Полимерные композиционные материалы: структура, свойства, технология
Сами по себе композиты давно стали основой многих отраслей промышленности. Материал зовется композиционным ввиду структуры. Матрицу-пластификатор армируют различными органическими и неорганическими материалами и получается полимерный композитный материал. ПКМ — это фактически Лего из мира органической химии. Если комбинировать матрицу и наполнитель, рассчитывать разные пропорции, то можно легко получить материалы гораздо лучше «традиционных», при этом они в основном намного легче обыкновенного армирования. Свойства полимерных композитов становятся все доступнее и уже применяются не только в области космических технологий, но и как более доступная основа для бытовых приборов.
Компонентами композитов может быть практически что угодно. Тут используется пластик, практически все металлы, полимерные волокна и т.д. Существуют еще более сложные композиты — полиматричные, если основой используют несколько различных полимеров для матрицы, а также гибридные варианты, при которых комбинируются армирующие волокна. Матрица-пластификатор отвечает за монолитность материала, тогда как армирующий наполнитель дает ему заданные параметры жесткости, деформации, прочности на излом, кручение и т. д.
Компания «Юнитрейд» занимается поставкой различных полимеров на основе нефти и не только. Вариации того, какие ПКМ сейчас может предложить миру химпром, рассмотрим ниже, с кратким экскурсом в особенности материалов.
Полимерные композиты
Полимерными композитами называется материал с соответствующей матрицей. Они наиболее популярны среди отраслей народного хозяйства. Современная аэрокосмическая отрасль уже немыслима без ПКМ. Например, в последнем поколении французского штурмового истребителя Дассо Рафаль ПКМ составляют почти четверть планера. Полимерные композитные материалы не корродируют, меньше страдают от статического электричества, не требуют дорогостоящих покрасочных эмалей, весьма легкие. Обратная сторона — материал недешевый, но кумулятивный экономический эффект очевиден сразу.
Стеклопластики
Всем известный «плексиглас», которым в свое время начали покрывать кокпиты современных скоростных истребителей, — это американский бренд оргстекла, начавший использование композитов с применением силикона. Химически натуральный оксид кремния довольно нейтрален, его очень тяжело растворить почти всеми кислотами. Физически же неорганическое стекло — фактически жидкость сверхвысокой вязкости, воспринимаемая нами твердым телом. То есть материал фактически несжимаемый, великолепный диэлектрик из-за свойств четырех- и восьмивалентного кремния, а также с неплохим коэффициентом преломления.
Матрицей в стеклопластиках бывают:
- термореактивные синтетические смолы из эпоксидки, фенолов, полиэфира;
- полистирол, полиамиды, полиэтилен — полиматериалы со сравнительно низкой температурой плавления.
Матрица под стеклопластики стала в последние годы более связующей, нежели определяющей параметры конечного вещества. Выяснилось, что у самих по себе стекловолокон довольно выдающиеся параметры — стеклянное волокно лишь нужно обеспечить прочными адгезионными связями в одно целое. В новых стеклопластиках армирующего волокна фактически четыре пятых от общей массы. Выпускают также слоистый стеклотекстолит. Стеклопластики недорогие, а потому их охотно применяют строители и даже производители обыкновенных бюджетных стеклопакетов.
Углепластики
Углепластиковые материалы стали фурором научно-популярной литературы последних лет. Собственно, многие новости о чем-то нано инновационном — это почти гарантированно связано с применением углеродных волокон. Четырехвалентный углерод — основа самой жизни и первый элемент органической химии. Поэтому получить его волокна можно из:
- натуральной и синтезированной целлюлозы;
- производных акрилонитрила;
- тяжелых нефтяных отложений — битумов, пеков, кера, озокерита и т. д.
В случае с нефтяными отложениями роль играет химическая ценность: из озокерита волокно добыть окислением, конечно, можно, химия разрешает, однако это окажется дороже, чем переработка более «бросовых» веществ. Волокно для армирования нужно обработать. Оно проходит три стадии:
- окисление;
- карбонизация;
- графитизация.
Эти стадии подобны естественному процессу образования каменного угля, поздние этапы происходят при температурах в тысячи градусов и повышенном давлении. Итоговый графит — практически стопроцентный углерод со следовыми примесями.
Преимущество углепластика — легкость, упругость, прочность. Он почти не расширяется, нагреваясь. Углеродное волокно с углеродной же матрицей в итоге создают углепластик — исключительно термопрочные вещества, сопротивляющиеся окислению, а потому широчайше применяемые в ракетостроении вместо графита, которого они прочней и плотней примерно в полтора раза.
Боропластик
Композиционный материал на полимерной основе, прошитый борными волокнами на полимерной матрице из термореактивного вещества. Волокна могут существовать как одинарные нити, и могут быть свиты жгутами, в результате чего получается сверхпрочный и твердейший материал. Армированный бором пластик наиболее устойчив химически и на сжатие, однако на излом он оказывается чрезвычайно хрупким. Борное волокно невероятно тяжело обрабатывать, потому итоговый ПКМ с бором оказывается дорогим — сотни долларов за килограмм только волокон, без учета матрицы. Для этого ПКМ нужны очень дорогие катализаторы, а рабочая температура сильно ограничена.
Органопластики
Изделия из полимерных композиционных материалов, где в основу кладут обыкновенные и привычные органические волокна — тканевые, нитевые, бумажные. Основа — эпоксидка и фенольные смолы. Армирующего волокна в них редко бывает больше трети и по массе и по объему. Производить органопластик сравнительно легко: матричные материалы недорогие, а волокна вообще можно набрать из отходов производства. Тем не менее, в итоге получается весьма прочный материал. Кевлар, гордость компании Дюпон — это органопластик на сложных амидных полимерах. Впрочем, амидное волокно в органопластическом производстве все же несколько дороже, чем обыкновенное армирование эпоксидки нитями.
Полимеры порошкового наполнителя
Также известнейшее изобретение. В начале прошлого века Лео Бакеланд патентует бакелит, который был сделан на матрице ФФМ-смолы или бакелита. Фенолформальдегидные смолы очень хрупки, однако если их перемешать с древесной мукой — они сильно упрощаются. Бакелит — идеальный материал под формовку, из него делали все: рычаги селекторов КПП, телефоны, отливные лотки для других материалов. Фактически, это самый распространенный в мире композитный материал ХХ века, деливший популярность с эбонитом, но вытеснивший его из многих областей. Сегодня область порошкообразных наполнителей «впитала» практически всю неорганику. Каолины, мел, мергели, известняки в связке с ПВХ и иными низкополимерными полимерами заполонили рынок ПКМ и есть почти во всех бытовых приборах. Они дешевы, а их сырьевые источники практически неисчерпаемы. Одновременно, простой рекомбинацией порошка и матрицы можно получить практически любую прочность, упругость, требуемую термостойкость.
Текстолиты
Композитный материал — Википедия
Обычная клеёная фанера является широко распространённым композитным материаломКомпозитный материа́л (КМ), компози́т — многокомпонентные материалы, состоящие, как правило, из пластичной основы (матрицы), армированной наполнителями, обладающими высокой прочностью, жёсткостью и т. д. Сочетание разнородных веществ приводит к созданию нового материала, свойства которого количественно и качественно отличаются от свойств каждого из его составляющих. Варьируя состав матрицы и наполнителя, их соотношение, ориентацию наполнителя, получают широкий спектр материалов с требуемым набором свойств. Многие композиты превосходят традиционные материалы и сплавы по своим механическим свойствам и в то же время они легче. Использование композитов обычно позволяет уменьшить массу конструкции при сохранении или улучшении её механических характеристик.
Структура композитных материалов
По структуре композиты делятся на несколько основных классов: волокнистые, слоистые, дисперсноупрочненные, упрочнённые частицами и нанокомпозиты. Волокнистые композиты армированы волокнами или нитевидными кристаллами — кирпичи с соломой и папье-маше можно отнести как раз к этому классу композитов. Уже небольшое содержание наполнителя в композитах такого типа приводит к появлению качественно новых механических свойств материала. Широко варьировать свойства материала позволяет также изменение ориентации размера и концентрации волокон. Кроме того, армирование волокнами придаёт материалу анизотропию свойств (различие свойств в разных направлениях), а за счёт добавки волокон проводников можно придать материалу электропроводность вдоль заданной оси.
В слоистых композиционных материалах матрица и наполнитель расположены слоями, как, например, в особо прочном стекле, армированном несколькими слоями полимерных плёнок.
Микроструктура остальных классов композиционных материалов характеризуется тем, что матрицу наполняют частицами армирующего вещества, а различаются они размерами частиц. В композитах, упрочнённых частицами, их размер больше 1 мкм, а содержание составляет 20—25 % (по объёму), тогда как дисперсноупрочненные композиты включают в себя от 1 до 15 % (по объёму) частиц размером от 0,01 до 0,1 мкм. Размеры частиц, входящих в состав нанокомпозитов — нового класса композиционных материалов — ещё меньше и составляют 10—100 нм.
Полимерные композитные материалы (ПКМ)
Композиты, в которых матрицей служит полимерный материал, являются одним из самых многочисленных и разнообразных видов материалов. Их применение в различных областях даёт значительный экономический эффект. Например, использование ПКМ при производстве космической и авиационной техники позволяет сэкономить от 5 до 30 % веса летательного аппарата. А снижение веса, например, искусственного спутника на околоземной орбите на 1 кг приводит к экономии 1000$. В качестве наполнителей ПКМ используется множество различных веществ.
А) Стеклопластики — полимерные композиционные материалы, армированные стеклянными волокнами, которые формируют из расплавленного неорганического стекла. В качестве матрицы чаще всего применяют как термореактивные синтетические смолы (фенольные, эпоксидные, полиэфирные и т. д.), так и термопластичные полимеры (полиамиды, полиэтилен, полистирол и т. д.). Эти материалы обладают достаточно высокой прочностью, низкой теплопроводностью, высокими электроизоляционными свойствами, кроме того, они прозрачны для радиоволн. Использование стеклопластиков началось в конце Второй мировой войны для изготовления антенных обтекателей — куполообразных конструкций, в которых размещается антенна локатора. В первых армированных стеклопластиках количество волокон было небольшим, волокно вводилось, главным образом, чтобы нейтрализовать грубые дефекты хрупкой матрицы. Однако со временем назначение матрицы изменилось — она стала служить только для склеивания прочных волокон между собой, содержание волокон во многих стеклопластиках достигает 80 % по массе. Слоистый материал, в котором в качестве наполнителя применяется ткань, плетённая из стеклянных волокон, называется стеклотекстолитом.
Стеклопластики — достаточно дешёвые материалы, их широко используют в строительстве, судостроении, радиоэлектронике, производстве бытовых предметов, спортивного инвентаря, оконных рам для современных стеклопакетов и т. п.
Б) Углепластики — наполнителем в этих полимерных композитах служат углеродные волокна. Углеродные волокна получают из синтетических и природных волокон на основе целлюлозы, сополимеров акрилонитрила, нефтяных и каменноугольных пеков и т. д. Термическая обработка волокна проводится, как правило, в три этапа (окисление — 220° С, карбонизация — 1000—1500° С и графитизация — 1800—3000° С) и приводит к образованию волокон, характеризующихся высоким содержанием (до 99,5 % по массе) углерода. В зависимости от режима обработки и исходного сырья полученное углеволокно имеет различную структуру. Для изготовления углепластиков используются те же матрицы, что и для стеклопластиков — чаще всего — термореактивные и термопластичные полимеры. Основными преимуществами углепластиков по сравнению со стеклопластиками является их низкая плотность и более высокий модуль упругости, углепластики — очень лёгкие и, в то же время, прочные материалы. Углеродные волокна и углепластики имеют практически нулевой коэффициент линейного расширения. Все углепластики хорошо проводят электричество, чёрного цвета, что несколько ограничивает области их применения. Углепластики используются в авиации, ракетостроении, машиностроении, производстве космической техники, медтехники, протезов, при изготовлении лёгких велосипедов и другого спортивного инвентаря.
На основе углеродных волокон и углеродной матрицы создают композитные углеграфитовые материалы — наиболее термостойкие композитные материалы (углеуглепластики), способные долго выдерживать в инертных или восстановительных средах температуры до 3000° С. Существует несколько способов производства подобных материалов. По одному из них углеродные волокна пропитывают фенолформальдегидной смолой, подвергая затем действию высоких температур (2000° С), при этом происходит пиролиз органических веществ и образуется углерод. Чтобы материал был менее пористым и более плотным, операцию повторяют несколько раз. Другой способ получения углеродного материала состоит в прокаливании обычного графита при высоких температурах в атмосфере метана. Мелкодисперсный углерод, образующийся при пиролизе метана, закрывает все поры в структуре графита. Плотность такого материала увеличивается по сравнению с плотностью графита в полтора раза. Из углеуглепластиков делают высокотемпературные узлы ракетной техники и скоростных самолётов, тормозные колодки и диски для скоростных самолётов и многоразовых космических кораблей, электротермическое оборудование.
В) Боропластики — композитные материалы, содержащие в качестве наполнителя борные волокна, внедрённые в термореактивную полимерную матрицу, при этом волокна могут быть как в виде мононитей, так и в виде жгутов, оплетённых вспомогательной стеклянной нитью или лентой, в которых борные нити переплетены с другими нитями. Благодаря большой твёрдости нитей, получающийся материал обладает высокими механическими свойствами (борные волокна имеют наибольшую прочность при сжатии по сравнению с волокнами из других материалов) и большой стойкостью к агрессивным условиям, но высокая хрупкость материала затрудняет их обработку и накладывает ограничения на форму изделий из боропластиков. Кроме того, стоимость борных волокон очень высока (порядка 400 $/кг) в связи с особенностями технологии их получения (бор осаждают из хлорида на вольфрамовую подложку, стоимость которой может достигать до 30 % стоимости волокна). Термические свойства боропластиков определяются термостойкостью матрицы, поэтому рабочие температуры, как правило, невелики.
Применение боропластиков ограничивается высокой стоимостью производства борных волокон, поэтому они используются главным образом в авиационной и космической технике в деталях, подвергающихся длительным нагрузкам в условиях агрессивной среды.
Г) Органопластики — композиты, в которых наполнителями служат органические синтетические, реже — природные и искусственные волокна в виде жгутов, нитей, тканей, бумаги и т. д. В термореактивных органопластиках матрицей служат, как правило, эпоксидные, полиэфирные и фенольные смолы, а также полиимиды. Материал содержит 40—70 % наполнителя. Содержание наполнителя в органопластиках на основе термопластичных полимеров — полиэтилена, ПВХ, полиуретана и т. п. — варьируется в значительно больших пределах — от 2 до 70 %. Органопластики обладают низкой плотностью, они легче стекло- и углепластиков, относительно высокой прочностью при растяжении; высоким сопротивлением удару и динамическим нагрузкам, но, в то же время, низкой прочностью при сжатии и изгибе.
Важную роль в улучшении механических характеристик органопластика играет степень ориентация макромолекул наполнителя. Макромолекулы жесткоцепных полимеров, таких, как полипарафенилтерефталамид (кевлар) в основном ориентированы в направлении оси полотна и поэтому обладают высокой прочностью при растяжении вдоль волокон. Из материалов, армированных кевларом, изготавливают пулезащитные бронежилеты.
Органопластики находят широкое применение в авто-, судо-, машиностроении, авиа- и космической технике, радиоэлектронике, химическом машиностроении, производстве спортивного инвентаря и т. д.
Д) Полимеры, наполненные порошками. Известно более 10000 марок наполненных полимеров. Наполнители используются как для снижения стоимости материала, так и для придания ему специальных свойств. Впервые наполненный полимер начал производить доктор Бейкеленд (Leo H.Baekeland, США), открывший в начале 20 в. способ синтеза фенолформальдегидной (бакелитовой) смолы. Сама по себе эта смола — вещество хрупкое, обладающее невысокой прочностью. Бейкеленд обнаружил, что добавка волокон, в частности, древесной муки к смоле до её затвердевания, увеличивает её прочность. Созданный им материал — бакелит — приобрёл большую популярность. Технология его приготовления проста: смесь частично отверждённого полимера и наполнителя — пресс-порошок — под давлением необратимо затвердевает в форме. Первое серийное изделие произведено по данной технологии в 1916, это — ручка переключателя скоростей автомобиля «Роллс-Ройс». Наполненные термореактивные полимеры широко используются по сей день.
Сейчас применяются разнообразные наполнители так термореактивных, так и термопластичных полимеров. Карбонат кальция и каолин (белая глина) дёшевы, запасы их практически не ограничены, белый цвет даёт возможность окрашивать материал. Применяют для изготовления жёстких и эластичных поливинилхлоридных материалов для производства труб, электроизоляции, облицовочных плиток и т. д., полиэфирных стеклопластиков, наполнения полиэтилена и полипропилена. Добавление талька в полипропилен существенно увеличивает модуль упругости и теплостойкость данного полимера. Сажа больше всего используется в качестве наполнителя резин, но вводится и в полиэтилен, полипропилен, полистирол и т. п. По-прежнему широко применяют органические наполнители — древесную муку, молотую скорлупу орехов, растительные и синтетические волокна. Большую популярность приобрел полимерно-песчаный композит на основе полиэтиленов с наполнителем из речного песка. Для создания биоразлагающихся композитов в качество наполнителя используют крахмал.
Е) Текстолиты — слоистые пластики, армированные тканями из различных волокон. Технология получения текстолитов была разработана в 1920-х на основе фенолформальдегидной смолы. Полотна ткани пропитывали смолой, затем прессовали при повышенной температуре, получая текстолитовые пластины. Роль одного из первых применений текстолитов — покрытия для кухонных столов — трудно переоценить.
Основные принципы получения текстолитов сохранились, но сейчас из них формуют не только пластины, но и фигурные изделия. И, конечно, расширился круг исходных материалов. Связующими в текстолитах является широкий круг термореактивных и термопластичных полимеров, иногда даже применяются и неорганические связующие — на основе силикатов и фосфатов. В качестве наполнителя используются ткани из самых разнообразных волокон — хлопковых, синтетических, стеклянных, углеродных, асбестовых, базальтовых и т. д. Соответственно разнообразны свойства и применение текстолитов.
Композитные материалы с металлической матрицей
При создании композитов на основе металлов в качестве матрицы применяют алюминий, магний, никель, медь и т. д. Наполнителем служат или высокопрочные волокна, или тугоплавкие, не растворяющиеся в основном металле частицы различной дисперсности.
Свойства дисперсноупрочненных металлических композитов изотропны — одинаковы во всех направлениях. Добавление 5-10% армирующих наполнителей (тугоплавких оксидов, нитридов, боридов, карбидов) приводит к повышению сопротивляемости матрицы нагрузкам. Эффект увеличения прочности сравнительно невелик, однако ценно увеличение жаропрочности композита по сравнению с исходной матрицей. Так, введение в жаропрочный хромоникелевый сплав тонкодисперсных порошков оксида тория или оксида циркония позволяет увеличить температуру, при которой изделия из этого сплава способны к длительной работе, с 1000° С до 1200° С. Дисперсноупрочненные металлические композиты получают, вводя порошок наполнителя в расплавленный металл, или методами порошковой металлургии.
Армирование металлов волокнами, нитевидными кристаллами, проволокой значительно повышает как прочность, так и жаростойкость металла. Например, сплавы алюминия, армированные волокнами бора, можно эксплуатировать при температурах до 450—500° С, вместо 250—300° С. Применяют оксидные, боридные, карбидные, нитридные металлические наполнители, углеродные волокна. Керамические и оксидные волокна из-за своей хрупкости не допускают пластическую деформацию материала, что создаёт значительные технологические трудности при изготовлении изделий, тогда как использование более пластичных металлических наполнителей позволяет переформование. Получают такие композиты пропитыванием пучков волокон расплавами металлов, электроосаждением, смешением с порошком металла и последующим спеканием и т. д.
В 1970-х появились первые материалы, армированные нитевидными монокристаллами («усами»). Нитевидные кристаллы получают, протягивая расплав через фильеры. Используются «усы» оксида алюминия, оксида бериллия, карбидов бора и кремния, нитридов алюминия и кремния и т. д. длиной 0,3-15 мм и диаметром 1-30 мкм. Армирование «усами» позволяет значительно увеличить прочность материала и повысить его жаростойкость. Например, предел текучести композита из серебра, содержащего 24% «усов» оксида алюминия, в 30 раз превышает предел текучести серебра и в 2 раза — других композиционных материалов на основе серебра. Армирование «усами» оксида алюминия материалов на основе вольфрама и молибдена вдвое увеличило их прочность при температуре 1650° С, что позволяет использовать эти материалы для изготовления сопел ракет.
Композитные материалы на основе керамики
Армирование керамических материалов волокнами, а также металлическими и керамическими дисперсными частицами позволяет получать высокопрочные композиты, однако, ассортимент волокон, пригодных для армирования керамики, ограничен свойствами исходного материала. Часто используют металлические волокна. Сопротивление растяжению растёт незначительно, но зато повышается сопротивление тепловым ударам — материал меньше растрескивается при нагревании, но возможны случаи, когда прочность материала падает. Это зависит от соотношения коэффициентов термического расширения матрицы и наполнителя.
Армирование керамики дисперсными металлическими частицами приводит к новым материалам (керметам) с повышенной стойкостью, устойчивостью относительно тепловых ударов, с повышенной теплопроводностью. Из высокотемпературных керметов делают детали для газовых турбин, арматуру электропечей, детали для ракетной и реактивной техники. Твёрдые износостойкие керметы используют для изготовления режущих инструментов и деталей. Кроме того, керметы применяют в специальных областях техники — это тепловыделяющие элементы атомных реакторов на основе оксида урана, фрикционные материалы для тормозных устройств и т. д.
Керамические композитные материалы получают методами горячего прессования (таблетирование с последующим спеканием под давлением) или методом шликерного литья (волокна заливаются суспензией матричного материала, которая после сушки также подвергается спеканию).
Примечания
Литература
- Кербер М. Л., Полимерные композиционные материалы. Структура. Свойства. Технологии. — СПб.: Профессия, 2008. — 560 с.
- Васильев В. В., Механика конструкций из композиционных материалов. — М.: Машиностроение, 1988. — 272 с.
- Карпинос Д. М., Композиционные материалы. Справочник. — Киев, Наукова думка
- СП 164.1325800.2014 Усиление железобетонных конструкций композитными материалами. Правила проектирования.
- Техническое заключение по результатам лабораторных испытаний арматурных выпусков из стеклопластика, установленных в монолитный бетон, на действие продольных относительно оси выпуска усилий // Tekhnicheskoe zaklyuchenie po rezul’tatam laboratornyh ispytaniy armaturnyh vypuskov iz stekloplastika, ustanovlennyh v monolitnyy beton, na deystvie prodol’nyh otnositel’no osi vypuska usiliy
- Высокопрочные системы усиления ITECWRAP/ITECRESIN. Екатеринбург: ООО НИИ Высокопрочные системы усиления ИНТЕР/ТЭК, 2010. 69 с. // Vysokoprochnye sistemy usileniya ITECWRAP/ITECRESIN. Yekaterinburg: OOO NII Vysokoprochnye sistemy usileniya INTER/TEK, 2010. 69.
- Коршунов, Я. Бурейская ГЭС: сверхпроектные работы/ Я. Коршунов // Газета «Вестник РусГидро».№ 4 — 2014. С.8. // Korshunov, Ya. Bureyskaya GES: sverhproektnye raboty/Ya. Korshunov//Gazeta «Vestnik RusGidro» #4-2014. P.8
- Усиление железобетонных конструкций (Пособие П 1-98 к СНиП 2.03.01-84*). Минск, 1998. // Usilenie zhelezobetonnyh konstrukciy (Posobie P 1-98 k SNiP 2.03.01-84*). Minsk, 1998.
- Хозин В. Г., Пискунов А. А., Гиздатуллин А. Р., Куклин А. Н.//Сцепление полимеркомпозитной арматуры с цементным бетоном / Известия КГАСУ № 1(23) — 2013. С.1-8
- Хозин В. Г., Пискунов А. А., Гиздатуллин А. Р., Куклин А. Н.//Сцепление полимеркомпозитной арматуры с цементным бетоном / Известия КГАСУ № 1(23) — 2013. С. 1-9
Ссылки
Композитный материал Википедия
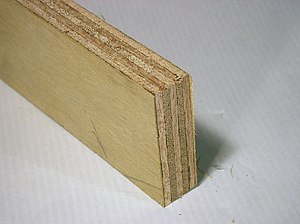
Композитный материа́л (КМ), компози́т — многокомпонентные материалы, состоящие, как правило, из пластичной основы (матрицы), армированной наполнителями, обладающими высокой прочностью, жёсткостью и т. д. Сочетание разнородных веществ приводит к созданию нового материала, свойства которого количественно и качественно отличаются от свойств каждого из его составляющих. Варьируя состав матрицы и наполнителя, их соотношение, ориентацию наполнителя, получают широкий спектр материалов с требуемым набором свойств. Многие композиты превосходят традиционные материалы и сплавы по своим механическим свойствам и в то же время они легче. Использование композитов обычно позволяет уменьшить массу конструкции при сохранении или улучшении её механических характеристик.
Структура композитных материалов[ | ]
По структуре композиты делятся на несколько основных классов: волокнистые, слоистые, дисперсноупрочненные, упрочнённые частицами и нанокомпозиты. Волокнистые композиты армированы волокнами или нитевидными кристаллами — кирпичи с соломой и папье-маше можно отнести как раз к этому классу композитов. Уже небольшое содержание наполнителя в композитах такого типа приводит к появлению качественно новых механических свойств материала. Широко варьировать свойства материала позволяет также изменение ориентации размера и концентрации волокон. Кроме того, армирование волокнами придаёт материалу анизотропию свойств (различие свойств в разных направлениях), а за счёт добавки волокон проводников можно придать материалу электропроводность вдоль заданной оси.
В слоистых композиционных материалах матрица и наполнитель расположены слоями, как, например, в особо прочном стекле, армированном несколькими слоями полимерных плёнок.
Микроструктура остальных классов композиционных материалов характеризуется тем, что матрицу наполняют частицами армирующего вещества, а различаются они размерами частиц. В композитах, упрочнённых частицами, их размер больше 1 мкм, а содержание составляет 20—25 % (по объёму), тогда как дисперсноупрочненные композиты включают в себя от 1 до 15 % (по объёму) частиц размером от 0,01 до 0,1 мкм. Размеры частиц, входящих в состав нанокомпозитов — нового класса композиционных материалов — ещё меньше и составляют 10—100 нм.
Полимерные композитные материалы (ПКМ)[ | ]
Композиты, в которых матрицей служит полимерный материал, являются одним из самых многочисленных и разнообразных видов материалов. Их применение в различных областях даёт значительный экономический эффект. Например, использование ПКМ при производстве космической и авиационной техники позволяет сэкономить от 5 до 30 % веса летательного аппарата. А снижение веса, например, искусственного спутника на околоземной орбите на 1 кг приводит к экономии 1000$. В качестве наполнителей ПКМ используется множество различных веществ.
А) Стеклопластики — полимерные композиционные материалы, армированные стеклянными волокнами, которые формируют из расплавленного неорганического стекла. В качестве матрицы чаще всего применяют как термореактивные синтетические смолы (фенольные, эпоксидные, полиэфирные и т. д.), так и термопластичные полимеры (полиамиды, полиэтилен, полистирол и т. д.). Эти материалы обладают достаточно высокой прочностью, низкой теплопроводностью, высокими электроизоляционными свойствами, кроме того, они прозрачны для радиоволн. Использование стеклопластиков началось в конце Второй мировой войны для изготовления антенных обтекателей — куполообразных конструкций, в которых размещается антенна локатора. В первых армированных стеклопластиках количество волокон было небольшим, волокно вводилось, главным образом, чтобы нейтрализовать грубые дефекты хрупкой матрицы. Однако со временем назначение матрицы изменилось — она стала служить только для склеивания прочных волокон между с
Композит Википедия
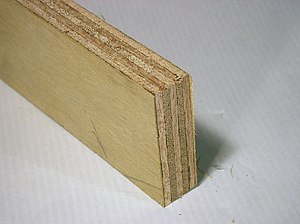
Композитный материа́л (КМ), компози́т — многокомпонентные материалы, состоящие, как правило, из пластичной основы (матрицы), армированной наполнителями, обладающими высокой прочностью, жёсткостью и т. д. Сочетание разнородных веществ приводит к созданию нового материала, свойства которого количественно и качественно отличаются от свойств каждого из его составляющих. Варьируя состав матрицы и наполнителя, их соотношение, ориентацию наполнителя, получают широкий спектр материалов с требуемым набором свойств. Многие композиты превосходят традиционные материалы и сплавы по своим механическим свойствам и в то же время они легче. Использование композитов обычно позволяет уменьшить массу конструкции при сохранении или улучшении её механических характеристик.
Структура композитных материалов[ | ]
По структуре композиты делятся на несколько основных классов: волокнистые, слоистые, дисперсноупрочненные, упрочнённые частицами и нанокомпозиты. Волокнистые композиты армированы волокнами или нитевидными кристаллами — кирпичи с соломой и папье-маше можно отнести как раз к этому классу композитов. Уже небольшое содержание наполнителя в композитах такого типа приводит к появлению качественно новых механических свойств материала. Широко варьировать свойства материала позволяет также изменение ориентации размера и концентрации волокон. Кроме того, армирование волокнами придаёт материалу анизотропию свойств (различие свойств в разных направлениях), а за счёт добавки волокон проводников можно придать материалу электропроводность вдоль заданной оси.
В слоистых композиционных материалах матрица и наполнитель расположены слоями, как, например, в особо прочном стекле, армированном несколькими слоями полимерных плёнок.
Микроструктура остальных классов композиционных материалов характеризуется тем, что матрицу наполняют частицами армирующего вещества, а различаются они размерами частиц. В композитах, упрочнённых частицами, их размер больше 1 мкм, а содержание составляет 20—25 % (по объёму), тогда как дисперсноупрочненные композиты включают в себя от 1 до 15 % (по объёму) частиц размером от 0,01 до 0,1 мкм. Размеры частиц, входящих в состав нанокомпозитов — нового класса композиционных материалов — ещё меньше и составляют 10—100 нм.
Полимерные композитные материалы (ПКМ)[ | ]
Композиты, в которых матрицей служит полимерный материал, являются одним из самых многочисленных и разнообразных видов материалов. Их применение в различных областях даёт значительный экономический эффект. Например, использование ПКМ при производстве космической и авиационной техники позволяет сэкономить от 5 до 30 % веса летательного аппарата. А снижение веса, например, искусственного спутника на околоземной орбите на 1 кг приводит к экономии 1000$. В качестве наполнителей ПКМ используется множество различных веществ.
А) Стеклопластики — полимерные композиционные материалы, армированные стеклянными волокнами, которые формируют из расплавленного неорганического стекла. В качестве матрицы чаще всего применяют как термореактивные синтетические смолы (фенольные, эпоксидные, полиэфирные и т. д.), так и термопластичные полимеры (полиамиды, полиэтилен, полистирол и т. д.). Эти материалы обладают достаточно высокой прочностью, низкой теплопроводностью, высокими электроизоляционными свойствами, кроме того, они прозрачны для радиоволн. Использование стеклопластиков началось в конце Второй мировой войны для изготовления антенных обтекателей — куполообразных конструкций, в которых размещается антенна локатора. В первых армированных стеклопластиках количество волокон было небольшим, волокно вводилось, главным образом, чтобы нейтрализовать грубые дефекты хрупкой матрицы. Однако со временем назначение матрицы изменилось — она стала служить только для склеивания прочных волокон между собой, содержание волокон во многих стеклопластиках достигает 80 % по массе. Слоистый материал, в котором в качестве наполнителя применяется ткань, плетённая из стеклянных волокон, называется стеклотекстолитом.
Стеклопластики — достаточно дешёвые материалы, их широко используют в строительстве, судостроении, радиоэлектронике, производстве бытовых предметов, спортивного инвентаря, оконных рам для современных стеклопакетов и т. п.
Б) Углепластики — наполнителем в этих полимерных композитах служат углеродные волокна. Углеродные волокна получают из синтетических и природных волокон на основе целлюлозы, сополимеров акрилонитрила, нефтяных и каменноугольных пеков и т. д. Термическая обработка волокна проводится, как правило, в три этапа
Композиционный материал Википедия
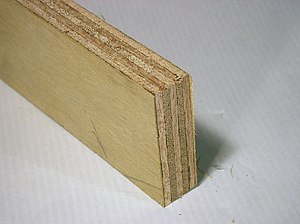
Композитный материа́л (КМ), компози́т — многокомпонентные материалы, состоящие, как правило, из пластичной основы (матрицы), армированной наполнителями, обладающими высокой прочностью, жёсткостью и т. д. Сочетание разнородных веществ приводит к созданию нового материала, свойства которого количественно и качественно отличаются от свойств каждого из его составляющих. Варьируя состав матрицы и наполнителя, их соотношение, ориентацию наполнителя, получают широкий спектр материалов с требуемым набором свойств. Многие композиты превосходят традиционные материалы и сплавы по своим механическим свойствам и в то же время они легче. Использование композитов обычно позволяет уменьшить массу конструкции при сохранении или улучшении её механических характеристик.
Структура композитных материалов[ | ]
По структуре композиты делятся на несколько основных классов: волокнистые, слоистые, дисперсноупрочненные, упрочнённые частицами и нанокомпозиты. Волокнистые композиты армированы волокнами или нитевидными кристаллами — кирпичи с соломой и папье-маше можно отнести как раз к этому классу композитов. Уже небольшое содержание наполнителя в композитах такого типа приводит к появлению качественно новых механических свойств материала. Широко варьировать свойства материала позволяет также изменение ориентации размера и концентрации волокон. Кроме того, армирование волокнами придаёт материалу анизотропию свойств (различие свойств в разных направлениях), а за счёт добавки волокон проводников можно придать материалу электропроводность вдоль заданной оси.
В слоистых композиционных материалах матрица и наполнитель расположены слоями, как, например, в особо прочном стекле, армированном несколькими слоями полимерных плёнок.
Микроструктура остальных классов композиционных материалов характеризуется тем, что матрицу наполняют частицами армирующего вещества, а различаются они размерами частиц. В композитах, упрочнённых частицами, их размер больше 1 мкм, а содержание составляет 20—25 % (по объёму), тогда как дисперсноупрочненные композиты включают в себя от 1 до 15 % (по объёму) частиц размером от 0,01 до 0,1 мкм. Размеры частиц, входящих в состав нанокомпозитов — нового класса композиционных материалов — ещё меньше и составляют 10—100 нм.
Полимерные композитные материалы (ПКМ)[ | ]
Композиты, в которых матрицей служит полимерный материал, являются одним из самых многочисленных и разнообразных видов материалов. Их применение в различных областях даёт значительный экономический эффект. Например, использование ПКМ при производстве космической и авиационной техники позволяет сэкономить от 5 до 30 % веса летательного аппарата. А снижение веса, например, искусственного спутника на околоземной орбите на 1 кг приводит к экономии 1000$. В качестве наполнителей ПКМ используется множество различных веществ.
А) Стеклопластики — полимерные композиционные материалы, армированные стеклянными волокнами, которые формируют из расплавленного неорганического стекла. В качестве матрицы чаще всего применяют как термореактивные синтетические смолы (фенольные, эпоксидные, полиэфирные и т. д.), так и термопластичные полимеры (полиамиды, полиэтилен, полистирол и т. д.). Эти материалы обладают достаточно высокой прочностью, низкой теплопроводностью, высокими электроизоляционными свойствами, кроме того, они прозрачны для радиоволн. Использование стеклопластиков началось в конце Второй мировой войны для изготовления антенных обтекателей — куполообразных конструкций, в которых размещается антенна локатора. В первых армированных стеклопластиках количество волокон было небольшим, волокно вводилось, главным образом, чтобы нейтрализовать грубые дефекты хрупкой матрицы. Однако со временем назначение матрицы изменилось — она стала служить только для склеивания прочных волокон между собой, содержание волокон во многих стеклопластиках достигает 80 % по массе. Слоистый материал, в котором в качестве наполнителя применяется ткань, плетённая из стеклянных волокон, называется стеклотекстолитом.
Стеклопластики — достаточно дешёвые материалы, их широко используют в строительстве, судостроении, радиоэлектронике, производстве бытовых предметов, спортивного инвентаря, оконных рам для современных стеклопакетов и т. п.
Б) Углепластики — наполнителем в этих полимерных композитах служат углеродные волокна. Углеродные волокна получают из синтетических и природных волокон на основе целлюлозы, сополимеров акрилонитрила, нефтяных и каменноугольных пеков и т.
Композиционный материал — Википедия. Что такое Композиционный материал
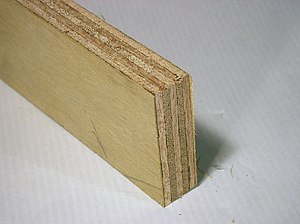
Композитный материа́л (КМ), компози́т — многокомпонентные материалы, состоящие, как правило, из пластичной основы (матрицы), армированной наполнителями, обладающими высокой прочностью, жёсткостью и т. д. Сочетание разнородных веществ приводит к созданию нового материала, свойства которого количественно и качественно отличаются от свойств каждого из его составляющих. Варьируя состав матрицы и наполнителя, их соотношение, ориентацию наполнителя, получают широкий спектр материалов с требуемым набором свойств. Многие композиты превосходят традиционные материалы и сплавы по своим механическим свойствам и в то же время они легче. Использование композитов обычно позволяет уменьшить массу конструкции при сохранении или улучшении её механических характеристик.
Структура композитных материалов
По структуре композиты делятся на несколько основных классов: волокнистые, слоистые, дисперсноупрочненные, упрочненные частицами и нанокомпозиты. Волокнистые композиты армированы волокнами или нитевидными кристаллами — кирпичи с соломой и папье-маше можно отнести как раз к этому классу композитов. Уже небольшое содержание наполнителя в композитах такого типа приводит к появлению качественно новых механических свойств материала. Широко варьировать свойства материала позволяет также изменение ориентации размера и концентрации волокон. Кроме того, армирование волокнами придаёт материалу анизотропию свойств (различие свойств в разных направлениях), а за счёт добавки волокон проводников можно придать материалу электропроводность вдоль заданной оси.
В слоистых композиционных материалах матрица и наполнитель расположены слоями, как, например, в особо прочном стекле, армированном несколькими слоями полимерных плёнок.
Микроструктура остальных классов композиционных материалов характеризуется тем, что матрицу наполняют частицами армирующего вещества, а различаются они размерами частиц. В композитах, упрочнённых частицами, их размер больше 1 мкм, а содержание составляет 20—25 % (по объёму), тогда как дисперсноупрочненные композиты включают в себя от 1 до 15 % (по объёму) частиц размером от 0,01 до 0,1 мкм. Размеры частиц, входящих в состав нанокомпозитов — нового класса композиционных материалов — ещё меньше и составляют 10—100 нм.
Полимерные композитные материалы (ПКМ)
Композиты, в которых матрицей служит полимерный материал, являются одним из самых многочисленных и разнообразных видов материалов. Их применение в различных областях даёт значительный экономический эффект. Например, использование ПКМ при производстве космической и авиационной техники позволяет сэкономить от 5 до 30 % веса летательного аппарата. А снижение веса, например, искусственного спутника на околоземной орбите на 1 кг приводит к экономии 1000$. В качестве наполнителей ПКМ используется множество различных веществ.
А) Стеклопластики — полимерные композиционные материалы, армированные стеклянными волокнами, которые формуют из расплавленного неорганического стекла. В качестве матрицы чаще всего применяют как термореактивные синтетические смолы (фенольные, эпоксидные, полиэфирные и т. д.), так и термопластичные полимеры (полиамиды, полиэтилен, полистирол и т. д.). Эти материалы обладают достаточно высокой прочностью, низкой теплопроводностью, высокими электроизоляционными свойствами, кроме того, они прозрачны для радиоволн. Использование стеклопластиков началось в конце Второй мировой войны для изготовления антенных обтекателей — куполообразных конструкций, в которых размещается антенна локатора. В первых армированных стеклопластиках количество волокон было небольшим, волокно вводилось, главным образом, чтобы нейтрализовать грубые дефекты хрупкой матрицы. Однако со временем назначение матрицы изменилось — она стала служить только для склеивания прочных волокон между собой, содержание волокон во многих стеклопластиках достигает 80 % по массе. Слоистый материал, в котором в качестве наполнителя применяется ткань, плетенная из стеклянных волокон, называется стеклотекстолитом.
Стеклопластики — достаточно дешёвые материалы, их широко используют в строительстве, судостроении, радиоэлектронике, производстве бытовых предметов, спортивного инвентаря, оконных рам для современных стеклопакетов и т. п.
Б) Углепластики — наполнителем в этих полимерных композитах служат углеродные волокна. Углеродные волокна получают из синтетических и природных волокон на основе целлюлозы, сополимеров акрилонитрила, нефтяных и каменноугольных пеков и т. д. Термическая обработка волокна проводится, как правило, в три этапа (окисление — 220° С, карбонизация — 1000—1500° С и графитизация — 1800—3000° С) и приводит к образованию волокон, характеризующихся высоким содержанием (до 99,5 % по массе) углерода. В зависимости от режима обработки и исходного сырья полученное углеволокно имеет различную структуру. Для изготовления углепластиков используются те же матрицы, что и для стеклопластиков — чаще всего — термореактивные и термопластичные полимеры. Основными преимуществами углепластиков по сравнению со стеклопластиками является их низкая плотность и более высокий модуль упругости, углепластики — очень лёгкие и, в то же время, прочные материалы. Углеродные волокна и углепластики имеют практически нулевой коэффициент линейного расширения. Все углепластики хорошо проводят электричество, чёрного цвета, что несколько ограничивает области их применения. Углепластики используются в авиации, ракетостроении, машиностроении, производстве космической техники, медтехники, протезов, при изготовлении лёгких велосипедов и другого спортивного инвентаря.
На основе углеродных волокон и углеродной матрицы создают композитные углеграфитовые материалы — наиболее термостойкие композитные материалы (углеуглепластики), способные долго выдерживать в инертных или восстановительных средах температуры до 3000° С. Существует несколько способов производства подобных материалов. По одному из них углеродные волокна пропитывают фенолформальдегидной смолой, подвергая затем действию высоких температур (2000° С), при этом происходит пиролиз органических веществ и образуется углерод. Чтобы материал был менее пористым и более плотным, операцию повторяют несколько раз. Другой способ получения углеродного материала состоит в прокаливании обычного графита при высоких температурах в атмосфере метана. Мелкодисперсный углерод, образующийся при пиролизе метана, закрывает все поры в структуре графита. Плотность такого материала увеличивается по сравнению с плотностью графита в полтора раза. Из углеуглепластиков делают высокотемпературные узлы ракетной техники и скоростных самолётов, тормозные колодки и диски для скоростных самолётов и многоразовых космических кораблей, электротермическое оборудование.
В) Боропластики — композитные материалы, содержащие в качестве наполнителя борные волокна, внедрённые в термореактивную полимерную матрицу, при этом волокна могут быть как в виде мононитей, так и в виде жгутов, оплетённых вспомогательной стеклянной нитью или лентой, в которых борные нити переплетены с другими нитями. Благодаря большой твёрдости нитей, получающийся материал обладает высокими механическими свойствами (борные волокна имеют наибольшую прочность при сжатии по сравнению с волокнами из других материалов) и большой стойкостью к агрессивным условиям, но высокая хрупкость материала затрудняет их обработку и накладывает ограничения на форму изделий из боропластиков. Кроме того, стоимость борных волокон очень высока (порядка 400 $/кг) в связи с особенностями технологии их получения (бор осаждают из хлорида на вольфрамовую подложку, стоимость которой может достигать до 30 % стоимости волокна). Термические свойства боропластиков определяются термостойкостью матрицы, поэтому рабочие температуры, как правило, невелики.
Применение боропластиков ограничивается высокой стоимостью производства борных волокон, поэтому они используются главным образом в авиационной и космической технике в деталях, подвергающихся длительным нагрузкам в условиях агрессивной среды.
Г) Органопластики — композиты, в которых наполнителями служат органические синтетические, реже — природные и искусственные волокна в виде жгутов, нитей, тканей, бумаги и т. д. В термореактивных органопластиках матрицей служат, как правило, эпоксидные, полиэфирные и фенольные смолы, а также полиимиды. Материал содержит 40—70 % наполнителя. Содержание наполнителя в органопластиках на основе термопластичных полимеров — полиэтилена, ПВХ, полиуретана и т. п. — варьируется в значительно больших пределах — от 2 до 70 %. Органопластики обладают низкой плотностью, они легче стекло- и углепластиков, относительно высокой прочностью при растяжении; высоким сопротивлением удару и динамическим нагрузкам, но, в то же время, низкой прочностью при сжатии и изгибе.
Важную роль в улучшении механических характеристик органопластика играет степень ориентация макромолекул наполнителя. Макромолекулы жесткоцепных полимеров, таких, как полипарафенилтерефталамид (кевлар) в основном ориентированы в направлении оси полотна и поэтому обладают высокой прочностью при растяжении вдоль волокон. Из материалов, армированных кевларом, изготавливают пулезащитные бронежилеты.
Органопластики находят широкое применение в авто-, судо-, машиностроении, авиа- и космической технике, радиоэлектронике, химическом машиностроении, производстве спортивного инвентаря и т. д.
Д) Полимеры, наполненные порошками. Известно более 10000 марок наполненных полимеров. Наполнители используются как для снижения стоимости материала, так и для придания ему специальных свойств. Впервые наполненный полимер начал производить доктор Бейкеленд (Leo H.Baekeland, США), открывший в начале 20 в. способ синтеза фенолформальдегидной (бакелитовой) смолы. Сама по себе эта смола — вещество хрупкое, обладающее невысокой прочностью. Бейкеленд обнаружил, что добавка волокон, в частности, древесной муки к смоле до её затвердевания, увеличивает её прочность. Созданный им материал — бакелит — приобрёл большую популярность. Технология его приготовления проста: смесь частично отвержденного полимера и наполнителя — пресс-порошок — под давлением необратимо затвердевает в форме. Первое серийное изделие произведено по данной технологии в 1916, это — ручка переключателя скоростей автомобиля «Роллс-Ройс». Наполненные термореактивные полимеры широко используются по сей день.
Сейчас применяются разнообразные наполнители так термореактивных, так и термопластичных полимеров. Карбонат кальция и каолин (белая глина) дёшевы, запасы их практически не ограничены, белый цвет даёт возможность окрашивать материал. Применяют для изготовления жёстких и эластичных поливинилхлоридных материалов для производства труб, электроизоляции, облицовочных плиток и т. д., полиэфирных стеклопластиков, наполнения полиэтилена и полипропилена. Добавление талька в полипропилен существенно увеличивает модуль упругости и теплостойкость данного полимера. Сажа больше всего используется в качестве наполнителя резин, но вводится и в полиэтилен, полипропилен, полистирол и т. п. По-прежнему широко применяют органические наполнители — древесную муку, молотую скорлупу орехов, растительные и синтетические волокна. Для создания биоразлагающихся композитов в качество наполнителя используют крахмал.
Е) Текстолиты — слоистые пластики, армированные тканями из различных волокон. Технология получения текстолитов была разработана в 1920-х на основе фенолформальдегидной смолы. Полотна ткани пропитывали смолой, затем прессовали при повышенной температуре, получая текстолитовые пластины. Роль одного из первых применений текстолитов — покрытия для кухонных столов — трудно переоценить.
Основные принципы получения текстолитов сохранились, но сейчас из них формуют не только пластины, но и фигурные изделия. И, конечно, расширился круг исходных материалов. Связующими в текстолитах является широкий круг термореактивных и термопластичных полимеров, иногда даже применяются и неорганические связующие — на основе силикатов и фосфатов. В качестве наполнителя используются ткани из самых разнообразных волокон — хлопковых, синтетических, стеклянных, углеродных, асбестовых, базальтовых и т. д. Соответственно разнообразны свойства и применение текстолитов.
Композитные материалы с металлической матрицей
При создании композитов на основе металлов в качестве матрицы применяют алюминий, магний, никель, медь и т. д. Наполнителем служат или высокопрочные волокна, или тугоплавкие, не растворяющиеся в основном металле частицы различной дисперсности.
Свойства дисперсноупрочненных металлических композитов изотропны -одинаковы во всех направлениях. Добавление 5-10 % армирующих наполнителей (тугоплавких оксидов, нитридов, боридов, карбидов) приводит к повышению сопротивляемости матрицы нагрузкам. Эффект увеличения прочности сравнительно невелик, однако ценно увеличение жаропрочности композита по сравнению с исходной матрицей. Так, введение в жаропрочный хромоникелевый сплав тонкодисперсных порошков оксида тория или оксида циркония позволяет увеличить температуру, при которой изделия из этого сплава способны к длительной работе, с 1000° С до 1200° С. Дисперсноупрочненные металлические композиты получают, вводя порошок наполнителя в расплавленный металл, или методами порошковой металлургии.
Армирование металлов волокнами, нитевидными кристаллами, проволокой значительно повышает как прочность, так и жаростойкость металла. Например, сплавы алюминия, армированные волокнами бора, можно эксплуатировать при температурах до 450—500° С, вместо 250—300° С. Применяют оксидные, боридные, карбидные, нитридные металлические наполнители, углеродные волокна. Керамические и оксидные волокна из-за своей хрупкости не допускают пластическую деформацию материала, что создаёт значительные технологические трудности при изготовлении изделий, тогда как использование более пластичных металлических наполнителей позволяет переформование. Получают такие композиты пропитыванием пучков волокон расплавами металлов, электроосаждением, смешением с порошком металла и последующим спеканием и т. д.
В 1970-х появились первые материалы, армированные нитевидными монокристаллами («усами»). Нитевидные кристаллы получают, протягивая расплав через фильеры. Используются «усы» оксида алюминия, оксида бериллия, карбидов бора и кремния, нитридов алюминия и кремния и т. д. длиной 0,3-15 мм и диаметром 1-30 мкм. Армирование «усами» позволяет значительно увеличить прочность материала и повысить его жаростойкость. Например, предел текучести композита из серебра, содержащего 24 % «усов» оксида алюминия, в 30 раз превышает предел текучести серебра и в 2 раза — других композиционных материалов на основе серебра. Армирование «усами» оксида алюминия материалов на основе вольфрама и молибдена вдвое увеличило их прочность при температуре 1650° С, что позволяет использовать эти материалы для изготовления сопел ракет.
Композитные материалы на основе керамики
Армирование керамических материалов волокнами, а также металлическими и керамическими дисперсными частицами позволяет получать высокопрочные композиты, однако, ассортимент волокон, пригодных для армирования керамики, ограничен свойствами исходного материала. Часто используют металлические волокна. Сопротивление растяжению растёт незначительно, но зато повышается сопротивление тепловым ударам — материал меньше растрескивается при нагревании, но возможны случаи, когда прочность материала падает. Это зависит от соотношения коэффициентов термического расширения матрицы и наполнителя.
Армирование керамики дисперсными металлическими частицами приводит к новым материалам (керметам) с повышенной стойкостью, устойчивостью относительно тепловых ударов, с повышенной теплопроводностью. Из высокотемпературных керметов делают детали для газовых турбин, арматуру электропечей, детали для ракетной и реактивной техники. Твёрдые износостойкие керметы используют для изготовления режущих инструментов и деталей. Кроме того, керметы применяют в специальных областях техники — это тепловыделяющие элементы атомных реакторов на основе оксида урана, фрикционные материалы для тормозных устройств и т. д.
Керамические композитные материалы получают методами горячего прессования (таблетирование с последующим спеканием под давлением) или методом шликерного литья (волокна заливаются суспензией матричного материала, которая после сушки также подвергается спеканию).
Примечания
Литература
- Кербер М. Л., Полимерные композиционные материалы. Структура. Свойства. Технологии. — СПб.: Профессия, 2008. — 560 с.
- Васильев В. В., Механика конструкций из композиционных материалов. — М.: Машиностроение, 1988. — 272 с.
- Карпинос Д. М., Композиционные материалы. Справочник. — Киев, Наукова думка
- СП 164.1325800.2014 Усиление железобетонных конструкций композитными материалами. Правила проектирования.
- Техническое заключение по результатам лабораторных испытаний арматурных выпусков из стеклопластика, установленных в монолитный бетон, на действие продольных относительно оси выпуска усилий // Tekhnicheskoe zaklyuchenie po rezul’tatam laboratornyh ispytaniy armaturnyh vypuskov iz stekloplastika, ustanovlennyh v monolitnyy beton, na deystvie prodol’nyh otnositel’no osi vypuska usiliy
- Высокопрочные системы усиления ITECWRAP/ITECRESIN. Екатеринбург: ООО НИИ Высокопрочные системы усиления ИНТЕР/ТЭК, 2010. 69 с. // Vysokoprochnye sistemy usileniya ITECWRAP/ITECRESIN. Yekaterinburg: OOO NII Vysokoprochnye sistemy usileniya INTER/TEK, 2010. 69.
- Коршунов, Я. Бурейская ГЭС: сверхпроектные работы/ Я. Коршунов // Газета «Вестник РусГидро».№ 4 — 2014. С.8. // Korshunov, Ya. Bureyskaya GES: sverhproektnye raboty/Ya. Korshunov//Gazeta «Vestnik RusGidro» #4-2014. P.8
- Усиление железобетонных конструкций (Пособие П 1-98 к СНиП 2.03.01-84*). Минск, 1998. // Usilenie zhelezobetonnyh konstrukciy (Posobie P 1-98 k SNiP 2.03.01-84*). Minsk, 1998.
- Хозин В. Г., Пискунов А. А., Гиздатуллин А. Р., Куклин А. Н.//Сцепление полимеркомпозитной арматуры с цементным бетоном / Известия КГАСУ № 1(23) — 2013. С.1-8
- Хозин В. Г., Пискунов А. А., Гиздатуллин А. Р., Куклин А. Н.//Сцепление полимеркомпозитной арматуры с цементным бетоном / Известия КГАСУ № 1(23) — 2013. С. 1-8
Ссылки
Композитный материал что это такое | Материалы
композитный материал что это такое
Композиционный материал это:
Композицио́нный материа́л (компози́т, КМ )#160 — искусственно созданный неоднородный сплошной материал, состоящий из двух или более компонентов с четкой границей раздела между ними. В большинстве композитов (за исключением слоистых) компоненты можно разделить на матрицу и включенные в нее армирующие элементы. В композитах конструкционного назначения армирующие элементы обычно обеспечивают необходимые механические характеристики материала (прочность, жесткость и т.д.), а матрица (или связующее) обеспечивает совместную работу армирующих элементов и защиту их от механических повреждений и агрессивной химической среды.
Механическое поведение композиции определяется соотношением свойств армирующих элементов и матрицы, а также прочностью связи между ними. Эффективность и работоспособность материала зависят от правильного выбора исходных компонентов и технологии их совмещения, призванной обеспечить прочную связь между компонентами при сохранении их первоначальных характеристик.
В результате совмещения армирующих элементов и матрицы образуется комплекс свойств композиции, не только отражающий исходные характеристики его компонентов, но и включающий свойства, которыми изолированные компоненты не обладают. В частности, наличие границ раздела между армирующими элементами и матрицей существенно повышает трещиностойкость материала, и в композициях, в отличие от однородных металлов. повышение статической прочности приводит не к снижению, а, как правило, к повышению характеристик вязкости разрушения.
Для создания композиции используются самые разные армирующие наполнители и матрицы. Это#160 — гетинакс и текстолит (слоистые пластики из бумаги или ткани, склеенной термореактивным клеем), стекло- и графитопласт (ткань или намотанное волокно из стекла или графита, пропитанные эпоксидными клеями), фанера … Есть материалы, в которых тонкое волокно из высокопрочных сплавов залито алюминиевой массой. Булат #160 — один из древнейших композиционных материалов. В нем тончайшие слои (иногда нити) высокоуглеродистой стали «склеены» мягким низкоуглеродным железом.
В последнее время материаловеды экспериментируют с целью создать более удобные в производстве, а значит#160 — и более дешёвые материалы. Исследуются саморастущие кристаллические структуры, склеенные в единую массу полимерным клеем (цементы с добавками водорастворимых клеев), композиции из термопласта с короткими армирующими волоконцами и пр.
Содержание
Классификация композитов
Преимущества композиционных материалов
Главное преимущество КМ в том, что материал и конструкция создается одновременно. Исключением являются препреги. которые являются полуфабрикатом для изготовления конструкций. Стоит сразу оговорить, что КМ создаются под выполнение данных задач, соответственно не могут вмещать в себя все возможные преимущества, но, проектируя новый композит, инженер волен задать ему характеристики значительно превосходящие характеристики традиционных материалов при выполнении данной цели в данном механизме, но уступающие им в каких-либо других аспектах. Это значит, что КМ не может быть лучше традиционного материала во всём, то есть для каждого изделия инженер проводит все необходимые расчёты и только потом выбирает оптимум между материалами для производства.
Причём, разные классы композитов могут обладать одним или несколькими преимуществами. Некоторых преимуществ невозможно добиться одновременно.
Недостатки композиционных материалов
Композиционные материалы имеют достаточно большое количество недостатков, которые сдерживают их распространение.
Высокая стоимость
Высокая стоимость КМ обусловлена высокой наукоёмкостью производства, необходимостью применения специального дорогостоящего оборудования и сырья, а следовательно развитого промышленного производства и научной базы страны.
Анизотропия свойств
Анизотропия — непостоянство свойств КМ от образца к образцу. Для компенсации анизотропии увеличивают коэффициент запаса прочности, что может нивелировать преимущество КМ в удельной прочности. Таким примером может служить опыт применения КМ при изготовлении вертикального оперения истребителя МиГ-29. Из-за анизотропии применявшегося КМ вертикальное оперение было спроектировано с коэффициентом запаса прочности кратно превосходящим стандартный в авиации коэффициент 1,5, что в итоге привело к тому, что композитное вертикальное оперение Миг-29 оказалось равным по весу конструкции классического вертикального оперения, сделанного из дюралюминия .
Низкая ударная вязкость
Низкая ударная вязкость также является причиной повышения коэффициента запаса прочности. Кроме этого, низкая ударная вязкость обуславливает высокую повреждаемость изделий из КМ, высокую вероятность возникновения скрытых дефектов, которые могут быть выявлены только инструментальными методами контроля .
Высокий удельный объем
Высокий удельный объем является существенным недостатком при применении КМ в областях с жесткими ограничениями по занимаемому объему. Это относится, например, к сверхзвуковым самолётам. у которых даже незначительное увеличение объема самолёта приводит к существенному росту волнового аэродинамического сопротивления .
Гигроскопичность
Композиционные материалы гигроскопичны. т.е. склонны впитывать влагу, что обусловлено несплошностью внутренней структуры КМ. При длительной эксплуатации и многократном переходе температуры через 0 по Цельсию вода, проникающая в структуру КМ, разрушает изделие из КМ изнутри (эффект по природе аналогичен разрушению автомобильных дорог в межсезонье). Так одной из возможных причин авиакатастрофы American Airlines Flight 587. в которой от фюзеляжа оторвался композитный киль, названо разрушение структуры композитного киля от периодически замерзавшей в ней воды. Аналогичные примеры отделения композитного киля от фюзеляжа происходили также в России. [2]
КМ могут впитывать также другие жидкости, обладающие высокой проникающей способностью, например, авиационный керосин .
Токсичность
При эксплуатации КМ могут выделять пары, которые часто являются токсичными. Если из КМ изготавливают изделия, которые будут располагаться в непосредственной близости от человека (таким примером может послужить композитный фюзеляж самолета Boeing 787 Dreamliner ), то для одобрения применяемых при изготовлении КМ материалов требуются дополнительные исследования воздействия компонентов КМ на человека.
Низкая эксплуатационная технологичность
Композиционные материалы обладают низкой эксплуатационной технологичностью. низкой ремонтопригодностью и высокой стоимостью эксплуатации. Это связано с необходимостью применения специальных трудоемких методов, специальных инструментов для доработки и ремонта объектов из КМ. Часто объекты из КМ вообще не подлежат какой-либо доработке и ремонту.
Области применения
Товары широкого потребления
Что такое композитный материал
Сегодня композитными материалами пользуются в различных отраслях промышленности, начиная производство бытовых предметов, заканчивая космическими ракетами. Благодаря их плотности, прочности и другим техническим характеристикам появилась возможность их использования в местах с экстремальными условиями. Что представляет собой композитные материалы?
Композитами называют сплошные неоднородные материалы, которые искусственно создаются с использованием нескольких компонентов имеющих различные физические и химические свойства. Механические свойства композитных материалов определяются соотношение характеристик армирующих элементов и матрицы, прочностью их связи, обеспечиваемой правильным выбором исходных компонентов и способов с которыми они совмещаются.
Чаще всего к композитам относят материалы, основанные на смоле или полимерных матрицах. Для изготовления этих материалов пользуются фенольными, эпоксидными, винилэфирными, полиэфирными, а также полипропиленовыми полимерами. В качестве армирующих веществ для изготовления композитов пользуются сыпучими веществами и волокнами. Прочность материала определяется количеством смолы. Чем меньше ее количество, тем он будет прочнее. Сегодня чтобы получить идеальные пропорции всех компонентов происходит постоянное совершенствование технологий формирования композитного материала.
При формовании матрицу композитного материала объединяют с армирующим веществом, для изготовления того или иного изделия. Термореактивными полимерными матрицами в ходе формования испытывается химическая реакция отверждения. При формовании происходит расплавление термопластичных полимерных матриц и их застывание в форме, которая задана. Обычно данный процесс происходит при комнатной температуре и нормальном давлении.
Кроме того часто пользуются контактным (ручным) формованием, имеющим ряд серьезных минусов. В изделии, которое сформовано с помощью этого способа, содержится много смолы, что приводит к его хрупкости. Помимо этого, в данном случае сложно получить матрицу и армирующее с идеальными пропорциями, а также сохранить толщину изделия, без образования воздушных ходов внутри.
При вакуумном формовании используют открытую оснастку, в которой размещают композитные компоненты, которые накрывают, используя полимерную пленку или силиконовую мембрану. Далее на оснастку при атмосферном давлении и высокой температуре накладывается вакуум.
Статья была опубликована: 28-08-, 15:17
Что такое композиты?
Композиты — многокомпонентные материалы, состоящие из полимерной, металлической, углеродной, керамической или другой основы (матрицы), армированной наполнителями из волокон, нитевидных кристаллов, тонкодиспeрсных частиц и др. Путем подбора состава и свойств наполнителя и матрицы, их соотношения, ориентации наполнителя можно получить материалы с требуемым сочетанием эксплуатационных и технологических свойств. Использование в одном материале нескольких матриц (полиматричные композитные материалы) или наполнителей различной природы (гибридные композитные материалы) значительно расширяет возможности регулирования свойств композитных материалов. Армирующие наполнители воспринимают основную долю нагрузки композитных материалов.
По структуре наполнителя композитные материалы подразделяют на волокнистые (армированы волокнами и нитевидными кристаллами), слоистые (армированы пленками, пластинками, слоистыми наполнителями), дисперсноармированные, или дисперсноупрочненные (с наполнителем в виде тонкодисперсных частиц). Матрица в композитных материалах обеспечивает монолитность материала, передачу и распределение напряжения в наполнителе, определяет тепло-, влаго-, огне- и химическую стойкость.
По природе матричного материала различают полимерные, металлические, углеродные, керамические и другие композиты.
Наиболее широкое применение в технике получили композитные материалы, армированные высокопрочными и высокомодульными непрерывными волокнами. К ним относят:
— полимерные композитные материалы на основе термореактивных (эпоксидных, полиэфирных, винилэфирных, феноло-формальдегидных, полиимидных и др.) и термопластичных смол, армированных стеклянными (стеклокомпозиты), углеродными (углекомпозиты), органическими (органокомпозиты), борными (борокомпозиты) и другими видами волокон
— металлические композитные материалы на основе сплавов Al, Mg, Cu, Ti, Ni, Сг, армированных борными, углеродными или карбидкремниевыми волокнами, а также стальной, молибденовой или вольфрамовой проволокой
— композитные материалы на основе углерода, армированного углеродными волокнами (углерод-углеродные материалы)
— композитные материалы на основе керамики, армированной углеродными, карбидкремниевыми и другими жаростойкими волокнами.
При использовании углеродных, стеклянных, арамидных и борных волокон, содержащихся в материале в количестве 50-70%, созданы композиции с ударной прочностью и ударным модулем упругости в 2-5 раз большими, чем у обычных конструкционных материалов и сплавов. Кроме того, волокнистые композитные материалы превосходят металлы и сплавы по усталостной прочности, термостойкости, виброустойчивости, шумопоглощению, ударной вязкости и другим свойствам.
Источники: http://dic.academic.ru/dic.nsf/ruwiki/7078, http://www.campingmanitoulin.com/stroymaterialy/3654-chto-takoe-kompozitnyy-material.html, http://www.uncm.ru/Page308.html
Комментарии: 1