, то уж сдавал их на реализацию ящиками. Если делал мечи, то не по два в год, а по четыре в неделю. И, естественно, обладал в соответствующее количество раз большим опытом в их изготовлении.
Но для возникновения специализации непременно требовался город — хоть на несколько тысяч жителей — чтобы мастер всё мог купить и продать. Даже очень крупные призамковые посёлки (а их население тоже иногда достигало нескольких тысяч человек) не давали такой возможности — ведь, в них не только ни что не производилось на продажу в другие поселения, но и отсутствовал даже внутренний товарообмен.
Очевидно, что чем более развит был обмен, тем больше могло быть мастеров и их специализаций, тем более могло проявиться разделение труда, но для значительно развития обмена непременно требовались деньги и сравнительная стабильность.
Ещё больший прогресс мог быть достигнут организацией мануфактуры, но вокруг неё требовалось выстроить уже 50 тысячный город, и ещё чтобы несколько таких же было поблизости.
Тем не менее, даже после сосредоточения ремесленного производства в городах, колоритная фигура кузнеца оставалась непременным элементом пасторального ландшафта вплоть до начала, а кое-где и до середины XX века. Долгое время крестьяне просто не имели возможности покупать городские изделия. На ранних этапах развития обмена квалифицированные ремесленники обслуживали только господствующие классы — в первую очередь военные сословия.
После распространения штукофенов
Кустарное производство железа, однако, перестало практиковаться сразу после распространения штукофенов. Кузнецы начали покупать железо в слитках, а ещё чаще — железный лом, на предмет перековки мечей на орала.
Когда же развитие товарности хозяйства сделало ремесленные изделия доступными широким массам, кузнецы ещё долго занимались починкой сделанных в городах орудий.
Параллельно с решением организационных моментов улучшение методов обработки металлов требовало и совершенствования техники. Поскольку же основным методом была ковка, то усовершенствованию подлежали в первую очередь молоты.
Дело было в том, что, если ковка осуществлялась ручным молотом, то и размер изделия оказывался ограничен физическими возможностями кузнеца. Человек был способен отковать деталь весом не более нескольких килограммов. В большинстве случаев этого оказывалось достаточно, но при изготовлении, скажем, деталей осадных машин без механического молота, приводимого в движение водяным колесом, мулами или рабочими, было уже не обойтись.
Проблема выковывания массивных (до нескольких центнеров) деталей была решена ещё в античности, но в период средних веков она обрела новую остроту, так как крицы, получаемые из штукофенов, тоже нельзя было отковать кувалдой.
Конечно, в принципе, можно было делить их на небольшие части, но, при этом, в каждой оказалось бы своё, причём неизвестное, содержание углерода, а потом, для изготовления мало-мальски крупного изделия полученные куски пришлось бы сковывать обратно.
Все это было крайне невыгодно. Ковать крицу надо было целиком. Потому, штукофен по-хорошему требовалось комплектовать даже не одной, а тремя водяными машинами — одна качала мехи, другая орудовала молотом, третья откачивала воду из шахты. Без третьей тоже было никак — кустарными заготовками штукофен рудой было не обеспечить.
Связь объёмов производства железа с технологиями, впрочем, была довольно слабой. Более это зависело от организации труда. Если металлург не отвлекался на другие задачи, то и сыродутных печей он мог наделать целую тучу. Так, в Риме производство достигло 1.5 килограмма на человека в год, и этого не хватало — железо в Рим возили даже из Китая. В Европе же и Азии даже с использованием штукофенов производство, обычно, не достигало килограмма. Но с появлением доменных печей в Европе этот показатель разом возрос втрое, а в Швеции с XVII века достиг 20 килограммов в год. К концу XVIII века этот рекорд был побит, и в Англии на душу населения стало производиться уже 30 кг железа в год.
В России после петровской индустриализации производство достигло 3 килограммов на душу населения в год и оставалось на этом уровне до конца XVIII века.
См. также
Примечания
- ↑ Duncan E. Miller and N.J. Van Der Merwe, ‘Early Metal Working in Sub Saharan Africa’ Journal of African History 35 (1994) 1-36; Minze Stuiver and N.J. Van Der Merwe, ‘Radiocarbon Chronology of the Iron Age in Sub-Saharan Africa’ Current Anthropology 1968.
- ↑ Серия исторических книг: Азимов А. Ближний Восток. История десяти тысячелетий — М.: ЗАО Центрполиграф, 2004. — 331 с.; Азимов А. Земля Ханаанская. Родина иудаизма и христианства — М.: ЗАО Центрполиграф, 2004. — 335 с.
- ↑ 1 2 Мезенин Н. А. Занимательно о железе. М. «Металлургия», 1972. 200 с. Использование железистых шлаков — «Черный нищий» ждет своего часа; пудлингование — Исчезнувшие профессии
Как получают и из чего делают железо (сталь)?
Железо и стали на его основе используются повсеместно в промышленности и обыденной жизни человека. Однако мало кто знает, из чего делают железо, вернее, как его добывают и преобразовывают в сплав стали.
Популярное заблуждение
Для начала определимся с понятиями, поскольку люди часто путаются и не совсем понимают, что такое железо вообще. Это химический элемент и простое вещество, которое в чистом виде не встречается и не используется. А вот сталь – это сплав на основе железа. Она богата на различные химические элементы, а также содержит углерод в своем составе, который необходим для придания прочности и твердости.
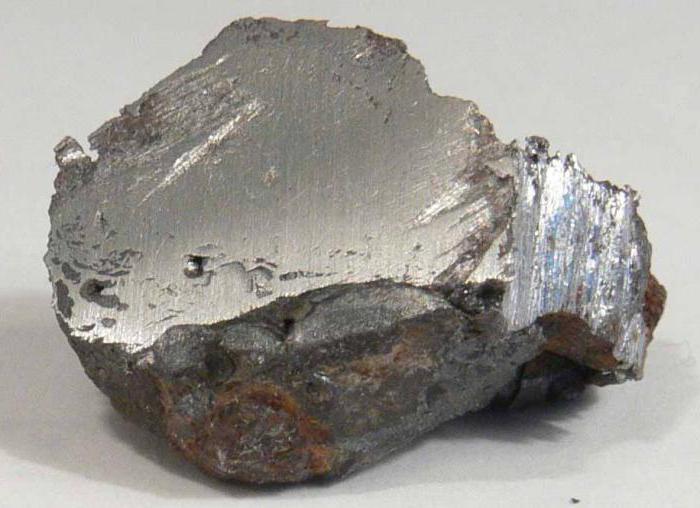
Следовательно, не совсем правильно рассуждать о том, из чего делают железо, так как оно представляет собой химический элемент, который есть в природе. Человек из него делает сталь, которая в дальнейшем может использоваться для изготовления чего-либо: подшипников, кузовов автомобилей, дверей и т. д. Невозможно перечислить все предметы, которые из нее производятся. Итак, ниже мы не будем разбирать, из чего делают железо. Вместо этого поговорим о преобразовании этого элемента в сталь.
Добыча
В России и мире существует множество карьеров, где добывают железную руду. Это огромные и тяжелые камни, которые достаточно сложно достать из карьера, так как они являются частью одной большой горной породы. Непосредственно на карьерах в горную породу закладывают взрывчатку и взрывают ее, после чего огромные куски камней разлетаются в разные стороны. Затем их собирают, грузят на большие самосвалы (типа БелАЗ) и везут на перерабатывающий завод. Из этой горной породы и будет добываться железо.
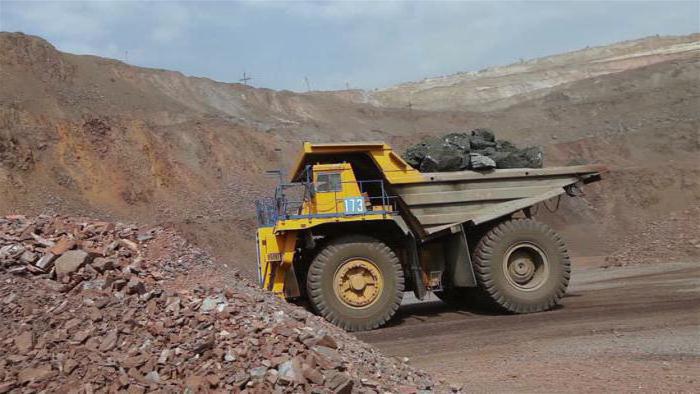
Иногда, если руда находится на поверхности, то ее вовсе необязательно подрывать. Ее достаточно расколоть на куски любым другим способом, погрузить на самосвал и увезти.
Производство
Итак, теперь мы понимаем, из чего делают железо. Горная порода является сырьем для его добычи. Ее отвозят на перерабатывающее предприятие, загружают в доменную печь и нагревают до температуры 1400-1500 градусов. Эта температура должна держаться в течение определенного времени. Содержащееся в составе горной породы железо плавится и приобретает жидкую форму. Затем его остается разлить в специальные формы. Образовавшиеся шлаки при этом отделяют, а само железо получается чистым. Затем агломерат подают в бункерные чаши, где он продувается потоком воздуха и охлаждается водой.
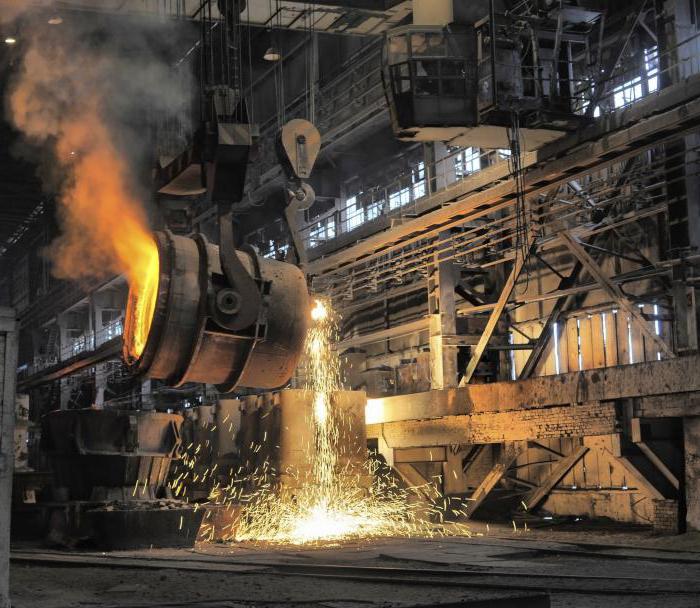
Есть и другой способ получения железа: горную породу дробят и подают на специальный магнитный сепаратор. Так как железо имеет способность намагничиваться, то минералы остаются на сепараторе, а вся пустая порода вымывается. Конечно, чтобы железо превратить в металл и придать ему твердую форму, его необходимо легировать с помощью другого компонента – углерода. Его доля в составе очень мала, однако именно благодаря нему металл становится высокопрочным.
Стоит отметить, что в зависимости от объема добавляемого в состав углерода сталь может получаться разной. В частности, она может быть более или менее мягкой. Есть, например, специальная машиностроительная сталь, при изготовлении которой к железу добавляют всего 0,75 % углерода и марганец.
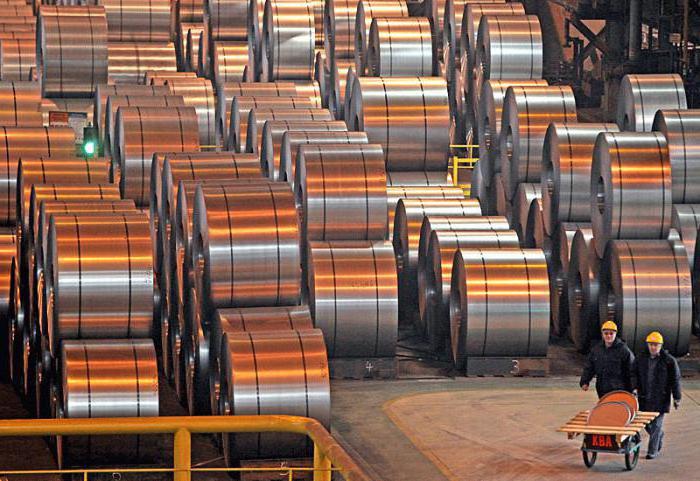
Теперь вы знаете, из чего делают железо и как его преобразовывают в сталь. Конечно, способы описаны весьма поверхностно, но суть они передают. Нужно запомнить, что из горной породы делают железо, из чего далее могут получать сталь.
Производители
На сегодняшний день в разных странах есть крупные месторождения железной руды, которые являются базой для производства мировых запасов стали. В частности, на Россию и Бразилию приходится 18 % мирового производства стали, на Австралию – 14 %, Украину – 11 %. Самыми крупными экспортерами является Индия, Бразилия, Австралия. Отметим, что цены на металл постоянно меняются. Так, в 2011 году стоимость одной тонны металла составляла 180 долларов США, а к 2016 году была зафиксирована цена в 35 долларов США за тонну.
Заключение
Теперь вы знаете, из чего состоит железо (имеется в виду металл) и как его производят. Применение этого материала распространено во всем мире, и его значение практически невозможно переоценить, так как используется он в промышленных и бытовых отраслях. К тому же экономика некоторых стран построена на базе изготовления металла и его последующего экспорта.
Мы рассмотрели, из чего состоит сплав. Железо в его составе смешивается с углеродом, и подобная смесь является основной для изготовления большинства известных металлов.
Железорудная промышленность — Википедия
Железорудная промышленность — отрасль горной промышленности, подотрасль чёрной металлургии, занимающаяся добычей железной руды и её предварительной переработкой: дроблением, сортировкой, обогащением, усреднением и окускованием мелочи путём агломерации или окомкования. Является сырьевой базой чёрной металлургии[1].
Известно, что люди добывали железную руду и получали из неё железо с древних времён. Однако быстрое развитие железорудной промышленности как индустриальной отрасли началось в 1-й половине XVIII века в связи с ростом выплавки чугуна и стали.
Развитие железорудной промышленности в мире[править | править код]
По данным Геологической службы США, мировая добыча железной руды составила в 2007 году 1,93 млрд тонн, увеличившись по сравнению с предыдущим годом на 7 %. Китай (1-е место), Бразилия (2-е место) и Австралия (3-е место в мире) обеспечивают две трети добычи, а вместе с Индией (4-е место) и Россией (5-е место в мире) — 80 %[2].
В 2009 году мировая добыча железной руды по данным U.S. Geological Survey составила 2,3 млрд тонн (рост на 3,6 % по сравнению с 2008 годом).
Список пятнадцати стран — крупнейших производителей железной руды в 2010 году представлен в нижеследующей таблице[3]:
За первое десятилетие XXI века производство железорудного сырья в мире удвоилось и в 2011 году оценивалось в 2,18 млрд тонн в год[4].
США[править | править код]
Основным железорудным районом США является месторождения (англ.)русск. района озера Верхнего. Запасы богатых руд Верхнего озера (основной рудной базы США) — 1,1 млрд т. Около 90 % руды добывается открытым способом. В связи с уменьшением запасов богатых руд много внимания уделяется использованию бедных руд (таконитов).
Австралия[править | править код]
Основным районом добычи железных руд в Австралии является район Хамерсли — Пилбара, где добывается около 90 % добычи в стране. Здесь действуют такие крупные рудники, как «Парабурду» (40 млн т в год), «Маунт-Уэйлбек» (32 млн т), «Маунт-Том-Прайс» (24,5 млн т), «Паннауоника» (16 млн т), «Маунт-Голдсуэрти» (7,8 млн т).
Бразилия[править | править код]
Бразилия обладает самыми крупными запасами железных руд в мире. В стране разрабатываются в основном богатые руды с содержанием железа более 60 %. Основной железорудный район Бразилии — штат Минас-Жерайс (так называемый железорудный четырёхугольник), где действуют крупные карьеры «Кауэ» (46 млн т), «Консейсан» (20 млн т), «Агуас-Кларас» (12 млн т), «Жерману» (10 млн т в год).
Крупнейшие компании-производители железной руды[править | править код]
Компания | Страновая принадлежность компании | На территории каких стран добывают руду предприятия компании | Суммарная производственная мощность по железной руде, млн. тонн в год. |
Vale | Бразилия | Бразилия, штат Минас Жейрас | 255 |
BHP Billiton | Австралия | Австралия, Бразилия[5] | 160 |
Rio Tinto | Великобритания | Австралия, Индия, Канада, Гвинея[6] | 153,4 |
ArcelorMittal | Великобритания | Канада, США, Мексика, Бразилия, Украина, Казахстан, Алжир, Либерия[7] | 78,9 (2011 год — 54,1 млн. тн[8]) |
Fortescue Metals Group | Австралия | Австралия | 165 |
Евразхолдинг | Россия, Великобритания, Люксембург | Россия, Украина | 50,4 |
Металлоинвест | Россия | Россия | 44,7 |
AnBen | Китай | Китай | 44,7 |
Метинвест Холдинг | Украина | Украина | 42,8 |
Anglo American | ЮАР | ЮАР | 41,1 |
LKAB | Швеция | Швеция | 38,5 |
Развитие железорудной промышленности в России и СССР[править | править код]
Железорудная промышленность в России существует более 300 лет. Однако в царской России уровень добычи железных руд был небольшой и составлял в 1913 году 9,2 млн тонн в год. Россия по уровню добычи железной руды занимала пятое место в мире после США, Германии, Англии и Франции. К 1917 году добыча железной руды сократилась и составляла всего 5,3 млн тонн в год. Основными центрами железорудной промышленности в дореволюционной были Урал и Кривой Рог[1].
Бурное развитие железорудной промышленности СССР начинается в годы первых пятилеток. В 1930 г. добыча железных руд в СССР превысила уровень 1913 г. Перед Великой Отечественной войной добывалось около 30 млн тонн руды в год. За военные годы уровень добычи сократился в два раза. Но к 1950 г. годовая добыча железной руды достигла 43,2 млн т. Динамика развития железорудной промышленности в послевоенные годы представлена в таблице. В 1958 г. СССР вышел на первое место в мире по добыче железной руды. В 1990 году добыча её превысила 236[9] млн тонн.
В СССР железорудная промышленность получила ускоренное развитие в связи с индустриализацией страны в годы первых пятилеток. СССР располагал значительными запасами богатых железных руд и практически неограниченными запасами бедных железных руд. По объёму балансовых запасов руды и по объёму производства товарной железной руды СССР занимал первое место в мире[10]. Огромные ресурсы железных руд позволяли при соответствующем развитии производственно-технической базы полностью удовлетворять растущие потребности чёрной металлургии СССР и ряда социалистических стран в товарной руде. Ускоренное развитие получил открытый способ добычи железной руды — наиболее экономичный и эффективный. Удельный вес добычи открытым способом увеличился с 54,3 % в 1959 году до 79,2 % в 1970 году. Технически перевооружены были шахты и рудники, разрабатывающие месторождения подземным способом.
Рост добычи руды в СССР в млн. тонн показан в таблице[11]
1913 | 1940 | 1950 | 1960 | 1970 | 1980 | 1985 | 1990 |
---|---|---|---|---|---|---|---|
9,2 | 29,9 | 39,7 | 105,9 | 195,5 | 244,7 | н.д. | 236 |
Резко выросла добыча бедных руд, которые проходили обогащение на обогатительных фабриках. Доля продукции обогатительных фабрик (концентратов) в товарной руде увеличилась с 53,6 % в 1965 до 62,3 % в 1970 году. Из концентратов расширилось производство агломерата с добавкой флюсов. Одновременно развивался новый способ окускования — окомкование концентратов на специальных установках (окомкователях) с последующим обжигом и получением окатышей, что позволило увеличить производительность доменных печей и снизить расход кокса.
В связи с ростом добычи бедных руд содержание железа в сырой руде в среднем снизилось с 40,8 % в 1965 до 37,3 % в 1970, а его содержание в товарной руде повысилось за эти годы с 56,7 % до 58,8 %, в концентрате — с 50,0 % до 61,8 %.
Существенно изменилось география размещения горнорудных предприятий отрасли. Важнейшей рудной базой Европейской части СССР являлся Криворожский железорудный бассейн. Предприятия этого бассейна снабжали железорудным сырьём заводы Приднепровья, Донбасса и других районов, а также ряд социалистических стран. Высокий удельный вес добычи рудного сырья в бассейне обеспечивали пять горно-обогатительных комбинатов (ГОКов) по открытой добыче и переработке железистых кварцитов: — Южный ГОК (пущен в 1955 году), Новокриворожский ГОК (пущен в 1959 году), Центральный ГОК (пущен в 1961 году), Северный ГОК (пущен в 1964 году) и Ингулецкий ГОК (пущен в 1965 году).
Второй по значимости и масштабам производства рудной базой страны и главной рудной базой заводов Центральной части СССР стали предприятия Курской магнитной аномалии (КМА). Запасы КМА во много раз превосходят запасы крупнейших месторождений мира. Здесь были построены такие крупные предприятия как Михайловский ГОК, Лебединский ГОК и другие.
На востоке страны усиленными темпами осваивались месторождения Урала, Сибири и Казахстана. На Урале в Свердловской области были построены Качканарский ГОК и Северо-Песчанский рудник.
В Казахстане в Кустанайском железорудном бассейне были построены Соколовско-Сарбайский ГОК, Лисаковский ГОК и Качарский ГОК
Руды мощного Ангаро-Питского железорудного бассейна в Красноярском крае и Ангаро-Илимского железорудного района в Иркутской области стали базой для развития металлургии Сибири. Был сооружён Коршуновский ГОК, увеличена добыча руд на рудниках Кемеровской области, введены в строй рудники в Красноярском крае, снабжающие рудой Кузнецкий комбинат (Кемеровская область).
Железорудная промышленность в постсоветской России[править | править код]
Основной объем (92,6 % в 2006 году) сырой руды на предприятиях РФ добывается открытым способом на 29 карьерах. На самых крупных карьерах (Лебединский, Михайловский, Стойленский, Северный Качканарского ГОКа, Костомукшский) производительностью более 20 млн. т в 2006 году было добыто 70 % железной руды, а на трех карьерах (Ковдорский, Главный, Западный Качканарского ГОКа) производительностью 10—20 млн. т добыча руды составила 16 % (40,63 млн. т).
Удельный вес 8 крупнейших ГОКов (Лебединский, Михайловский, Качканарский, Стойленский, Костомукшский, Ковдорский, Оленегорский, Коршуновский) в добыче сырой руды открытым способом в России в 2006 г. достиг 243,4 млн. т и составил 96 % всей открытой добычи. Средневзвешенная по добыче глубина их 273,7 м; самые глубокие из них Лебединский (355 м), Ковдорский (339 м), Стойленский (328,5 м).
Подземным способом железная руда в России добывается на 11 шахтах и подземном руднике Оленегорского ГОКа, суммарная добыча на которых в 2006 г. составила 20,43 млн. т. Максимальная добыча была достигнута на шахте им. Губкина комбината «КМАруда» (3992 тыс. т) и шахте Шерегешского рудоуправления (3480 тыс. т), минимальная — на шахте «Сидеритовая» (523 тыс. т). Максимальную глубину имеет шахта Таштагольского рудника (800 м), минимальную — шахта «Сидеритовая» (280 м).
В 2006 г. российской железорудной промышленностью произведено 103,7 млн. т железорудного сырья, т. е. на 6,9 млн. т больше, чем в 2005 г.[12].
Объём добычи сырой и производства товарной железной руды на предприятиях России, млн тонн[13] | ||||
---|---|---|---|---|
Предприятие | Сырая руда | Товарная руда | ||
2005 г. | 2006 г. | 2005 г. | 2006 г. | |
Качканарский ГОК | 45,999 | 51,2 | 8,6 | 9,4 |
Лебединский ГОК | 48,9 | 49,9 | 20,6 | 21,0 |
Михайловский ГОК | 42,5 | 49,6 | 16,9 | 20,1 |
Костомукшский ГОК | 25,4 | 26,3 | 9,1 | 9,96 |
Стойленский ГОК | 24,4 | 26,0 | 11,9 | 12,7 |
Ковдорский ГОК | 16,2 | 15,5 | 5,8 | 5,6 |
Оленегорский ГОК | 12,0 | 13,3 | 4,0 | 4,5 |
Коршуновский ГОК | 11,3 | 11,6 | 4,5 | 4,98 |
Высокогорский ГОК | 4,3 | 4,4 | 1,4 | 1,5 |
КМАруда | 4,0 | 3,99 | 1,85 | 1,85 |
Шерегешское рудоуправление | 3,0 | 3,5 | 1,6 | 1,8 |
Тейское рудоуправление | 2,6 | 2,8 | 1,5 | 1,6 |
Ирбинское рудоуправление | 2,5 | 2,4 | 1,4 | 1,3 |
Богословское рудоуправление | 2,4 | 2,3 | 1,3 | 1,3 |
ГОП ММК | 2,4 | 2,2 | 1,5 | 1,5 |
Абаканское рудоуправление | 2,0 | 2,0 | 0,8 | 0,9 |
Таштагольское рудоуправление | 1,9 | 1,8 | 1,5 | 1,3 |
Бакальское рудоуправление | 1,4 | 1,8 | 1,1 | 1,2 |
Казское рудоуправление | 1,5 | 1,5 | 0,8 | 0,8 |
Первоуральское рудоуправление | 1,3 | 1,0 | 0,06 | 0,1 |
Краснокаменское рудоуправление | 1,1 | 0,7 | 0,5 | 0,2 |
ИТОГО | 257,3 | 273,9 | 96,8 | 103,7 |
- Институт горного дела УрО РАН. Технико-экономические показатели горных предприятий за 1990—2006 гг.. — Екатеринбург: Типография «Уральский центр академического обслуживания», 2007. — 390 с. — ISBN 5-7691-1889-X.
Производство железа, черная металлургия
Железо
Производство чугуна
Чугун получают в вертикальных печах – домнах.
Чугун выплавляют из шихты, содержащей куски обогащенной руды, в присутствии восстановителя (кокса) и флюсов (обычно доломита CaCO3 MgCO3). Снизу в доменную печь вдувают воздух, обогащенный кислородом. Содержащийся в коксе углерод сгорает, а полученный диоксид углерода восстанавливается избытком углерода до монооксида. Образующийся в печи монооксид углерода последовательно восстанавливает содержащийся в руде оксид железа(III) до железа:
3Fe2O3 + CO = 2Fe3O4 + CO2
2Fe3O4 + 2CO = 6FeO + 2CO2
FeO + CO = Fe + CO2
Если бы доменную печь можно было загружать чистыми оксидом железа и углеродом и продувать чистым кислородом, то термохимия доменной печи сводилась бы к написанным выше простым уравнениям. На самом же деле во вдуваемом воздухе больше азота, чем кислорода, а руда может содержать свыше 50% безрудных минералов (пустой породы), в основном силикатов. Азот проходит через печь, не вступая в реакцию, но с силикатами дело сложнее. Чтобы можно было отделить силикаты от железа и вывести из печи, они должны быть жидкими. Силикаты, содержащиеся в железной руде, образуют расплавленный шлак при взаимодействии с известью CaO. Для этого в печь вместе с рудой загружают в нужной пропорции известняк CaCO3. Известняк, или «флюс», разлагается в верхней части печи соответственно реакции
CaCO3 = Ca + CO2
образуя известь, необходимую для перевода силикатных примесей железной руды в жидкий шлак. Доменная печь дает почти столько же шлака, сколько и чугуна. Затвердевая, шлак превращается в темный стекловидный материал, который в прошлом накапливался в больших шлаковых отвалах возле передельных металлургических заводов. В наши дни шлак идет на изготовление заполнителя для бетона, железнодорожного балласта, шлаковаты и противоюзового покрытия автомобильных дорог.
Из сказанного выше вытекают основные требования к конструкции доменной печи. Она должна обеспечивать непрерывную загрузку топливом, рудой и флюсом сверху, непрерывную подачу воздуха и периодический отвод жидких продуктов снизу. Печь должна быть достаточно высокой, чтобы успевали протекать необходимые химические реакции. Воздух вдувается в печь через фурмы, расположенные в ее нижней части, и поднимается сквозь шихту вверх. Восстановленное губчатое железо и шлак плавятся на уровне «заплечиков», в самой широкой части печи, а жидкость накапливается в горне, ниже фурм. В горне периодически пробивают заделанные глиной летку для выпуска металла и (несколько выше) шлаковую летку.
Восстановление оксида железа до губчатого железа и разложение известнякового флюса происходят в шахте – основной части доменной печи – в процессе медленного оседания шихты. Шихта начинает разогреваться в колошнике – верхнем конце шахты. Диоксид углерода и азот непрерывно отводятся по широкому газоходу из колошника. Поскольку при нормальной работе доменной печи давление газов в колошнике выше атмосферного, верхний конец печи нельзя просто открывать для загрузки, иначе упадет давление газов и из печи будут выдуваться наружу тонкоизмельченные компоненты шихты. Для предотвращения этого предусмотрен двухконусный шлюзовой засыпной аппарат. Нижний конус поднимают так, чтобы он газоплотно закрывал загрузочное отверстие, а затем опускают верхний для загрузки. После этого снова поднимают верхний конус, герметизируя вход в печь, и, опустив нижний, пропускают порцию шихты (колошу) в колошник.
Современная доменная печь представляет собой крупное сооружение. Высота печи, производящей 1000 т чугуна в сутки, составляет около 30 м, а диаметр на уровне заплечиков – ок. 8 м. Печь устанавливается на бетонном фундаменте, на котором в стальном кожухе выводится кладка из огнеупорного кирпича. Нижняя часть этой конструкции охлаждается водой.
Сколь ни внушительны размеры доменной печи, сама она – лишь малая часть чугуноплавильного завода. Для ее нормальной работы нужны еще отделение шихтовых материалов, грузоподъемные устройства для загрузки печи, насосы для подачи воздуха (дутья) и воздухонагреватели (кауперы), шлаковозы и литейный цех или приемная система для расплавленного металла. Для загрузки доменных печей иногда применяются ленточные конвейеры, но чаще руда, топливо и флюс подаются скиповыми подъемниками – небольшими сосудами (скипами), движущимися на колесах по наклонным рельсам от нижних засыпных бункеров до верхней загрузочной площадки, где они автоматически опрокидываются, разгружаясь в приемную воронку засыпного аппарата.
Эффективность доменной печи существенно повышается при использовании горячего дутья. Воздух, подводимый к фурмам, предварительно нагревается до температуры, которая может достигать 1000° C. Нагревание осуществляется в кауперах, каждый из которых ненамного уступает в размерах самой доменной печи. Каупер представляет собой вертикальный цилиндрический стальной кожух с внутренней «шахматной» насадкой из огнеупорного кирпича.
Газ, отводимый с верхнего конца доменной печи, содержит моноксид углерода и другие газы, способные гореть. Этот газ по широким наклонным газоходам подводится к нижней части каупера, где, пройдя через пылевой фильтр, сжигается в камере горения. Продукты горения поднимаются вверх, нагревая кирпичную насадку. Когда насадка достаточно нагрета, перекрывают подачу топлива и газа в камеру горения и включают воздуходувки, которые гонят воздух через каупер в фурмы доменной печи. Для каждой доменной печи обычно предусматривают четыре каупера: два нагреваются, а два других подают горячее дутье. Потоки газа и воздуха периодически переключаются так, что непрерывно поддерживается заданная температура дутья.
Существует ряд способов дополнительного повышения эффективности доменной печи. Один из них – работа при давлении внутренних газов, вдвое превышающем атмосферное. Это позволяет повысить производительность примерно на 15% и снизить потребление кокса примерно на 10%. Экономические преимущества повышения производительности в какой-то мере снижаются затратами на более мощн